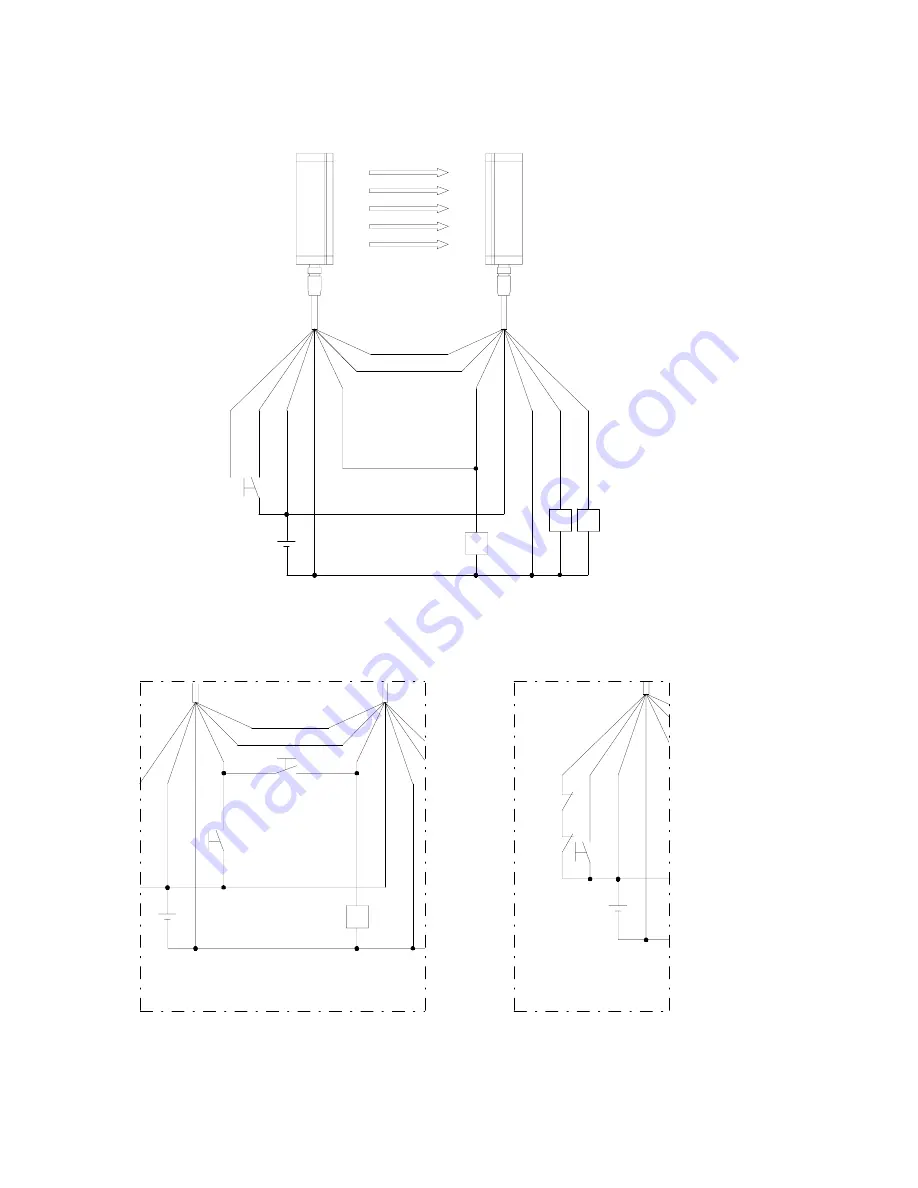
F3S-B
28
2-3-2 Wiring Diagram
Disconnect all sources of power before wiring the F3S-B to a machine.
RS-485(A) (Grey 5)
RS-485(B) (Pink 6)
In
sta
bility (
ye
llo
w
4)
Receiver
Emitter
E
xt. test (
G
reen 3
)
Output2 (W
hi
te
1)
Output1 (Gree
n
3)
0 V
(B
lue 7)
24
VDC (
B
ro
wn
2
)
0 V
(B
lue 7)
24
VDC (
B
ro
wn
2
)
Relay m
onitoring (
W
hite 1)
K2
K1
E1
S1
E1: 24 VDC Power supply
S1: External test switch
RS-485(A) (Grey 5)
RS-485(B) (Pink 6)
0 V
(B
lue 7)
24
VDC (
B
ro
wn
2
)
0 V
(B
lue 7)
24
VDC (
B
ro
wn
2
)
0 V
(B
lue 7)
24
VDC (
B
ro
wn
2
)
E1
S1
E
xt. test (
G
reen 3
)
R
el
ay m
oni
tori
ng
(W
hi
te 1)
k1
k2
k1, k2: Auxiliary contact to monitor the
condition of the final relay
Emitter
Emitter
Receiver
E1
S2: Restart interlock reset switch
K1, K2: Relay or PLC input to control the dangerous movement of a machine
Load: Inductive load with surge suppressor (Note) or resistive load to indicate unstable condition
Inter
lock selection (
yell
ow
4)
S2
Load
Load
Inter
lock selection
(y
el
lo
w
4)
In
sta
bility (
ye
llo
w
4)
S3
S3: Mode change switch for inspection
When using Start/restart interlock Function
When using optional Relay Monitoring Function