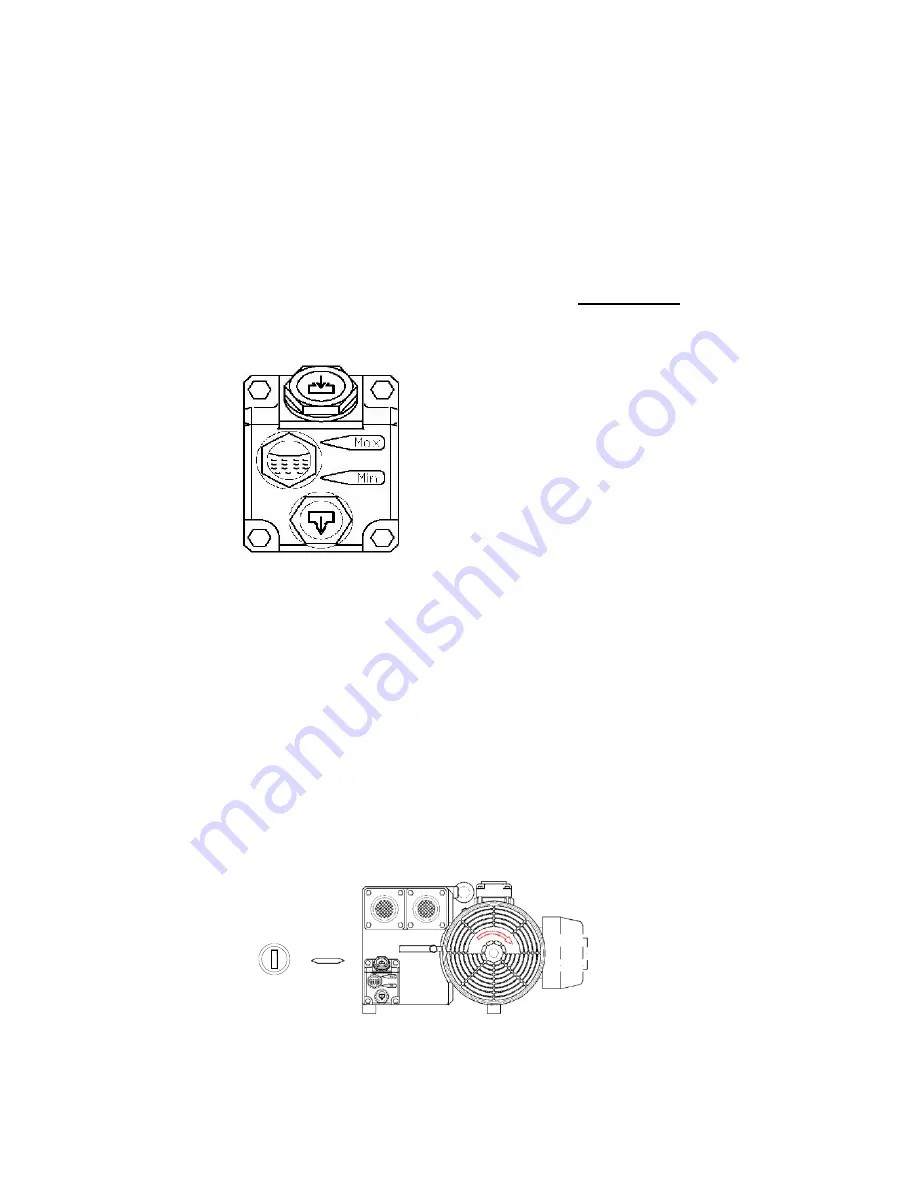
6
2.5 CHECK OIL LEVEL
Check the oil level only when the machine is not in operation and all
vacuum built up in the chamber has been vented. Be aware that the oil
may be very hot and avoid all contact.
Checking the Oil Level
* Check the oil level on a daily basis
* When checking the oil level use the sight gauge shown in
figure 1 below
. The level
should be between the arrows indicating Minimum and Maximum. If the level is below the
minimum arrow add oil until the maximum arrow is reached.
Figure 1
2.6 POWER CONNECTION
When preparing to install the machine’s main power connection please refer to the electrical
information on the serial number plate located on the machine’s back panel. A certified
electrician should be employed to complete this connection.
2.7 VACUUM PUMP ROTATION
If your machine operates on 3 phase power it is important to check the rotation of the vacuum
pump. The pump should turn in the direction indicated in
Figure 2
below. If the pump turns
in the wrong direction it will make a sound that is obviously wrong. Turn off the power
immediately and change the position of two of the power wires and retest.
Figure 2
Main switch