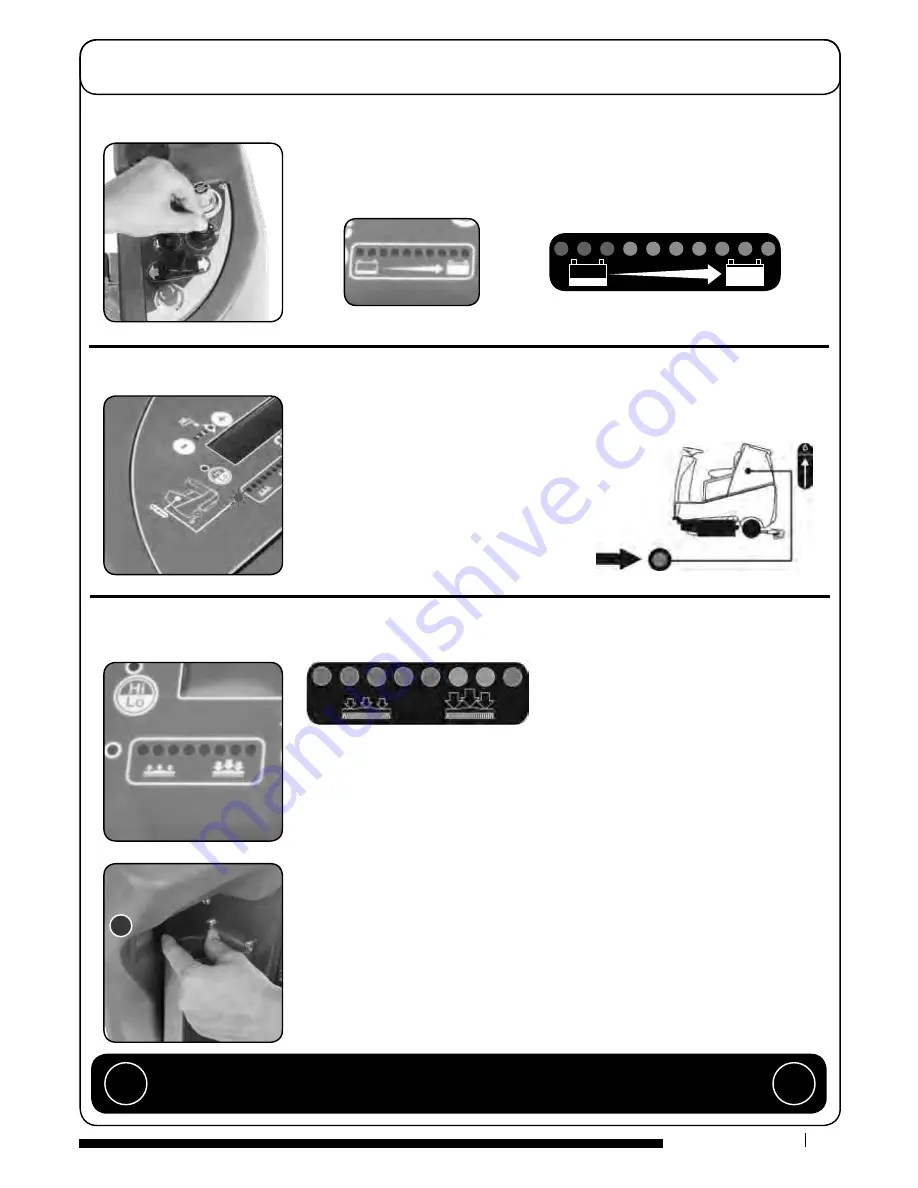
Machine Operation
11
T 01460 68600
Insert the key into the ignition and quarter-turn it clockwise to position (1) ‘ON’.
The battery charge-level indicator will illuminate.
Setting the Cleaning Controls
Waste-water Tank Fill Level Warning Light
When the waste-water tank becomes full, a red warning light will
illuminate on the operator control panel (as illustrated) and the
vacuum motor will stop automatically.
The waste-water tank requires emptying
(see page 16)
.
The machine is equipped with a brush-pressure load-warning system.
If the brush load increases due to changing floor types, the pressure can be
adjusted manually by the operator using the adjuster knob found on the left hand
side of the control column.
Turn it anti-clockwise to decrease load on the brushes and clockwise to increase
load/pressure on the brushes
(see Fig.28).
Note: The run-time of the machine may decrease
if the load on the brushes is increased.
Brush pressure / Load adjustment
28
Note:
The run-time of the machine may decrease if the load on the brushes is increased.
!
!
Summary of Contents for TRO 650/200T
Page 3: ...Machine Overview 13 14 6 12 22 21 18 19 20 16 17 11 10 9 2 3 4 5 6 7 8 15 23 ...
Page 27: ...EU Declaration of Conformity 27 T 01460 68600 ...
Page 28: ...Warranty 28 www numatic co uk ...
Page 29: ...Notes 29 T 01460 68600 ...
Page 30: ...Notes 30 www numatic co uk ...
Page 31: ...Notes 31 T 01460 68600 ...