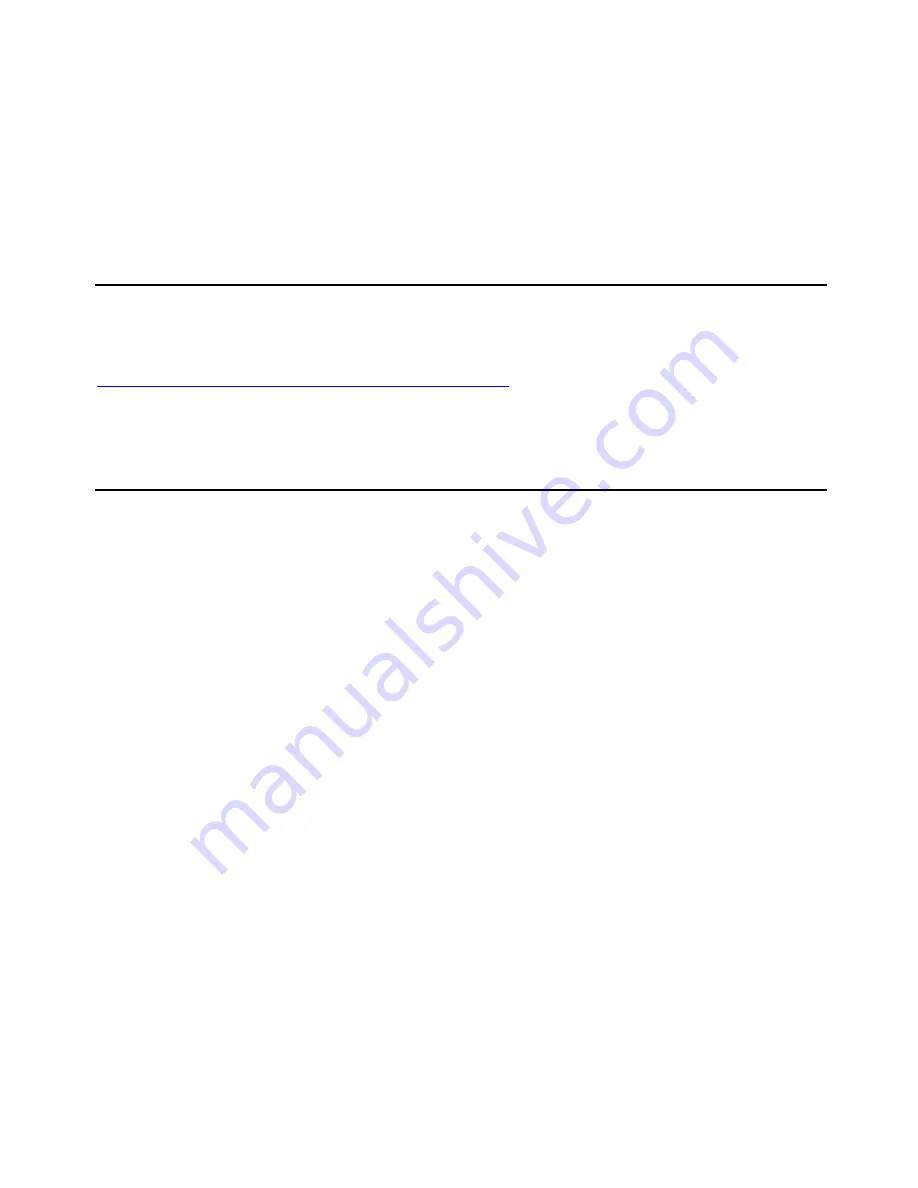
30 QuantumDrive-4000 Manual
91-0027 Rev. E
Copyright © Nutfield Technology, Inc.
6/2010
13. Service
And
Support
Your satisfaction is important to us. If you need assistance please contact your local
representative first. If the local representative is unable to assist you, contact NTI at the
address below.
13.1 Product Return Procedure
If a product is to be returned to the factory, please go to our web-site:
http://www.nutfieldtech.com/nutfield/service.asp
and fill out the RMA request form.
13.2 Contact Information
Nutfield Technology, Inc.
1 Wall St., Suite 113
Hudson, NH 03051
TEL: 603-893-6200
FAX: 603-893-6214
www.nutfieldtech.com