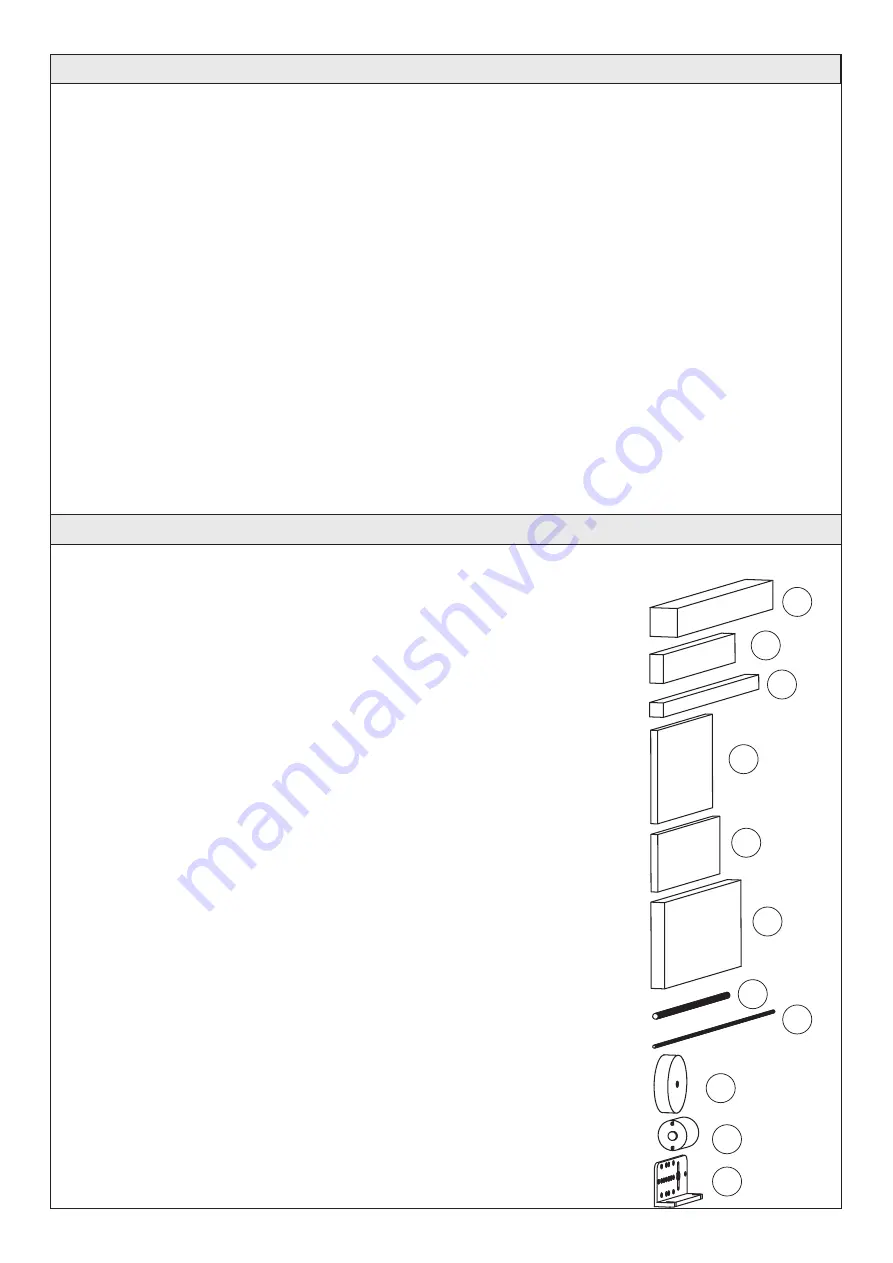
3
E101887#1
3. Tools:
Wood files / rasps:
Choose the correct grade of file or rasp according to the work in hand.
Use needle files for small slots and notches
Note!
Use a sand paper and block on all flat surfaces and loose sheet
on curves.
Sanding:
Use a sand paper and block on all flat surfaces and loose sheet on curves;
Drilling:
Use a pillar drill
Note!
Take care to adhere to the safety rules, tie all long hair back,
remove jewellery, wear an apron and safety glasses. Hold the work
to be drilled in a machine vice.
Clamping:
Hold the work with clamps whilst the glue is drying. Do not over tighten them
or they may leave marks.
Soldering:
Use a 30 Watt soldering iron.
Clean the area to be soldered and use a flux.
Please Note!
Soldering iron tips get hot and can cause burns.!
4. Parts List:
Part
Material
Amount
Size
Diagram
Chassis
Pine
1
20 x 20 x 200 mm
Seat / Arms/
Body / Head
Pine
2
10 x 20 x 150 mm
Arms /Legs
Pine
2
10 x 10 x 200 mm
Base
Plywood
1
5 x 65 x 115 mm
Seat
Plywood
2
5 x 40 x 130 mm
Controller/
Battery holder
Plywood
1
10 x 60 x 160 mm
Axle/ Neck/
Steering bar
Beech dowel
1
4mm dia x 150mm
Roof supports
Welding rod
3 2 mm dia x 250mm
Wheels
Beech
4
40mm dia
Motor
1
21 dia x 25mm
Angle brackets
Plastic
2
2
3
4
5
6
7
8
9
10
11
1