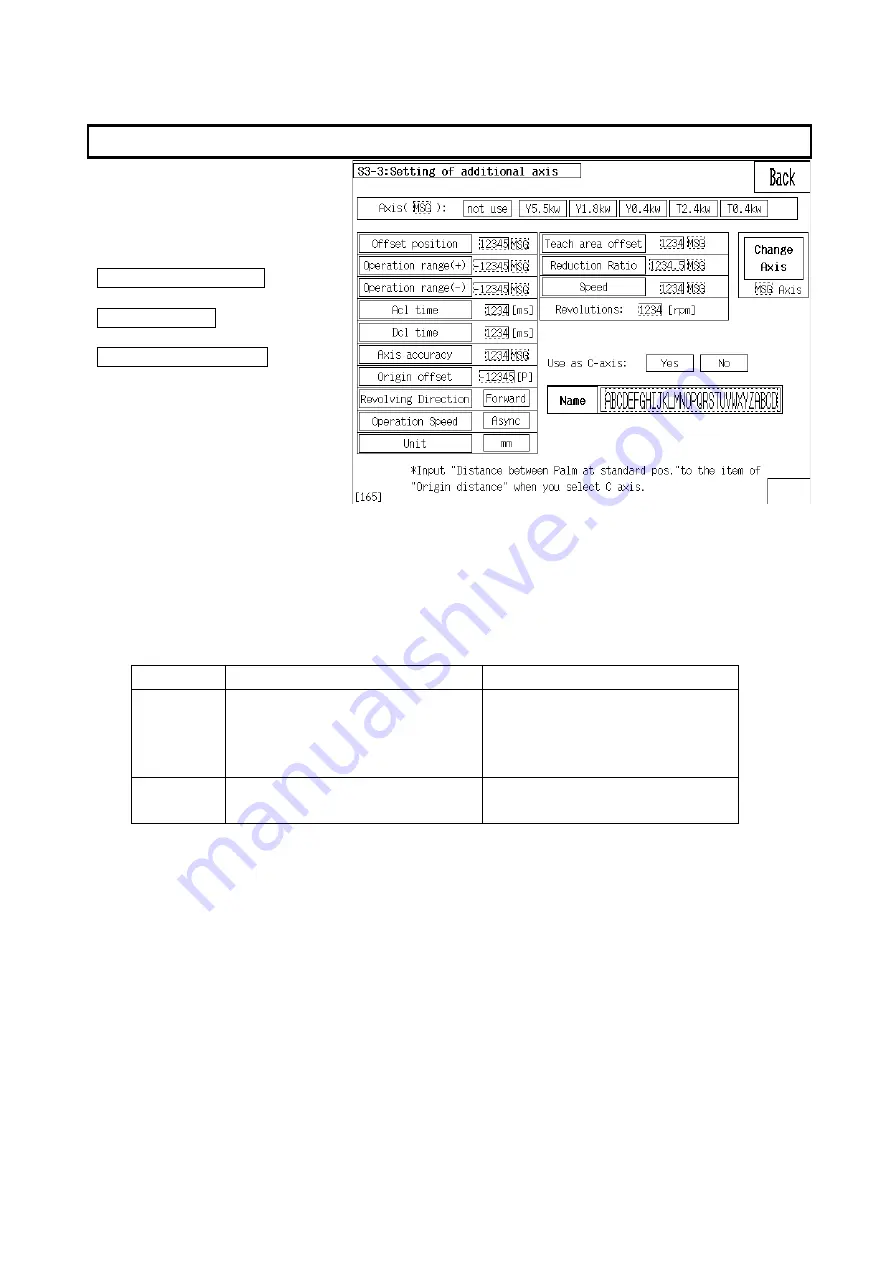
5-17
5.14.
Expansion Axis Setting
This screen is for setting
expansion axis.
The directory to expansion axis
setting is as follows.
System storage menu
↓
Motor axis data
↓
Expansion axis setting
Note) Amp unit is required to add expansion axis.
1.
Set expansion axis
Select type of servo motor to be installed.
2.
Relationship between expansion axis and C axis
What is difference from expansion axis to be used as C axis from not as C axis.
For C axis
Not for C axis
Control
method
Robot sequence commands
(
HMOV/HMOVD/TRQC
)
*Can be synchronized with
robot sequence.
Built-in PLC commands
(
EXMOVA/EXMOVR
)
Step
storing
Store per every program
Max 9 steps per a program
Stored per every axis
Max 99 steps per a axis
3.
Coordinates offset
・
For the expansion axis that [Not use as C axis] is selected, enter the distance of offset
off the position where encoder origin is stored. Normally don’t need to enter as those
are the exact same position.
・
For the expansion axis that [Use as C axis] is selected, enter the distance between
palms (paddles) where encoder origin is stored. Normally don’t need to enter as those
are the exact same position.
4.
Operation range+-
Enter operation range for the expanded area.
5.
Acceleration / deceleration time
Enter Acceleration / deceleration time.
6.
Axis accuracy
Summary of Contents for A Series
Page 2: ...History Version Date Content Page 01 2012 04 24 First edition...
Page 4: ......
Page 10: ......
Page 11: ...2 1 2 Harness Cable Connection...
Page 25: ...3 7 3 4 Contactor Unit MCRU 1 UL CE Neither LED nor jumper pin is on contactor unit...
Page 30: ......
Page 31: ...4 1 4 Adjustments...
Page 55: ...6 1 6 Maintenance Functions Maintenance on Touch panel POD is explained...
Page 74: ......
Page 76: ......
Page 77: ......