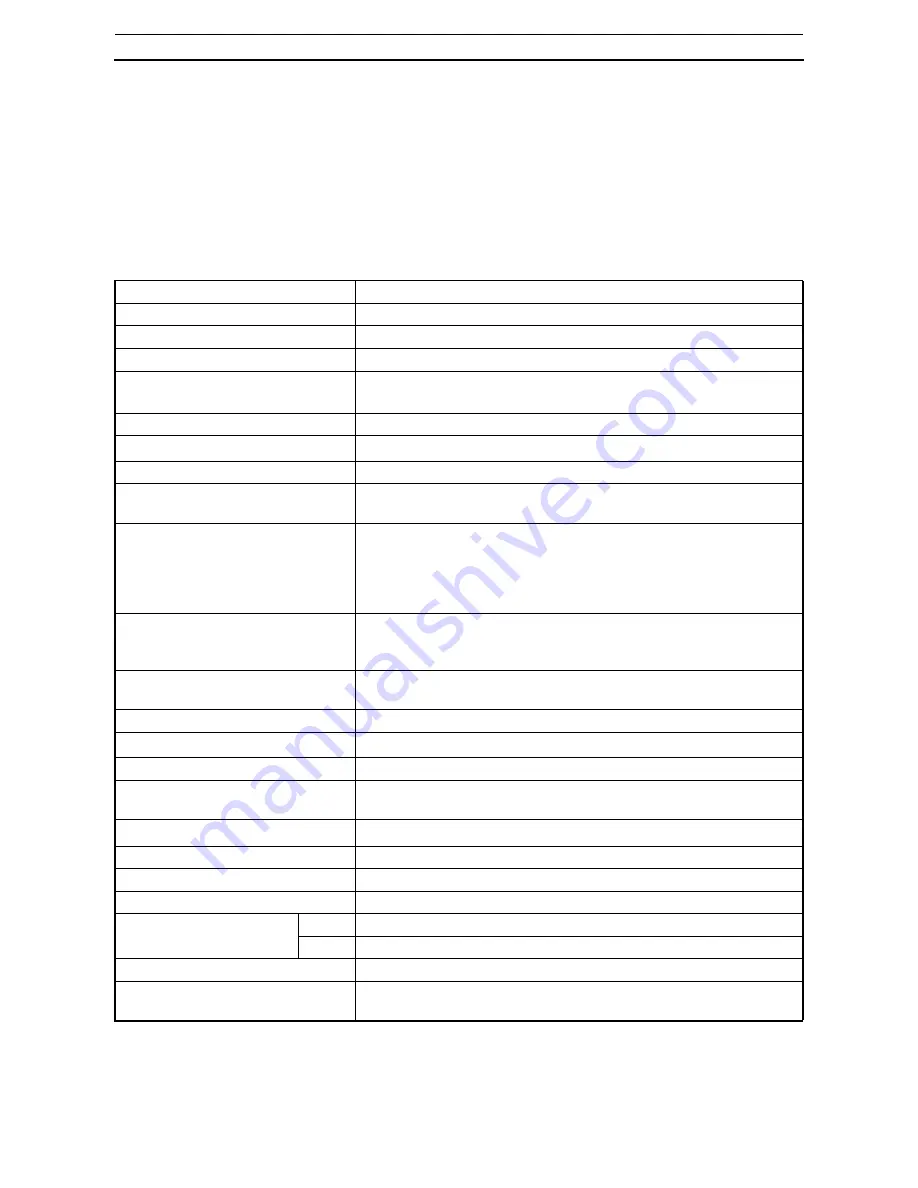
2-1 F3SS System Specifications
2 Theory of Operation
2
2 Theory of Operation
2-1 F3SS System Specifications
The F3SS is a long-range, single-beam infrared safety control designed for perimeter and access guarding. In-
terruption of the beam sends a stop signal to the guarded machine. A “redundant” microprocessor design com-
bined with extensive fault mode and effects analysis provides safe, control reliable operation.
A F3SS system consists of one emitter and one receiver. No interconnecting cables or separate control enclo-
sure are required. Maximum distance between emitter and receiver is 60 m(200 ft.).
2-1-1 Technical Specifications*
*1. ESPE(Electro-Sensitive Protective Equipment)
*2. AOPD(Active Opto-electronic Protective Devices)
*Specifications subject to change without notice.
Operating range
0.3-60 m
Number of beams
1 (single beam)
Beam diameter
31 mm
Minimum object resolution
Opaque object, ø31 mm or more
Orientation angle
Emitter and receiver: ±2.5
°
maximum, at operating range longer than 3
m (IEC61496-2).
Light source (emission waveform)
Infrared LED (880 nm)
Power supply voltage
24 VDC
±10%, ripple (p-p) 5% or less
Rise time after power ON
Within 4 seconds
Current consumption
Emitter: 170 mA max.
Receiver: 800 mA max.
Operating mode
Either of the following modes is selectable by the select switch of the
receiver:
Auto start
Start interlock
Start/restart interlock
Control output
PNP transistor output x 2 outputs, load current 250 mA or less (resid-
ual voltage 1V or less) (excluding voltage drop due to cable exten-
sion), ON at light ON.
Protective circuit
Output load is short-circuit protected, inverted power supply connec-
tion is protected.
Response time (ON-->OFF)
35 ms or shorter
Ambient temperature
0-55
°
C at operation and storage (non-icing, non-condensing)
Ambient humidity
35-95% RH at operation and storage (non-condensing)
Resistance to vibration
Malfunction and durability: 10-55 Hz, double amplitude 0.7 mm, X, Y
and Z-direction, 20 sweeps
Shock resistance
Malfunction and durability: 100 m/s
2
, X, Y and Z-direction, 1000 times
Protective structure
IEC60529 IP65
Connecting method
Connect by terminal block on internal board.
Weight (packaged)
2.5kg
Material
Case
Aluminum
Cap
Aluminum
Accessories
Mounting hardware, operating instructions, caps for unused conduits
Applicable standard
IEC(EN)61496-1 TYPE4 ESPE *1
IEC61496-2 TYPE4 AOPD *2
Summary of Contents for F3SS
Page 4: ......