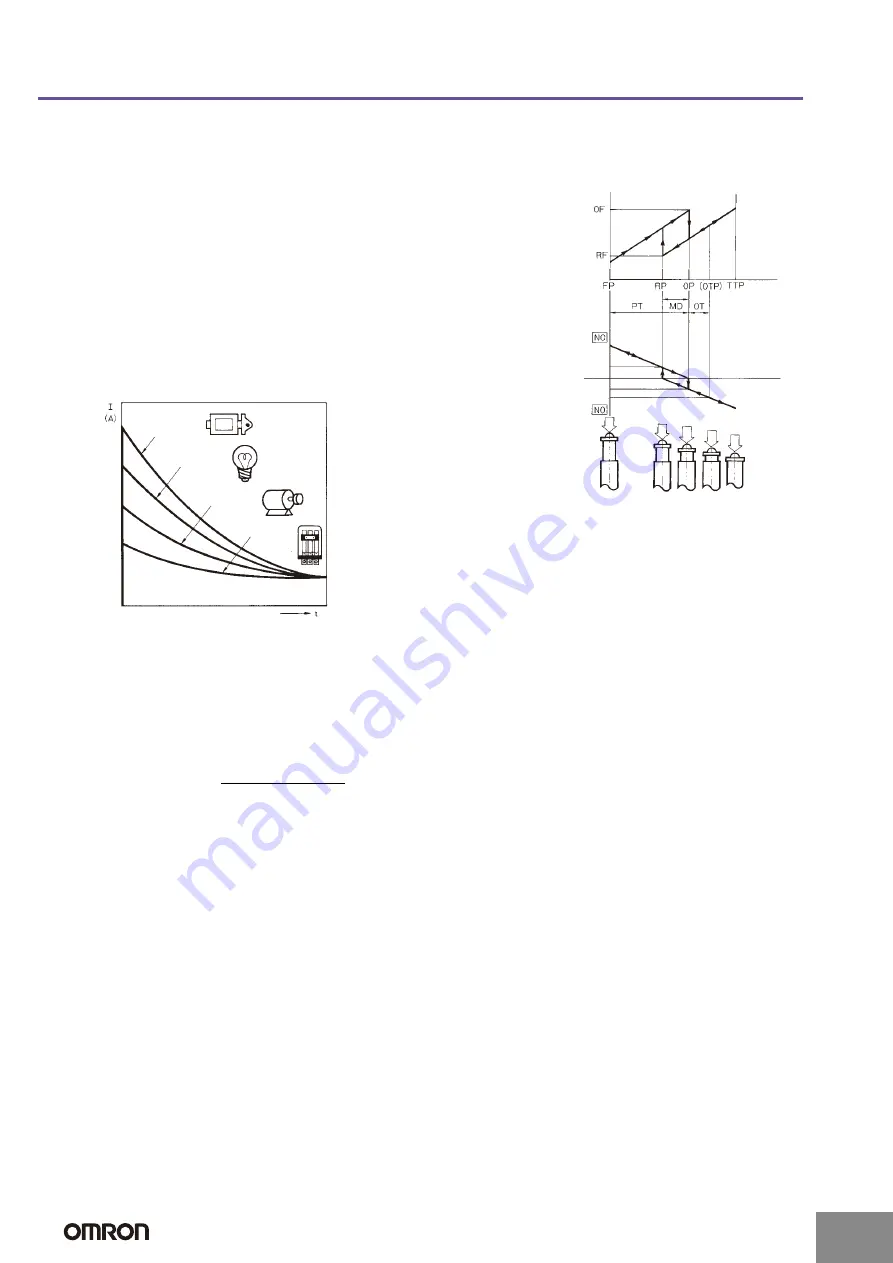
Technical Guide for Limit Switches
Precautions for Correct Use
Switch Operation
•
The Switch in actual operation may cause accidents that cannot be
foreseen from the design stage. Therefore, the Switch must be
practically tested before actual use.
•
When testing the Switch, be sure to apply the actual load condition
together with the actual operating environment.
•
All the performance ratings in this catalog are provided under the
following conditions unless otherwise specified.
Inductive load:
A minimum power factor of 0.4 (AC) or a maximum time constant
of 7 ms (DC)
Lamp load:
An inrush current 10 times higher than the normal current
Motor load:
An inrush current 6 times higher than the normal current
(1) Ambient temperature: +5
°
C to +35
°
C
(2) Ambient humidity: 40% to 70%RH
Note: An inductive load causes a problem especially in DC circuitry. Therefore,
it is essential to know the time constants (L/R) of the load.
Mechanical Characteristics
Operating Force, Stroke, and Contact Characteristics
•
The following graph indicates the relationship between operating
force and stroke or stroke and contact force. In order to operate the
Limit Switch with high reliability, it is necessary to use the Limit
Switch within an appropriate contact force range. If the Limit Switch
is used in a normally closed condition, the dog must be installed so
that the actuator will return to the FP when the actuator is actuated
by the dog. If the Limit Switch is used in a normally open condition,
the actuator must be pressed to 70% to 100% of the OT (i.e., 60%
to 80% of the TT) and any slight fluctuation must be absorbed by
the actuator.
•
If the full stroke is set close to the OP or RP, contact instability may
result. If the full stroke is set to the TTP, the actuator or switch may
become damaged due to the inertia of the dog. In that case, adjust
the stroke with the mounting panel or the dog.
Refer to page 11, Dog Design, page 12, Stroke Settings vs. Dog
Movement Distance, and page 12, Dog Surface for details.
•
The following graph shows an example of changes in contact force
according to the stroke. The contact force near the OP or RP is
unstable, and the Limit Switch cannot maintain high reliability.
Furthermore, the Limit Switch cannot withstand strong vibration or
shock.
•
If the Limit Switch is used so that the actuator is constantly pressed,
it will fail quickly and reset faults may occur. Inspect the Limit Switch
periodically and replace it as required.
Mechanical Conditions for Switch Selection
•
The actuator must be selected according to the operating method.
(Refer to page 9.)
•
Check the operating speed and switching frequency.
1. If the operating speed is extremely low, the switching of the
movable contact will become unstable, thus resulting in incorrect
contact or contact weld.
2. If the operating speed is extremely high, the Switch may break due
to shock. If the switching frequency is high, the switching of the
contacts cannot catch up with the switching frequency. Make
sure that the switching frequency is within the rated switching
frequency.
•
Do not impose excessive force on the actuator, otherwise the
actuator may become damaged or not operate correctly.
•
Make sure that the stroke is set within the suitable range specified
for the model, or otherwise the Switch may break.
Electrical Characteristics
Electrical Characteristics for Switch Selection
•
The switching load capacity of the Switch greatly varies between
AC and DC. Always be sure to apply the rated load. The control
capacity will drastically drop if it is a DC load. This is because a DC
load has no current zero-cross point, unlike an AC load. Therefore,
if an arc is generated, it may continue comparatively for a long time.
Furthermore, the current direction is always the same, which
results in a contact relocation phenomena whereby the contacts
easily stick to each other and do not separate when the surfaces of
the contacts are uneven.
•
If the load is inductive, counter-electromotive voltage will be
generated. The higher the voltage is, the higher the generated
energy will be, which will increase the abrasion of the contacts and
contact relocation phenomena. Be sure to use the Switch within the
rated conditions.
•
If the load is a minute voltage or current load, use a dedicated
Switch for minute loads. The reliability of silver-plated contacts,
which are used by standard Switches, will be insufficient if the load
is a minute voltage or current load.
Solenoid
(Approximately
10 to 20 times higher)
Incandescent lamp
(Approximately
10 to 15 times higher)
Motor
(Approximately
5 to 10 times higher)
Relay
(Approximately
4 to 5 times higher)
Oper
ating f
orce
Contact f
orce
Stroke
Stroke
FP
OTP
Changes to opposite side
Changes to opposite side
http://www.ia.omron.com/
C-2
(c)Copyright OMRON Corporation 2007 All Rights Reserved.