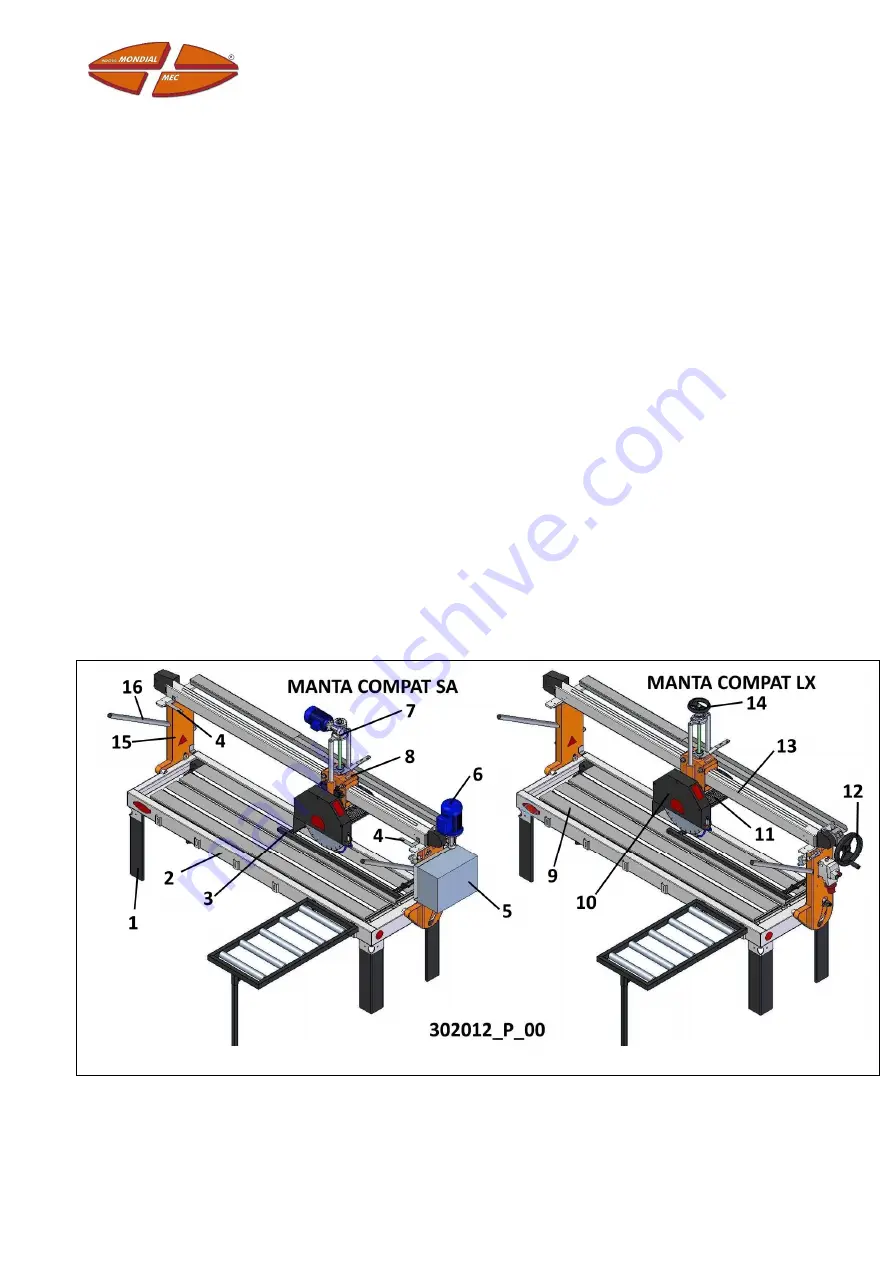
Page
34
of
87
301006_R00_IT
7.1
Description of the Machine
Machine MANTA COMPAT 200-250-300 is an electrical sawing machine that allows the cut of each
stony material for the construction industry.
The main feature that distinguishes the MANTA COMPAT 200-250-300 machine lies in the
affordability, versatility, simplicity and, at the same time, robustness.
Suitable for both small workshop and large industry.
The sawing machine MANTA COMPAT 200-250-300 is available in two versions:
1) Manual version LX
2) Semi-automatic version SA.
The cutting of the material takes place by:
1) Positioning the workpiece on the work surface manually by the operator.
2) Longitudinal movement of the cutting head (X-axis) by the operator by means of belt
transmission actuated by a mechanical hand wheel in the LX manual version, and using
instead a gear motor with electronic speed variator for the semi-automatic SA version.
3) Adjustment the cutting height (Z-axis) by hand wheel for LX manual version, powered by
geared motor for semi-automatic SA version.
4) The two motorized movements in the semi-automatic version are executed with a single
control device (joystick) by the operator on the switchboard.
5) The piece remains fixed, the tool is moving during cutting.
For these unique features, the machine takes the name of "bridge saw."
Possibility of inclination of the head for cuts from 90 ° to 45 ° by moving the entire electric motor unit
by means of a lever placed on the shoulders.
Cutting takes place by means of a water recirculating cooling system powered by electric pumps
submerged in the tub formed directly on the machine base.
The structure and the base is made of painted steel, the work bench is made of galvanized steel. The
cutter is raised on fixed angular legs with the possibility of being dismantled.
The machine must be moved and raised exclusively with lifting equipment as described in Chapter 8
of the manual.
7.1.1 Composition of the Machine
Machines are composed of the following units
Image 3 Machine Units
Summary of Contents for MANTA COMPAT 200 LX
Page 78: ...Page 78 of 87 301011_R00_IT ...
Page 79: ...301011_R00_IT Page 79 of 87 ...
Page 80: ...Page 80 of 87 301011_R00_IT ...
Page 81: ...301011_R00_IT Page 81 of 87 ...
Page 82: ...Page 82 of 87 301011_R00_IT ...
Page 83: ...301011_R00_IT Page 83 of 87 ...
Page 84: ...Page 84 of 87 301011_R00_IT ...
Page 85: ...301011_R00_IT Page 85 of 87 ...
Page 86: ...Page 86 of 87 301011_R00_IT ...