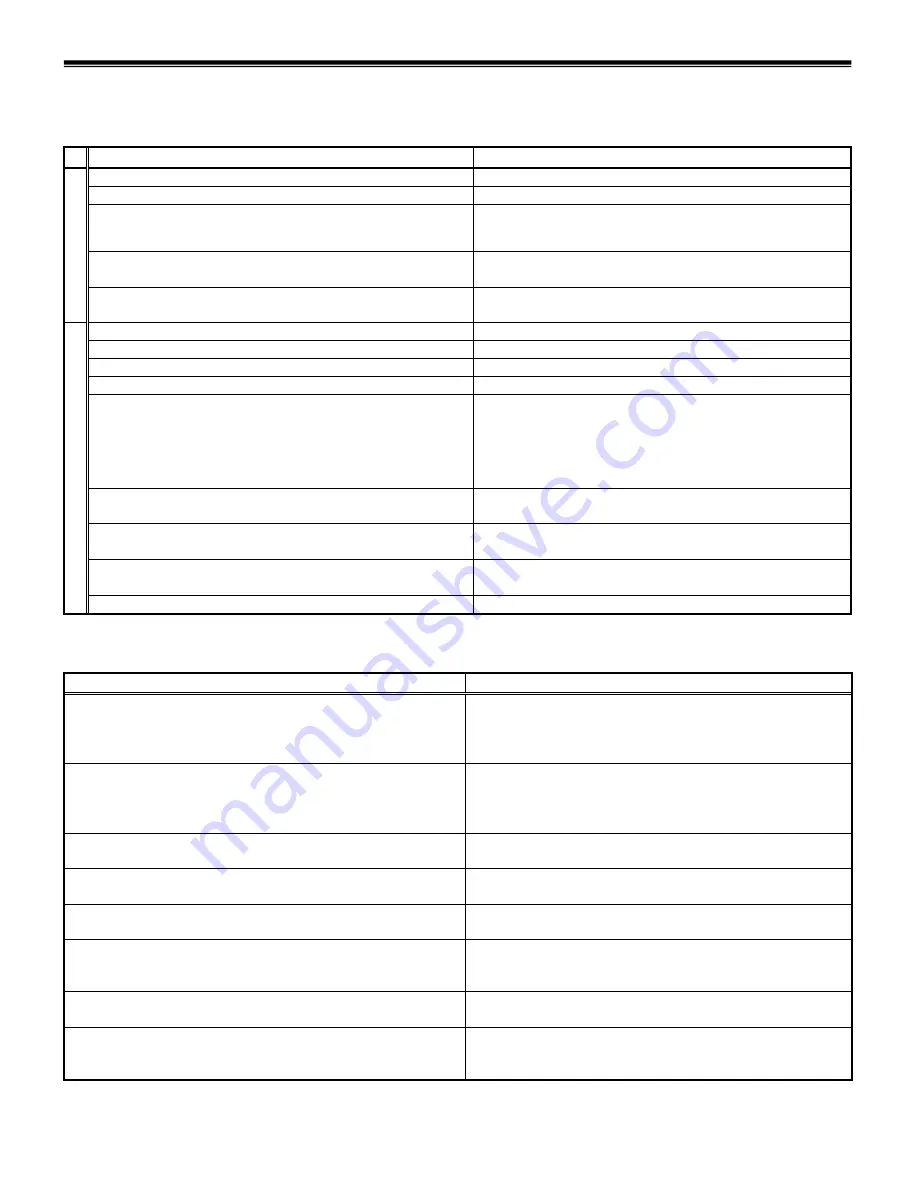
30
4. MAIN CAUSES AND SUGGESTED REMEDIES FOR A DECREASE IN NUMBER BLOWS
AND IMPACT FORCE
MAJOR CAUSES
SUGGESTED REMEDIES
B
reak
er
Improper pressure of the sealed gas.
Regulate the sealed gas to the correct pressure.
Wear of shank bushing beyond limit.
Replace the shank bushing.
Wear beyond limit, damage or deformation of the striking
surface of the piston, and the shank section, impact receiving
surface and tip of chisel.
Replace the piston or chisel (use only genuine parts).
Damage or wear of cylinder, piston, cylinder sleeve,
valve, valve box and valve box sleeve.
Repair flaws with an oil stone or polishing paper or
replace.
Insufficient gas pressure of accumulator or damaged
bladder.
Recharge nitrogen gas or replace the bladder.
E
xca
va
to
r
Half opening of stop valve.
Fully open the valve.
Clogging by foreign matter in the piping.
Disassemble and remove foreign matter.
Lack of hydraulic oil.
Replenish with the same hydraulic oil.
Deterioration or contamination of hydraulic oil.
Replace all oil with fresh oil.
Defective operation or improper set pressure of the
main relief valve and secondary relief valve.
Send the main relief valve to the manufacturer’s designated
service factory for adjustment.
Regulate the secondary relief valve to correct the set
pressure.
Or repair or replace the damaged spring, seat, valve or
piston.
Insufficient discharge and pressure owing to a hydraulic
pump malfunctioning.
Send the excavator pump to the manufacturer’s
designated service factory for repair.
Use of the excavator when oil temperature is above
80
°
C (176
°
F).
Avoid using the hydraulic breaker if the oil temperature
is above 80
°
C (176
°
F).
Disorderly operation of the pressure valve in the tank,
and clogging of cooler fins or filter elements.
Send these parts to the manufacturer’s designated
service factory for repair or replacement.
Improper selection and damage of directional valve.
Repair or replace.
EARLY WEAR AND DAMAGE OF PARTS
MAJOR CAUSES
PLACES
Lack, deterioration or contamination of hydraulic oil or use
of regenerated oil.
Damage or formation rust on the cylinder, piston, valve,
valve box and cylinder sleeve.
Damage or wear of relief valves, pump or operating
valve.
Entry of foreign matter during mounting or dismounting of
the breaker, insufficient oil flushing after installation of
piping, or entry of drains in the hydraulic oil tank.
Damage to the sliding parts between the cylinder and
piston, and the sliding parts of the valve.
Damage to the U-packings, clogging of the filter
elements or damage to the relief valves
Abnormal rise of oil temperature.
Deformation or hardening of the U-packings and
O-rings.
Insufficient greasing.
Damage and wear of shank bushing, the shank section
of the chisel, and front cap bushing.
Loosening of screwed parts owing to insufficient or
uneven tightening.
Wear and breakage of bolts, or gas leakage.
Excessive prying of chisel during operation.
Damage to the cylinder and piston, wear of the shank
bushing, and front cap bushing, or failure of chisel or
side rod.
Continuous blowing for more than 1 minute.
Breakage of bolts, wear of chisel or damage of relief
valves and pump, and striking surface of piston.
Underwater use of a breaker with standard specification
Embrittlement of U-packings, damage to the cylinder
and piston (contamination of hydraulic oil or damage to
the hydraulic apparatus of the excavator).