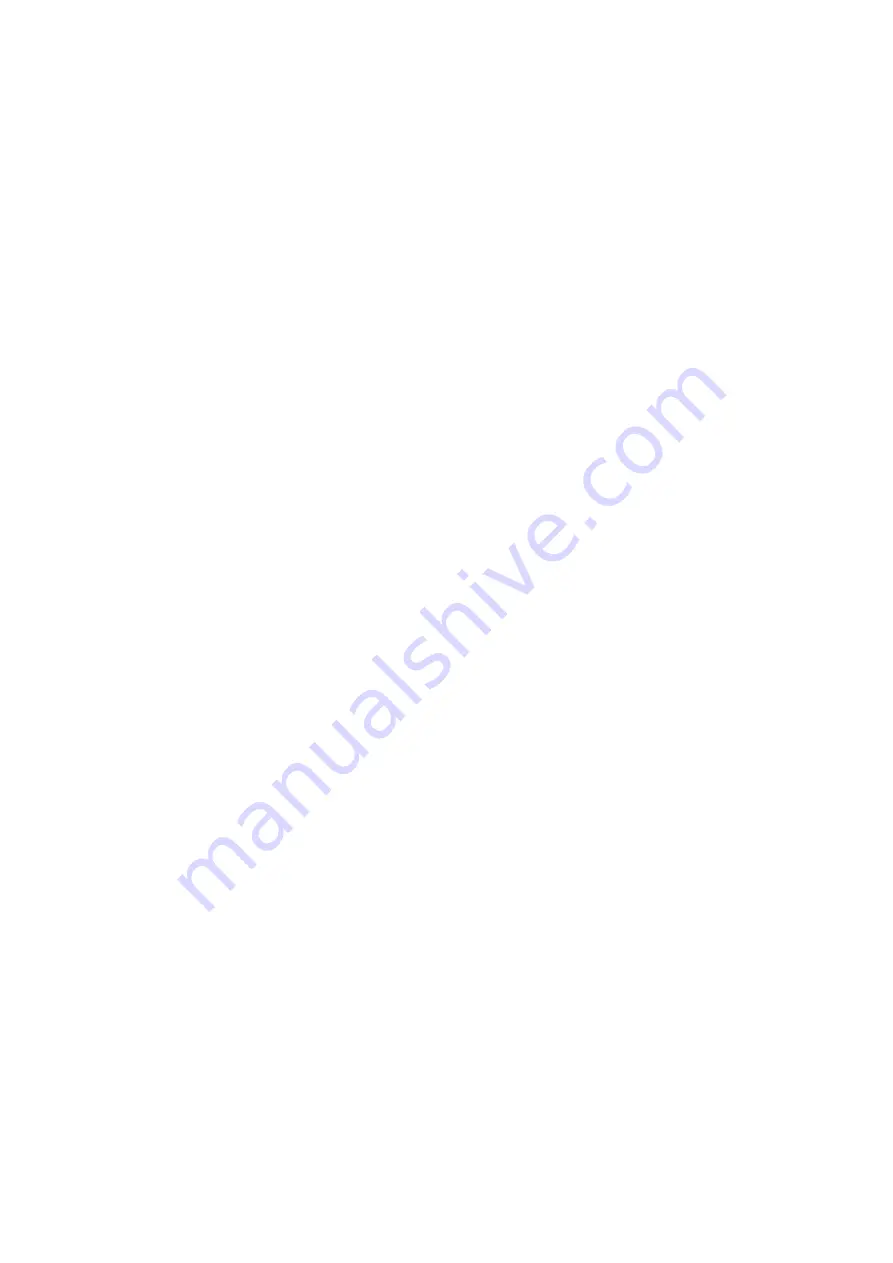
5
GENERAL SAFETY RULES FOR
WOODWORKING MACHINERY (1)
1.
Know your machine. For your own safety, read the operation manual
carefully. Learn its applications and limitations, as well as specific
potential hazards pertinent to this machine.
2.
Make sure the machine is properly grounded.
3.
Keep guards in place and in working order. If a guard must be removed
for maintenance or cleaning, make sure it is properly reattached before
using the machine again.
4.
Remove adjusting keys and wrenches. Form habit of checking to see that
keys and adjusting wrenches are removed from the machine before
turning it on.
5.
Keep work area clean. Cluttered areas and workbenches increase the
likelihood of an accident.
6.
Do not use in dangerous environments. Do not use machine in damp or
wet locations, or expose them to rain. Keep work area well illuminated.
7.
Keep children away. All visitors should be kept at a safe distance from
work area.
8.
Make workshop childproof. With padlocks, master switches, or by
removing starter keys.
9.
Do not force the machine. It will do the job better and be safer at the rate
for which it was designed.
10.
Use the right tools. Do not force the machine or attachments to do a job
for which they were not designed. Contact the manufacturer or distributor
if there is any question about the machine's suitability for a particular job.
11.
Wear proper apparel. Avoid loose clothing, gloves, neckties, rings,
bracelets, or jewelry which could be caught in moving parts. Nonstop
footwear is recommended. Wear protective hair covering to contain long
hair.
12.
Always use safety glasses, also use face or dust mask if operations is
impact resistant lenses. They are not safety glasses.
13.
Secure work.
14.
Keep proper footing and balance at all times.
Summary of Contents for 5018
Page 1: ...5018 18 Cutoff Saw...
Page 4: ...1 WARNING LABEL LOCATIONS...
Page 14: ...11 CUTTING CAPACITY DIAGRAM...
Page 40: ...37 REPLCING V BELT 2 Belts Spindle Pulley Motor Pulley Inside Flange...
Page 46: ...43 ELECTRIC WIRING DIAGRAM 230V 60HZ...
Page 47: ...44 AIR CIRCUIT DIAGRAM...
Page 48: ...45 PART LIST...
Page 50: ...47 PART LIST...