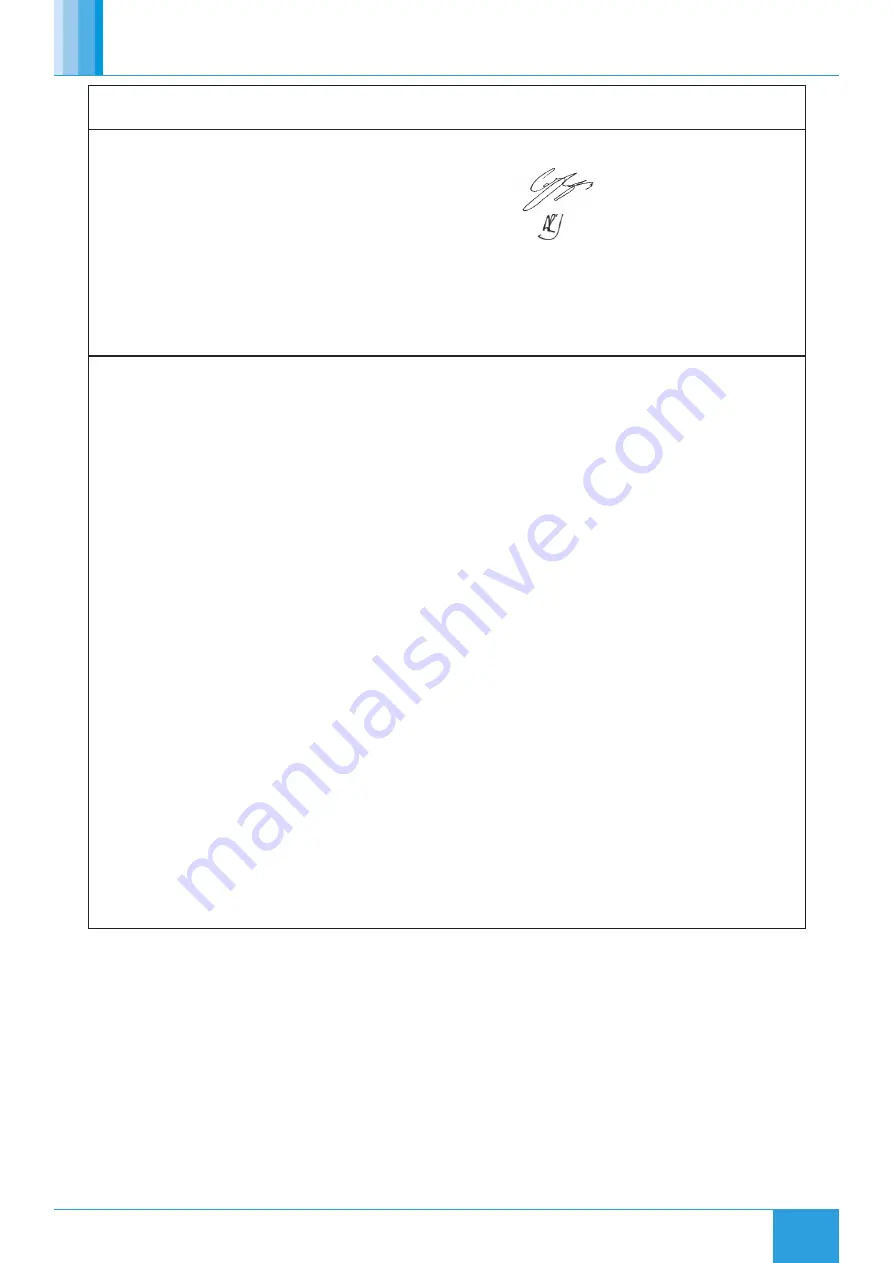
7
06. 10. 20. Document Number 671139
Nuaire |
Western Industrial Estate
|
Caerphilly
|
CF83 1NA
|
nuaire.co.uk
ES-OPUSDC
Installation Manual
1.0
1.1
To comply with EC Council Directives 2006/42/EC Machinery Directive and
2014/30/EU (EMC).
To be read in conjunction with the relevant Product Documentation (see 2.1)
2.0 INFORMATION SUPPLIED WITH THE EQUIPMENT
2.1
2.2 Each unit has a rating plate attached to its outer casing. The rating plate
Each item of equipment is supplied with a set of documentation which provides
the information required for the safe installation and maintenance of the
equipment. This may be in the form of a Data sheet and/or Installation and
Maintenance instruction.
GENERAL
The equipment referred to in this Declaration of Incorporation
is supplied by
Nuaire to be assembled into a ventilation system which may or may not include
additional components.
The entire system must be considered for safety purposes and it is the
responsibility of the installer to ensure that all of the equipment is installed in
compliance with the manufacturers recommendations and with due regard to
current legislation and codes of practice.
provides essential data relating to the equipment such as serial number, unit
code and electrical dat a. Any further data that may be required will be found
in the documentation. If any item is unclear or more information is required,
contact Nuaire.
3.1
2.3 Where warning labels or notices are attached to the unit the instructions given
mus t be adhered to.
3.0 TRANSPORTATION, HANDLING AND STORAGE
3.2 When handling the equipment, care should be taken with corners and edges and
Care must be taken at all times to prevent damage to the equipment. Note that
shock to the unit may result in the balance of the impeller being affected.
that the weight distribution within the unit is considered. Lifting gear such as
slings or ropes must be arranged so as not to bear on the casing.
4.1
4.2 Where installation accessories are supplied with the specified equipment eg.
It is important that the specified operational limits for the equipment are
adhered to e.g. operational air temperature, air borne contaminants and unit
orientation.
3.3 Equipment stored on site prior to installation should be protected from the
weather an d steps taken to prevent ingress of contami nants.
4.0 OPERATIONAL LIMITS
wall mounting brackets. They are to be used to support the equipment only.
Other system components must have separate provision for support.
5.0 INSTALLATION REQUIREMENTS
have no adverse effect on the fan. The speed will return to normal once the
interference has subsided.
4.3 Flanges and connection spigots are provided for the purpose of joining to
duct work systems. They must not be used to support the ductwork.
4.4 In the event of RF interference the fan may change speed. This is normal and will
5.1
5.2
The electrical installation of the equipment must comply with the requirements
of the relevant local electrical safety regulations.
5.3
For EMC all control and sensor cables should not be placed within 50mm or on
the same metal cable tray as 230V switched live, lighting or power cables and
any cables not intended for use with this product.
In addition to the particular requirements given for the individual product, the
following general requirements should be noted.
Where access to any part of equipment which moves , or can become electrically
live are not prevented by the equipment panels or by fixed installation detail
(eg ducting), then guarding to the appropriate standard must be fitted.
6.0 COMMISSIONING REQUIREMENTS
6.1
General pre-commissioning checks relevant to safe operation consist of the
7.1
7.0
OPERATIONAL REQUIREMENTS
6.2
Other commissioning requirements are given in the relevant product documentation.
7.2
following:
Ensure that no foreign bodies are present within the fan or casing.
Check electrical safety. e.g. Insulation and earthing.
Check guarding of system.
Check operation of Isolators/Controls.
Check fastenings for security.
Equipment access panels must be in place at all times during operation of the
unit, and must be secured with the original fastenings.
If failure of the equipment occurs or is suspected then it should be taken out of
service until a competent person can effect repair or examination. (Note that
certain ranges of equipment are designed to detect and compensate for fan failure).
conditions.
8.5
Care should be taken when removing and storing access panels in windy
before access panels are removed. This will allow the impeller to come to rest.
NB: Care should still be taken however since airflow generated at some
other point in the system can cause the impeller to “windmill” even when
power is not present.
8.0 MAINTENANCE REQUIREMENTS
8.1
Specific maintenance requirements are given in the relevant product documentation.
8.2
It is important that the correct tools are used for the various tasks required.
8.3
If the access panels are to be removed for any reason the electrical supply to the
unit must be isolated.
8.4 A minimum period of two minutes should be allowed after electrical disconnection
INFORMATION FOR SAFE INSTALLATION, OPERATION AND MAINTENANCE
OF NUAIRE VENTILATION EQUIPMENT
DECLARATION OF INCORPORATION AND INFORMATION
FOR SAFE INSTALLATION, OPERATION AND MAINTENANCE
Designation of machinery:
Machinery Types:
I & M Serial No.:
ES-Opus DC
ES Opus DC 40-M, 60-M, 40-2M,
60-2M, 75-M, 110-M
671339
Applied National Standards:
BS EN ISO 13857
BS848 Parts 1, 2.2 and 5
Relevant EC Council Directives:
2006/42/EC (Machinery Directive)
Applied Harmonised Standards:
BS EN ISO 12100, BS EN ISO 9001,
We declare that the machinery named below is intended to be assembled
with other components to constitute a system of machinery. All parts
except for moving parts requiring the correct installation of safety guards
comply with the essential requirements of the Machinery Directive. The
machinery shall not be put into service until the system has been
declared to be in conformity with the provisions of the EC Machinery
Directive.
Date:
Signature of manufacture representatives:
Name:
Position:
31. 12. 10
Technical Director
1) C. Biggs
2) A. Jones
31. 12. 10
Manufacturing Director
Note: All standards used were current and valid at the date of signature.