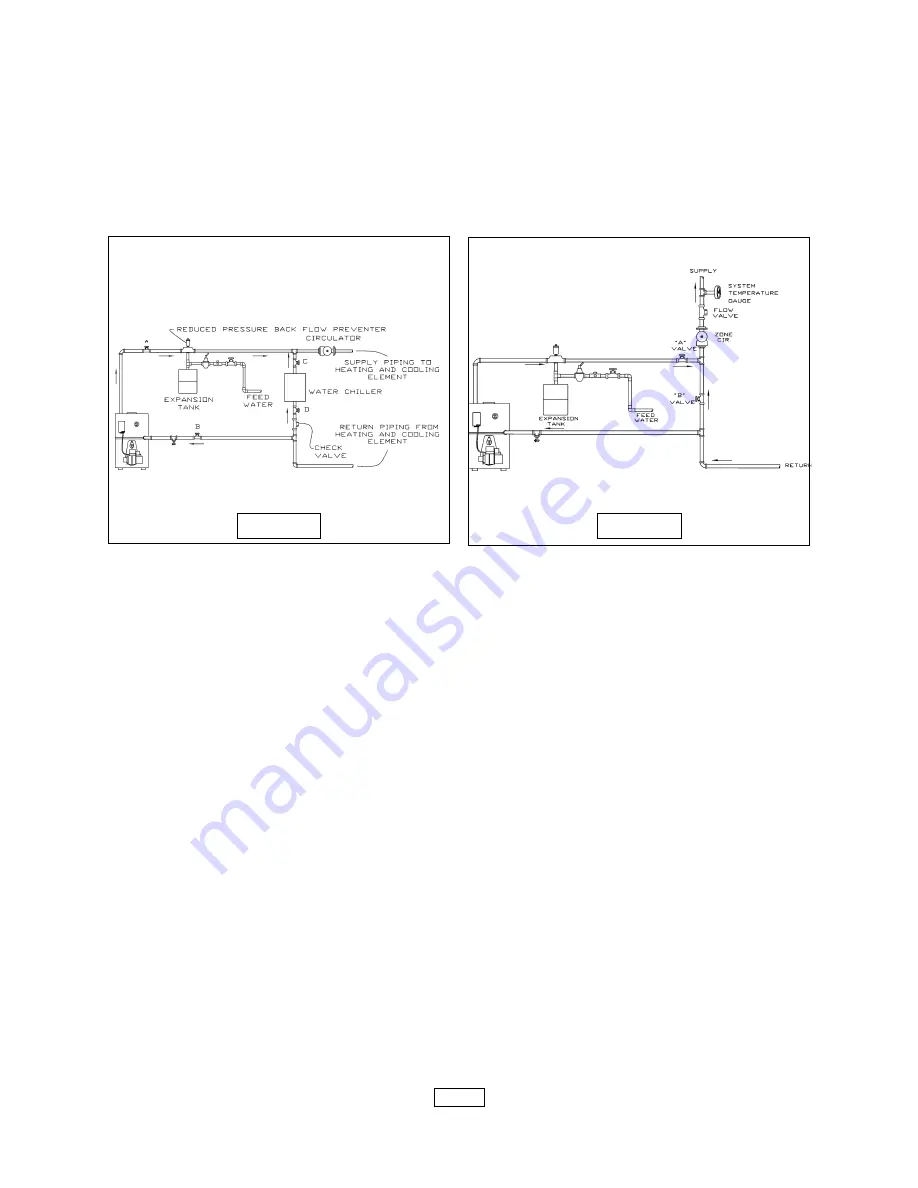
PAGE 6
CONNECTING SUPPLY AND RETURN PIPING
1. Connect supply and return piping as suggested in
figure 5, below. When the boiler is
used in connection with refrigerated systems:
A. The chilled medium MUST BE IN PARALLEL with the boiler.
B. Use appropriate valves to prevent the chilled medium from entering the heating
boiler.
2. During the heating cycle open valves
A
and
B
, close valves
C
and
D
.
3. During heating cooling cycle open valves
C
and
D
, close valves
A
and
B
.
A. Maintain a minimum clearance of one inch to hot water pipes.
In air handling units where they may be exposed to refrigerated air circulation, the boiler
piping system
MUST
be supplied with flow control valves or other automatic means to
prevent gravity circulation of the boiler water during the cooling cycle.
4. Hot water boilers installed above radiation level must be provided with a low water
device either as part of the boiler or at the time of boiler installation.
5. When a boiler is connected to a heating system that utilizes multiple zoned
circulators, each circulator must be supplied with a flow control valve to prevent gravity
circulation.
*
Reduced pressure back flow preventer must be present under provisions required by
the Environmental Protection Agency, (EPA).
6. Bypass piping is an option which gives the ability to adjust the supply boiler water
temperature to fit the system or condition of the installation. Although, this method of
piping is not typically required for baseboard heating systems.
A. This method is used to protect systems using radiant panels and the material they
are encased in from high temperature supply water from the boiler. See figure 6
above.
B. This method is used to protect boilers from condensate forming due to low
temperature return water. Generally noticed in large converted gravity systems or other
large water volume systems. See figure 7 on page 7.
FIGURE 6
FIGURE 5