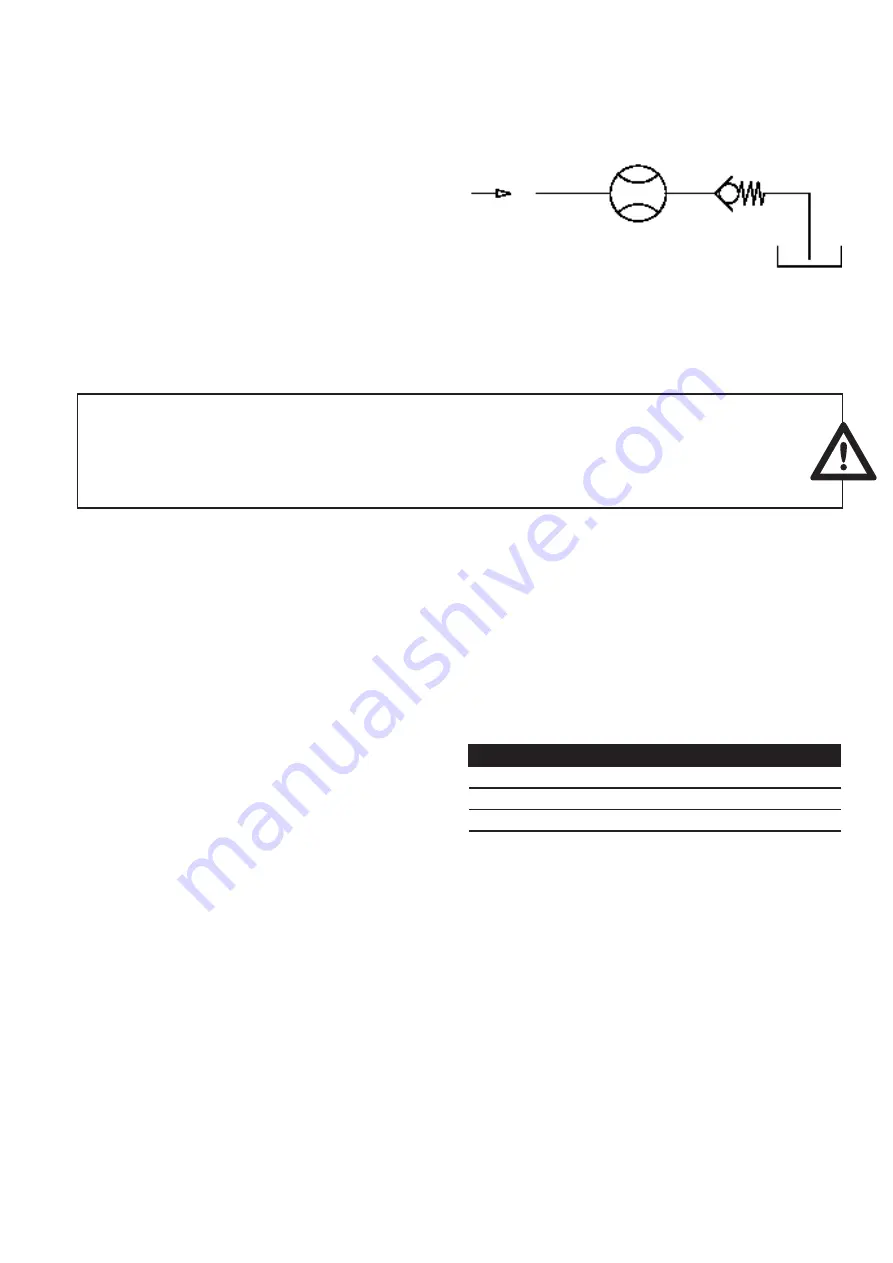
6
9. Mounting the Flow Meter
The flow meter should be mounted in an easily accessible location so that
disassembly to clean the measuring elements is easy. Since flow meters
operate in any installation position and flow direction, you can mount it
anywhere in your system. When installing the flow meter, make sure that
liquid remains in the flow meter even at standstill of the system and that the
flow meter can never run dry. The outlet of the flow meter should always
have a certain backpressure since this fixes the measuring element of the
flow meter in the liquid column (the measuring element uses to support itself
on the liquid column) and the pipeline cannot empty itself. In critical cases,
or if the pipeline can run empty in standstill or standby mode, it is always
advisable to install an additional non-return check valve in the outlet line.
Flow meters of the ”FHG“ series can be installed in the pipeline. Always
select large cross-sections (if possible) for the hydraulic inlet and outlet or
the entire pipeline system. This reduces the pressure drop and the flow rate
throughout the system.
Installation Notes
Installation Position
Any, note arrow indicating preferred direction if necessary (calibration ar-
row).Mount the device in such a way that the preamplifier is turned away
from any potential heat source.
Straight pipe sections are
not
required in inlet/outlet.
Connecting Units
If the connecting units (mounting flanges) are to be installed on-site, compli-
ance with the specified torque is required.
Important:
Make sure that the flow meter measuring elements are always completely filled both
in inflow and outflow and that the outflow has a little backpressure. This prevents the
measuring elements from being damaged by a sudden and steep increase of flow and
at the same time improves measurement accuracy.
Fig. 1: Flow meter with backpressure
Pipe Thread
Please comply with the screw-in depths and sealing systems. PTFE tape or
liquid sealants such as adhesives are not permitted!
Fastening
The devices must be installed stress-free into the pipeline. This is accomplis-
hed with fastening screws located at the face sides in the connecting units.
For stress-free assembly, the compressive strength may be limited!
FHG Flow Meter Size
Torque
FHG 1xx2
70 Nm
FHG 1xx4
120 Nm
FHG 1xx5
240 Nm
FHG 1xx7
160 Nm
Table 1: Starting torque of the connection units
10. Cleaning and Flushing of Pipeline before Initial Start-Up
Before initial start-up of the flow meter, you must flush and clean the whole
system to prevent contaminants from reaching the measuring elements duri-
ng the assembly and installation. Foreign matter or contaminants may block
the flow meter or severely damage it so that the flow meter readings are no
longer valid and the device must be returned for repairs. After completion
of the installation or piping, you must first flush the entire pipeline system
and carefully clean and flush the tank. This requires that the flow sensor is
removed from the fluid circuit to flush out all foreign matter or contaminants
(e.g. chips, metal parts) without problems. Use a rinsing fluid that is compa-
tible with the subsequent used fluid and will not cause adverse reactions.
Such information can be obtained from the supplier or manufacturer of the
fluid or from Omega.
Flow meters are sensors manufactured with a high degree of precision.
They have mechanical measuring elements consisting of two rotors fitted
into the housing with narrow gaps. Even the smallest damage to the rotors
causes a measuring error. Always make sure that foreign matter or conta-
minants cannot reach the measuring elements and that the fluid flowing
through the flow meter is always free of pollutants and particles. Once the
system is thoroughly flushed and no extraneous material is in the piping sys-
tem, you can mount the flow meter into the fluid circuit and start the actual
initial startup process.
Non return valve
Flow meter
Tank