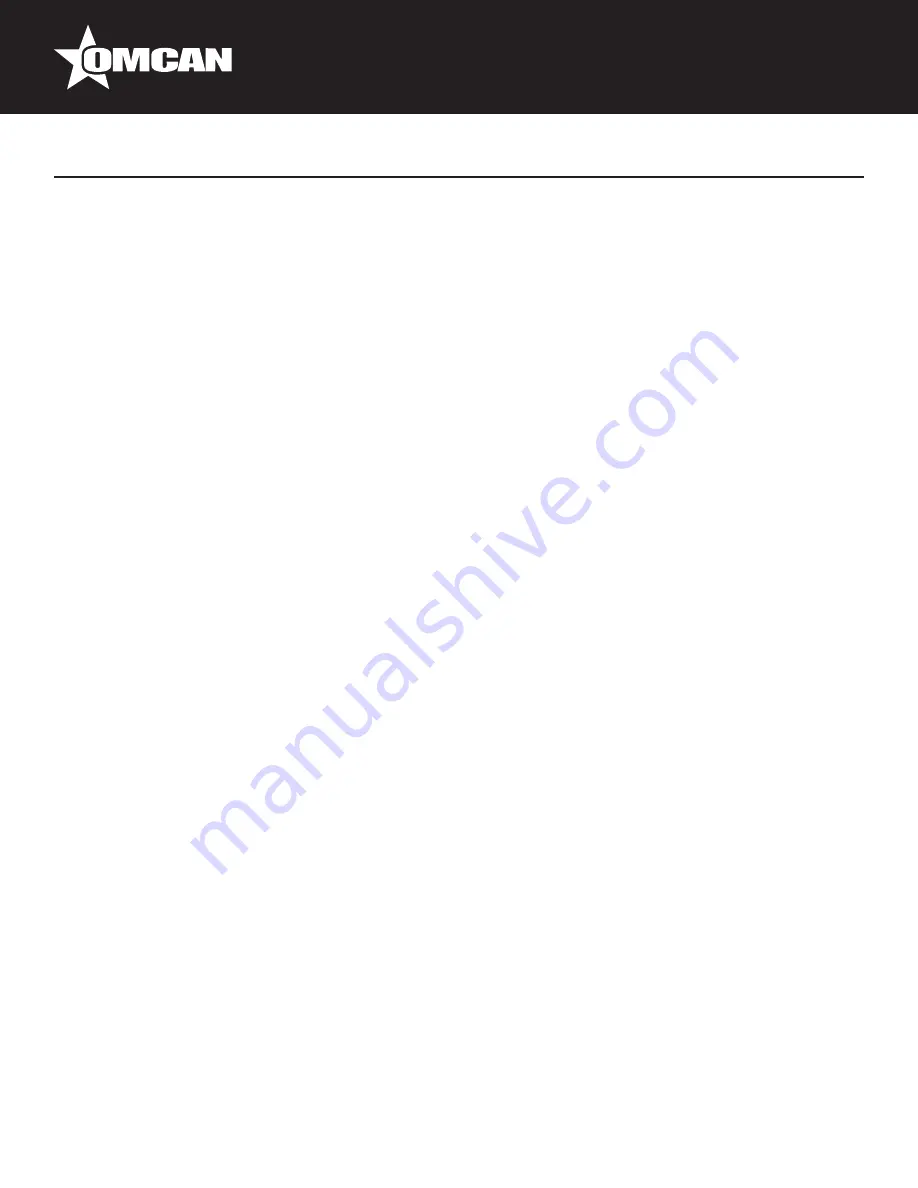
11
Operation
INFORMATION OF A GENERAL NATURE FOR NORMAL USE
1.
Perform the safety controls at the start of every day and/or work shift.
2. The entire mass of dough to roll must be malleable and at room temperature. It is absolutely forbidden to
roll blocks of dough that are not malleable, if just taken out of a freezer, for example.
3. The thickness of the mass of dough before a rolling pass must be below 40mm in order to prevent it from
bumping against the interlocked guard fitted for the protection of the roller feed area.
4. The use of the worktables as worktops for working the dough by hand or with means that are not
contemplated by the manufacturer is forbidden; in particular, it is forbidden to place masses of dough
on them or beat them with rolling pins or anything else to reduce their thickness; the worktables and the
associated supports are not suitable for supporting stresses apart from those due to the tables themselves,
the dough to roll and the cutting unit where applicable; in the event of mechanical yielding, the risk of
causing serious damage to the machine as well as to exposed persons would be very high.
5. Do not move excessively heavy or very big masses by hand, so as to prevent risks of an ergonomic type
with the possibility of muscle-skeletal injuries,
6.
If it is necessary sprinkle flour on the dough when working it, do not spread it brusquely but simply let it fall
on several points of the dough; the reason for this is to limit dispersion of dust in the air.
7.
No particular PPE are required for routine use, unless the need arises from a health and safety risk
assessment conducted by the employer. For example if the operator ignores the above and sprinkles flour
with fast broad arm movement clouds of flour will develop in the air with consequent health risks if inhaled
(rhinitis, asthma, etc.); in this case, it is the responsibility of the employer to adopt appropriate measures
for eliminating or minimizing the risks caused by dispersed dust (e.g. before sprinkling the flour check
that there is no one in the vicinity, wear a mask for protecting the airways with an adequate filtering power
for the flour grain dimensions – indicated in the technical sheet if available, or to be measured by the
employer, etc.). The employer is responsible for identifying any other PPE that may be necessary (e.g. for
ensuring the hygiene of the foodstuffs).
8. Set sheeting thicknesses that are just smaller than the thickness of the dough to roll, so as to prevent the
dough from “tearing”; this becomes all the more important the smaller the thickness of the dough to roll.
9. When the cutting unit is mounted on the machine the maximum pastry thickness than can pass underneath
is 7mm with the unit lowered, and 23mm with the unit raised.
10.
Do not recover the flour deposited on parts of the machine; it could be contaminated and compromise the
purity and hygiene of the dough with risks for consumers as a consequence.
11. Attempting to reach the rollers from under the guard is forbidden; there are no reasons for doing so and
such action would lead to pointless exposure to risks of injury. To remove residues between the scrapers
and the rollers or to clean the rollers, stop the machine and raise the guards: it is possible to access the
rollers easily and safely.
12. When the emergency button is pressed, the machine stops and the electric power to the motor is
disconnected; only use it when necessary – otherwise use the STOP button; to restart the machine it is
necessary to rearm the emergency button and press the enabling button.
13.
The same effect is obtained by raising an interlocked guard; to restart the machine it is necessary to close
the guard and then press the start enabling button.
14. In normal conditions, do not stop the machine by raising the guards so as not to expose yourself to
pointless risks (rollers and belts continue running for a maximum of one second before stopping) and
contribute to the longest possible life of the safety system; instead use the STOP button.
15.
When cleaning the machine wear at least an adequate dust mask and complete protection goggles.
Summary of Contents for BE-IT-710-CSS
Page 19: ...19 Parts Breakdown Model BE IT 710 CSS 49115...
Page 21: ...21 Parts Breakdown Model BE IT 710 FSS 49116 Base Assembly...
Page 22: ...22 Parts Breakdown Model BE IT 710 FSS 49116 Head Assembly...
Page 24: ...24 Electrical Schematics Model BE IT 710 CSS 49115...
Page 25: ...25 Electrical Schematics Model BE IT 710 FSS 49116...