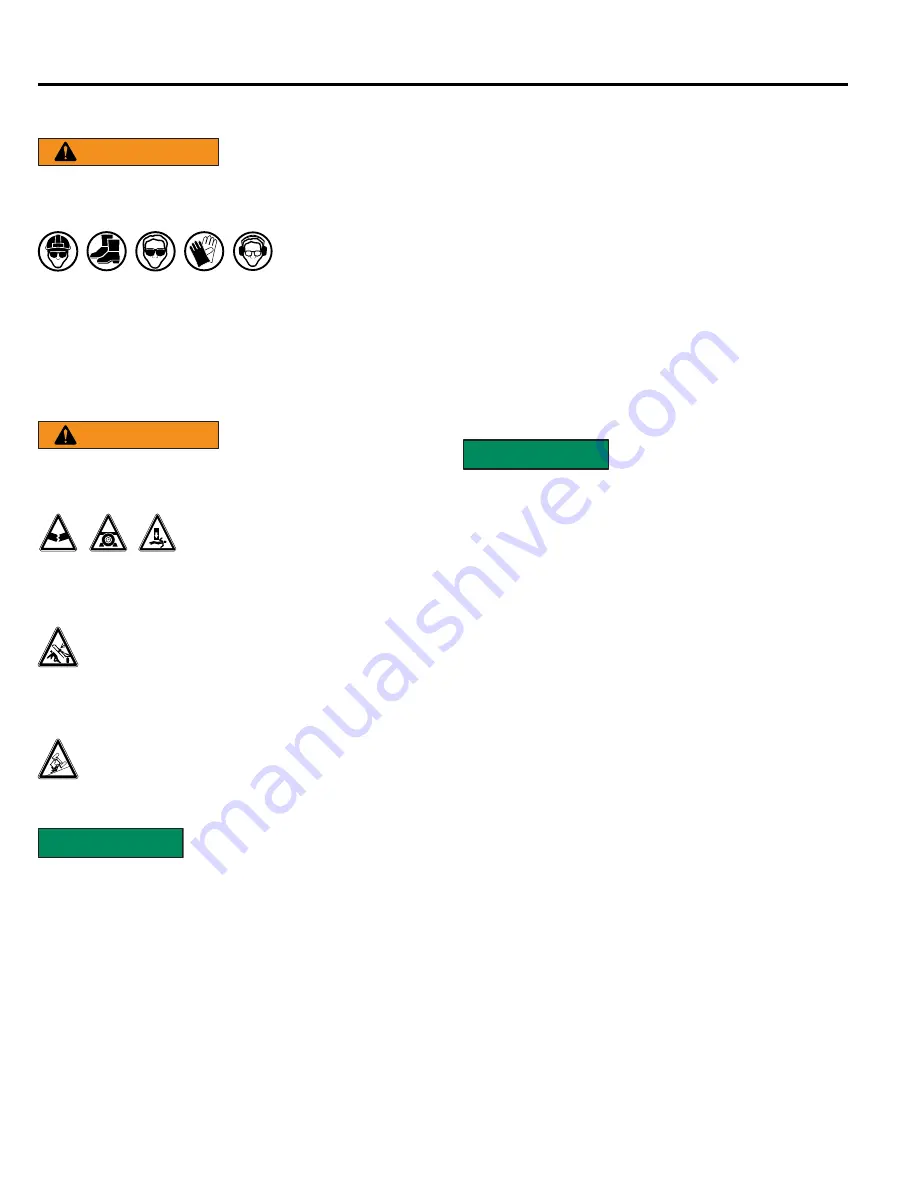
Ogden Metalworks, Inc. — 217-582-2552
30
Hay Runner™ Hay Rake
9. Maintenance
9.1 General Maintenance Safety
WARNING
Failure to comply with
the following safety
instructions could result in serious injury and
possibly even death.
Personal
Protection
Equipment
Wear personal protection equipment (PPE),
which may include hard hat, safety glasses,
safety shoes, gloves, etc. appropriate for the
work site and working conditions.
9.2 Work Area
WARNING
Failure to comply with
the following safety
instructions could result in serious injury and
possibly even death.
Crush Hazard
Always set the wheel rake on
safety stands or on the
ground and chock the wheels when performing
maintenance.
Crush hazard
The rake arms can drop unexpectedly if
the wing locks are not installed. Whenever
the wings are raised the transport locks, and
their retaining pins must be installed.
The wheel rake is top heavy when the
wings are raised. Make sure the rake is on
a firm, level surface before performing any
maintenance.
SAFETY
INSTRUCTIONS
The following safety
instructions are provided to
help prevent injury or limit equipment damage.
A fire extinguisher and first aid kit should be
readily accessible while performing maintenance
on this equipment.
Do not leave tools lying around the work area.
Follow good shop practices. Keep service area
clean and dry. Be sure electrical outlets and
tools are properly grounded. Use adequate light.
Keep all parts in good condition and properly
installed. Fix damage immediately. Replace worn
or broken parts.
Use the correct tools, jacks, hoists, or other
tools that have the capacity for the job.
Use certified safety stands rated to support the
wheel rake’s weight when working beneath the
wheel rake.
Do not position jack stands under moveable
parts. Test the stability of the wheel rake before
working underneath.
If the wheel rake is attached to the tractor, set
the brakes, remove the key, chock the tractor
wheels, and block the wheel rake before working
underneath.
9.3 Parts Replacement
SAFETY
INSTRUCTIONS
Replacement parts must be
genuine factory replacement
parts to restore the unit to its original
specifications. The manufacturer will not accept
responsibility for damages as a result of using
unapproved parts.
Replace any worn, cut, abraded, flattened, or
crimped hoses.
Summary of Contents for RCR812
Page 2: ......
Page 15: ...Hay Runner Hay Rake 13 Ogden Metalworks Inc 217 582 2552 5 6 ...
Page 40: ...Ogden Metalworks Inc 217 582 2552 38 Hay Runner Hay Rake 11 2 Wheel Rake Frame ...
Page 44: ...Ogden Metalworks Inc 217 582 2552 42 Hay Runner Hay Rake 11 5 Single and Tandem Axles ...
Page 49: ...Hay Runner Hay Rake 47 Ogden Metalworks Inc 217 582 2552 NOTES ...
Page 50: ...Ogden Metalworks Inc 217 582 2552 48 Hay Runner Hay Rake NOTES ...
Page 51: ......