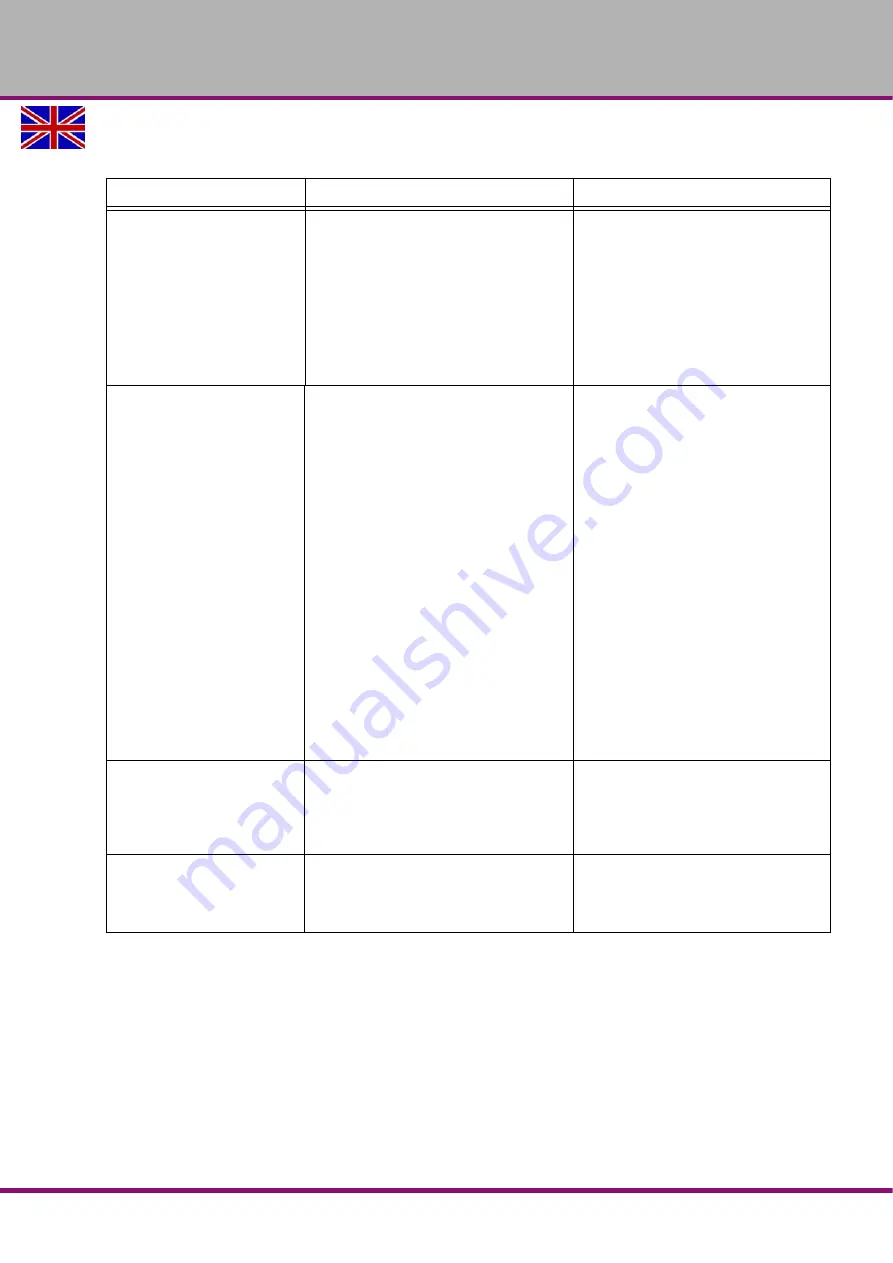
Malfunctions
Version 1.0.9 dated 2019-05-13
Page 59
Translation of the original instructions
GH 10T | GH 15T
GB
GH10T_G
H15T_G
B_4-
1.f
m
OPTIMUM
M A S C H I N E N - G E R M A N Y
®
5
Malfunctions
Malfunction
Cause/possible effects
Solution
Motor does not turn on
•
Micro fuse 1F1 defective at the freezer
plug connection.
ing diagram GH10T , GH15T“ on page
•
Cover item 51 not completely closed,
micro switch item 24 is not pressed.
•
Carbon brushes item 49 worn
•
Motor defective
•
Determine the cause, where appro-
priate have this checked by a trained
specialist.
Replace micro fuse.
•
Close cover completely, check micro
switch.
•
Replace carbon brushes
•
Replace motor
Drills become eccentric, tips
no longer true.
Drills cannot be centred; after
sharpening, the tip is not cen-
tred.
Incorrect drill grinding, geome-
try not true.
No back cut on the drill; the
drill does not cut after regrind-
ing.
Drills are not back cut.
Appliance is grinding the drills
wrongly, clearance angle
incorrect.
•
Incorrect operation and maintenance
of the appliance
•
Drill diameter adjusting screw not set
correctly.
•
Drill stop edge and clamping head
group stop surface neglected during
setting.
•
Turn the chuck in the housing
through 180° and grind both sides of
the drill until a grinding noise is no
longer audible.
•
Drill is not clamped correctly in the
chuck.
•
Drill is moved by contact pressure
while grinding in the chuck, because
the grinding disk is worn
•
The chuck has not been inserted
correctly in the clamping head group.
•
Set the drill diameter correctly. Con-
sider the backlash of the thread in
the adjusting screw. The smaller the
drill, the more difficult the setting.
•
Observe the required stop areas
while setting, the cutting edge of the
drill and stop area at the clamping
head group.
•
Flying sparks detectable with HSS
spiral drills? No, grinding disk is
worn and must be replaced.
Clamping head group cannot
be placed in its housing, or
only with difficulty.
•
New appliance, new parts, as yet no
wear on the surfaces.
•
Surfaces covered with grinding dust.
•
Reduce and round the diameter of
the housing or the clamping head
group bevel with 120 grain emery
cloth.
•
Clean the surfaces, use some oil.
The wear of the steel disk,
coated with cubic crystalline
boron nitride is too great.
•
Regrinding of spiral drills with hard
metal tips (hammer drills). The life of
the grinding disk with HSS spiral drills
is much higher.
•
Use of an SDC grinding wheel, see
spare parts