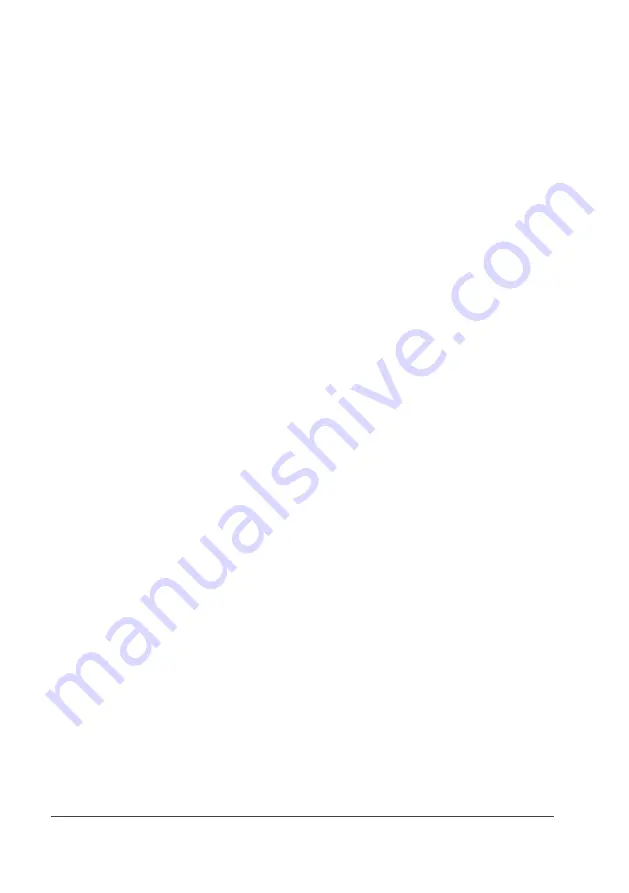
18
WHO TO
CONTACT
WHO TO CONTACT FOR HELP
Before you call for help and to avoid unnecessary call out fees, check these items
before you call for assistance:
1. Is the power turned ON at the plant?
2. Are there lights ON in the panel face?
3. Has a Safety Switch, not related to the plant, tripped in your switchboard?
4. Has the outlet hose become kinked, preventing the plant pumping out?
5. Is the outlet dripper filter blocked?
If you have an issue, you can try to reset the system with the following sequence:
a) Turn the system OFF using the control panel ON/OFF switch on the side of the
panel. This will reset the programme.
b) Turn the system ‘ON’ using the ON/OFF switch.
c) If the system starts and operates correctly, observe the system over the next few
days for another ALARM event and discuss it with your Service Agent.
d)
If the system goes back into the ALARM mode, call your Service Agent.
Limit your water usage until the fault is rectified.
For Assistance or for your closest Service Agent call Head Office on:
03 344 0262
0800 48 48 49
(if no answer please leave your name and number on the answerphone).