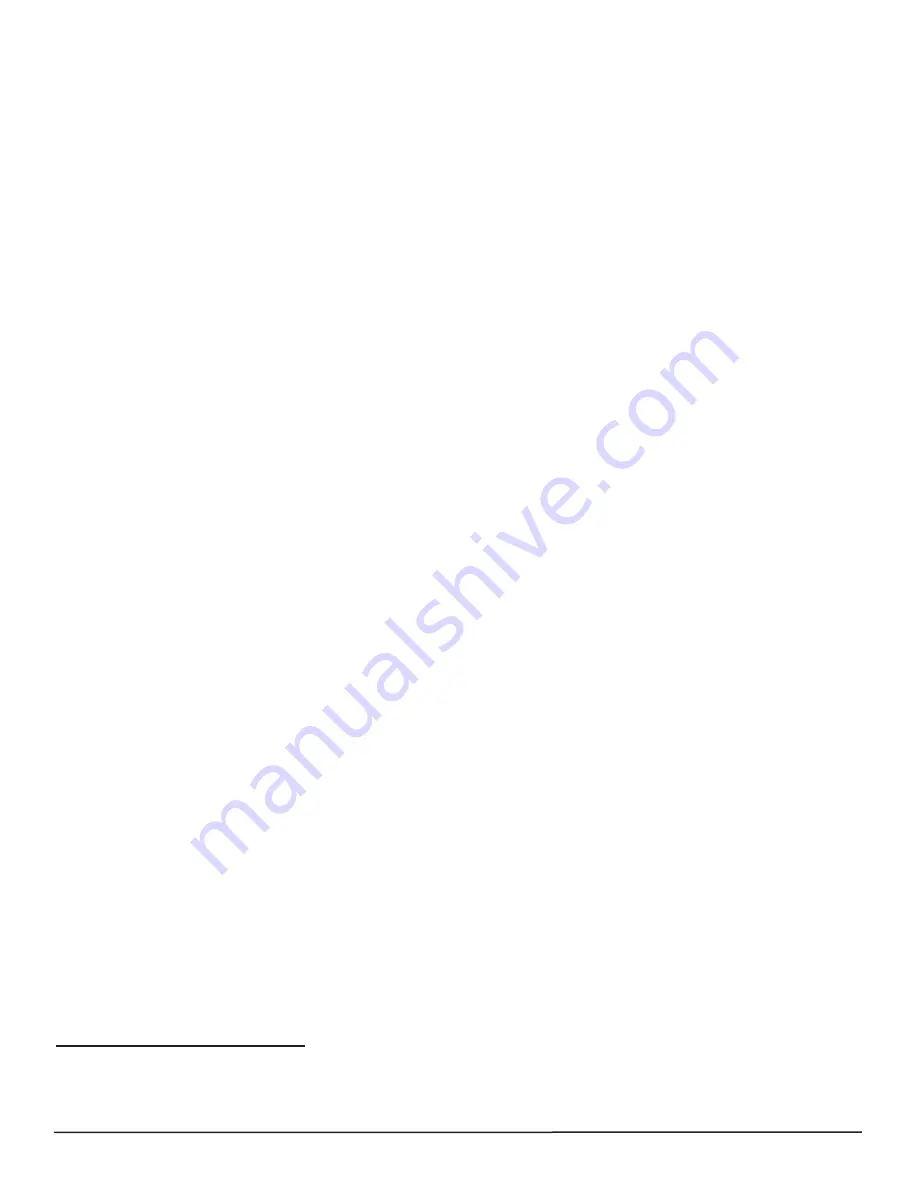
Before starting your project become familiar with this assembly manual and determine if you can
complete the project yourself or will require a professional contractor. Please note that certain
counties and municipalities require building permits prior to installation. We recommend to all
consumers that they check with their local county/municipality for these specifics prior to purchasing
any of our products since this is your sole responsibility.
Prior to the product arriving, clear the construction area. Remove all debris; roots, grass, rocks, etc.
Make sure the ground slopes away from the site at least 10 feet in all directions. If necessary, build
up the soil in the center of the site and slope away for the high point to provide drainage. Fill in any
low spots within the perimeter of the site. A slope of 1/8 inch per foot is enough to prevent water
accumulation. We recommend excavating the site 4-6 inches deep and laying gravel or crushed
rock where drainage may be a concern.
What type of foundation should I use?
P
atio Stone Foundation :
If the ground is stable and has sufficient drainage, you can set patio
stones directly on firm compacted soil. If not, consider laying down sand and then gravel or crushed
rock. Excavate the site making it about 12” wider and longer than the floor footprint. Excavate down
approximately 4-6 inches deep. Lay 1-2 inches of sand first and then fill with 3-4 inches of gravel or
rock for good drainage and support. Most of our sheds and playhouses include floors with support
runners. Support each runner with 4-5 patio stones (less for smaller sheds). Patio stones can be
anything from a mid size brick to a round our square 12” long by 1 1/2” thick stone. Place stones
directly under the floor runners, check for level and adjust height as necessary. Having a solid and
level foundation is the most critical piece of work you can do to make the project go smoothly. Most
of this work can be done prior to your shed arriving!
4x4 Pressure Treated Beam Foundation :
You can build directly on pressure-treated beams or
railroad ties laid on a properly prepared construction site as mentioned above. Run beams
perpendicular to floor runners. Use a 2x4 straight piece of lumber on edge and a carpenter's level
to position correctly. To prevent the beams from shifting, secure them with ½ inch rebar inserted
through holes drilled in the beams and driven 3 to 4 feet into the ground. Leave each side or end of
the foundation open to promote drainage and air circulation beneath the floor. Consider using a wire
mesh or equivalent to prevent pesky critters from gaining access on ends.
Concrete - Slab Foundation :
Typically a slab 3-4 inches thick laid over a sub-base of 4 inches of
gravel or crushed rock is sufficient but may vary depending on your geographic location. Using
either mix your own concrete or having it delivered by truck, ready to pour, depends on how much
time and effort you have to dedicate to the project. In any event, make sure you excavate the slab
area to a depth 6 inches. This would put the finished slab surface approximately 2 inches above
ground (remember you will be using 4 inches of gravel as your subbase). For example, a slab for
our 8’x12’ SpaceMaker Shed will require approximately 1 cubic yard of premixed concrete.
For more detailed information on how to pour your concrete-slab foundation or any other questions
regarding specifications, foundations and permits, please visit our website at
www.outdoorlivingtoday.com
or call our Customer Support Line at
1-888-658-1658
to speak with
a Product Representative.
* Please note that all measurements in our Detailed Assembly Manuals may be subject to change without notice. Please
confirm exact foundation size with Outdoor Living Today if you have any concerns or questions.
What Can I Do Before My Shed Arrives?
1-888-658-1658 www.outdoorlivingtoday.com [email protected]
Page 5