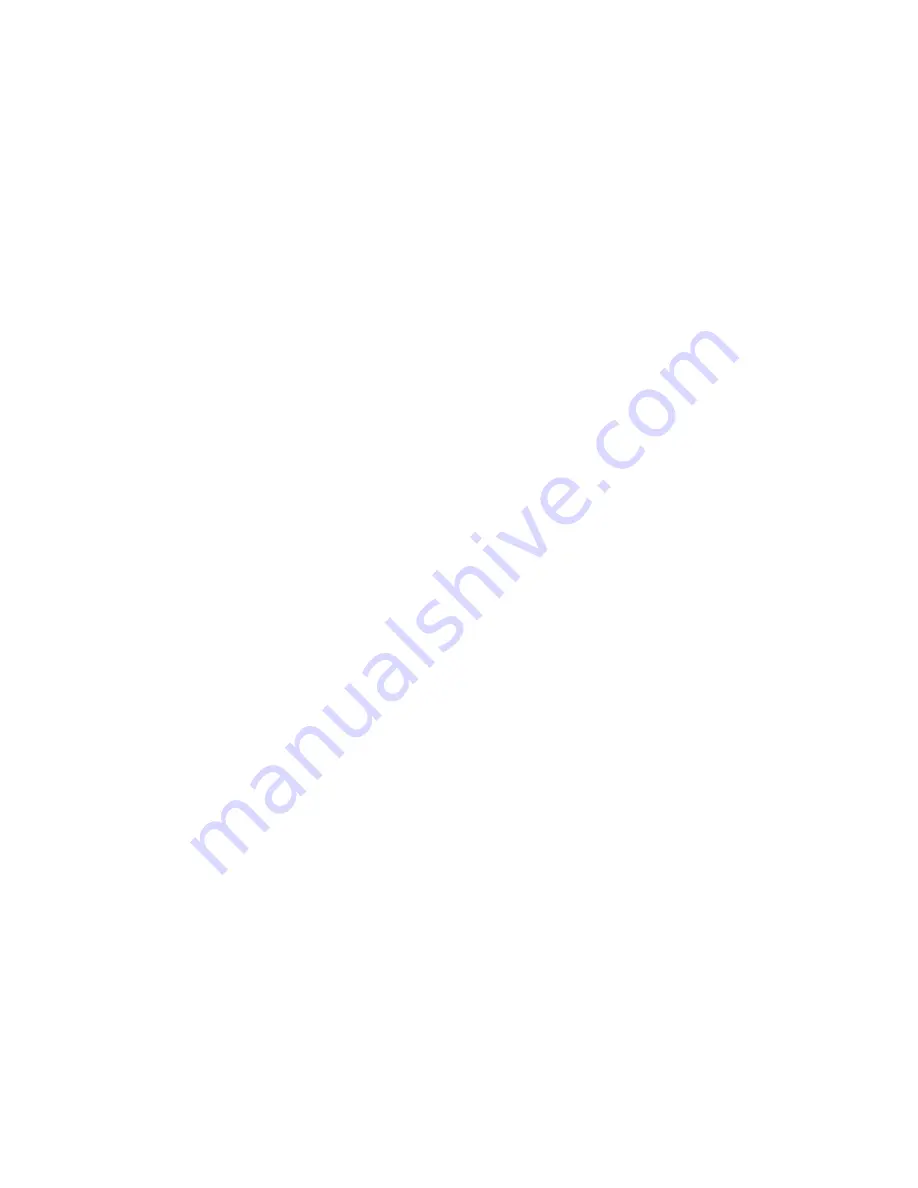
Page | 8
II.INSTALLATION
This section explains the installation requirements for the Stoner. All Oliver
Stoners have been tested per Oliver Manufacturing’s protocols, at our facility, to
ensure the quality of the machine. Stoners are operated on test blocks at the factory
for a minimum of five hours. During and after operation, the drive mechanism
and
controls are checked to ensure that they will operate satisfactorily when you set
them up at your factory.
2.1 De-Skidding and Uncrating
Although Oliver is built to give years of service, it can be damaged while
uncrating. First the top of the crate should be carefully removed. Then take off the
sides. After the top and sides are withdrawn, the Oliver Stoner can be disengaged
from the bottom of the crate by removing the four 3/8" bolts located on the
mounting flanges of the stoner. While removing the crate, do not put anything on
the separating deck. If the deck is damaged, good separations are impossible. Also,
be careful not to puncture the filter screens located on the sides of the machine. If
the filter screens are damaged, dirt may be sucked into the machine and may plug
the deck.
Immediately after uncrating your Oliver Stoner, inspect for shipping damage.
If the machine is impaired in any way, it was caused in transit and a claim should
be filed with the carrier.
The feed hopper, mounting brackets and discharge hoppers are attached to
the inside of the crate or the inside of the stoner. All items securely fastened inside
the stoner may be removed by opening the filter screens and cutting the tie wires.
2.2 Foundation and space requirements
Foundation Requirement:
A solid foundation is required for your Oliver
Stoner. False vibrations from flooring can ruin the separation quality of the
machine. A six-inch concrete slab makes an ideal platform but is not essential. Many
customers operate Oliver Stoners on wooden floors with no problems. If you feel
that your floor is insecure, please contact the factory for recommendations.
Summary of Contents for Hi-Cap N Series
Page 6: ...Page 6 ...
Page 34: ...Page 34 this section intentionally left blank ...
Page 35: ...Page 35 V Appendices Appendix A Maintenance and Basic Troubleshooting ...
Page 41: ...Page 41 Appendix B The ABB ACS380 VFD ...
Page 43: ...43 P a g e Figure 17 VFD keypad display ...
Page 44: ...44 P a g e Figure 18 VFD keypad status line ...
Page 47: ...47 P a g e A 2 Programming the VFD from the Keypad Figure 20 Changing VFD parameters ...
Page 49: ...49 P a g e ...
Page 50: ...50 P a g e Appendix C Timer manual ...
Page 51: ...51 P a g e C 1 Getting to know timer operation ...
Page 52: ...52 P a g e C 2 Timer dip switch selection ...
Page 53: ...53 P a g e Appendix D Electrical and Dimensional drawings ...
Page 54: ...Page 54 D 1 Electrical drawings ...
Page 55: ...55 P a g e ...
Page 56: ...56 P a g e ...
Page 57: ...57 P a g e D 2 DIMENSIONAL LAYOUT DRAWINGS ...
Page 58: ......