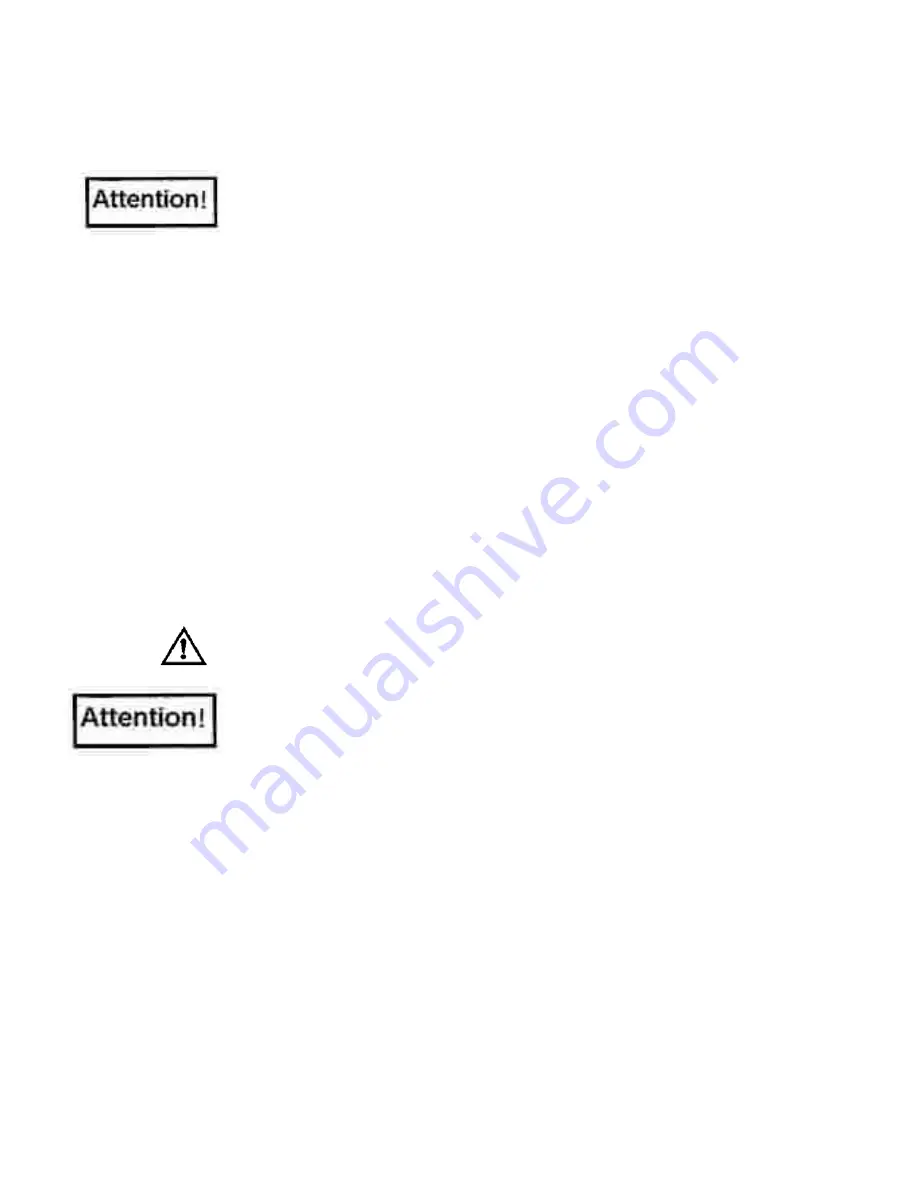
13
Strainer
A strainer (6) is installed at the water inlet of the machine which must be
checked and cleaned, respectively replaced whenever needed.
Severe damage on pump set and control units can be caused by
running the machine with polluted feed water and/or clogged strainer.
Frost Protection
Frost-protection of the machine is of vital interest, as frost can cause severe
damage on the entire system.
The best frost protection is to store the machine/accessories in a permanently
frost-protected area.
If there is a risk of temperatures below freezing point during storage and/or
transportation, the machine to be frost-protected as follows:
•
2 l of a 1 : 1 water/anti-freeze liquid (e.g. Glysantin) to be mixed in a clean
vessel. Put water supply hose into the vessel and start the high pressure
pump.
•
Spray pistol/stop valve to be opened in order to circulate the anti-freeze
liquid.
•
Spray pistol/stop valve to be opened and closed several times in order to
also fill safety/control valve with anti-freeze liquid.
•
Stop high pressure pump and disconnect all hoses.
•
Machine is now protected against temperatures of –30 °C.
Disregarding of frost-protection instructions can cause severe
damage on the entire system.
Anti-freeze liquid to be collected for re-use, respectively to be
dumped properly according to safety regulations.