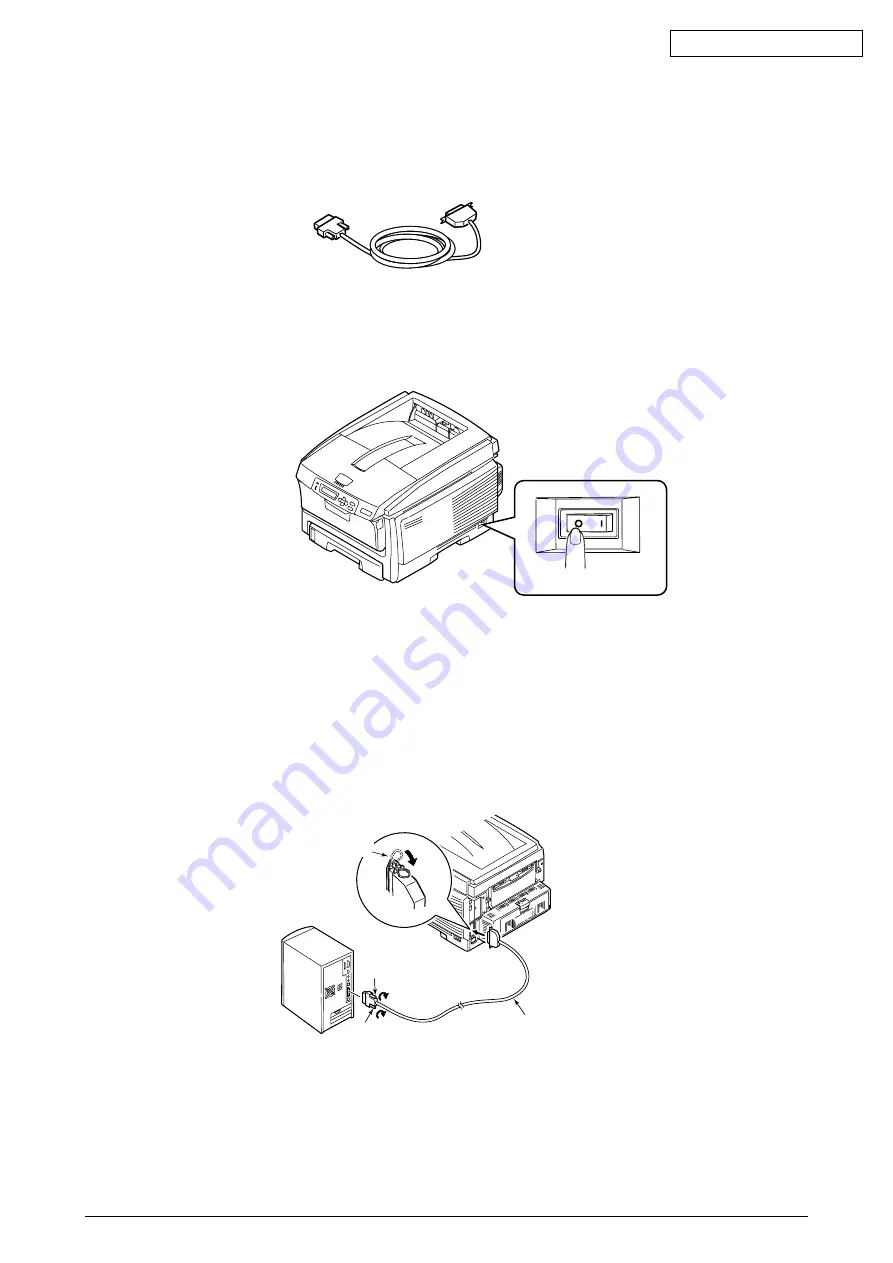
43827101TH Rev.2
65 /
Oki Data CONFIDENTIAL
<Parallel Connection> (Centronics I/F model)
1. Prepare a parallel cable.
2. Power off Printer and Personal Computer
3. Connect Personal Computer and Printer
(1)
Connect a parallel cable into a parallel interface connector of printer and use metal fittings to
secure the cable.
(2)
Connect a parallel cable into a parallel interface connector of PC and use screw to secure the
cable.
O
I
OFF
Parallel cable
Screw
Screw
Metal fittings