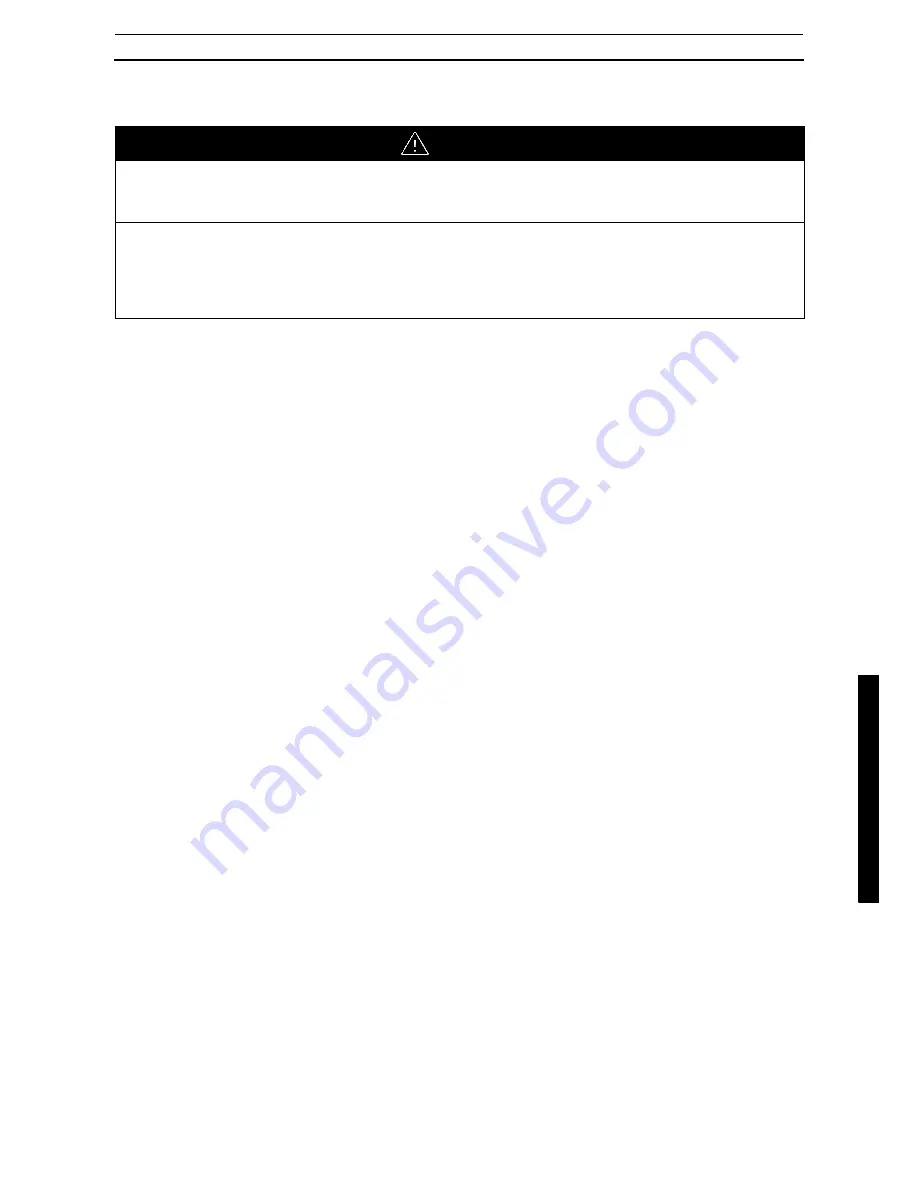
1 Important Safety Warnings
1
1 Important Safety Warnings
A F3SL system is a general purpose presence sensing device designed to guard personnel working around
moving machinery.
Whether a specific machine application and F3SL system installation complies with safety regulations depends
on the proper application, installation, maintenance and operation of the F3SL system. These items are the re-
sponsibility of the purchaser, installer and employer.
The employer is responsible for the selection and training of personnel to properly install, operate, and maintain
the machine and its safeguarding systems. A F3SL system should only be installed, verified and maintained by
a qualified person.A qualified person is defined as "a person or persons who, by possession of a recognized
degree or certificate of professional training, or who, by extensive knowledge, training or experience, has suc-
cessfully demonstrated the ability to solve problems relating to the subject matter and work." (ANSI B30.2-1983)
To use a F3SL system the following requirements must be met:
• The guarded machine
must
be able to stop anywhere in its cycle. Do not use a safety light curtain on a press
with a full-revolution clutch.
• The guarded machine must not present a hazard from flying parts.
• The guarded machine must have a consistent stopping time and adequate control mechanisms.
• Severe smoke, particulate matter and corrosives may degrade the efficiency of a safety light curtain. Do not
use the F3SL system in this type of environment.
• All applicable governmental and local rules, codes, and regulations must be satisfied. This is the employer’s
responsibility.
• All safety-related machine control elements must be designed so that a alarm in the control logic or failure
of the control circuit does not lead to a failure to danger.
• Additional guarding may be required for access to dangerous areas not covered by the F3SL system.
• Perform the OMRON test procedure at installation and after maintenance, adjustment, repair or modification
to the machine controls, tooling, dies or machine, or the F3SL system.
• Perform only the test and repair procedures outlined in this manual.
• Follow all procedures in this manual for proper operation of the F3SL system.
The enforcement of these requirements is beyond the control of OMRON. The employer has the sole responsi-
bility to follow the preceding requirements and any other procedures, conditions and requirements specific to his
machinery.
WARNING
Please read this information completely before starting the installation procedure. A F3SL should only be
installed, checked out and maintained by a qualified person. It is important that the user be familiar with the
installation requirements, safe mounting distance, controls and features before using the F3SL.
If the F3SL is used as a safety device, the user has the responsibility to insure that applicable national, fed-
eral and local safety rules, codes and regulations are satisfied. In addition, the user should insure that all
machine operators, maintenance personnel, electricians, supervisors, etc. are familiar with and understand
all instructions regarding the use of the F3SL, the machinery on which it is installed and the appropriate
safety regulations.
Summary of Contents for F3SL
Page 2: ......