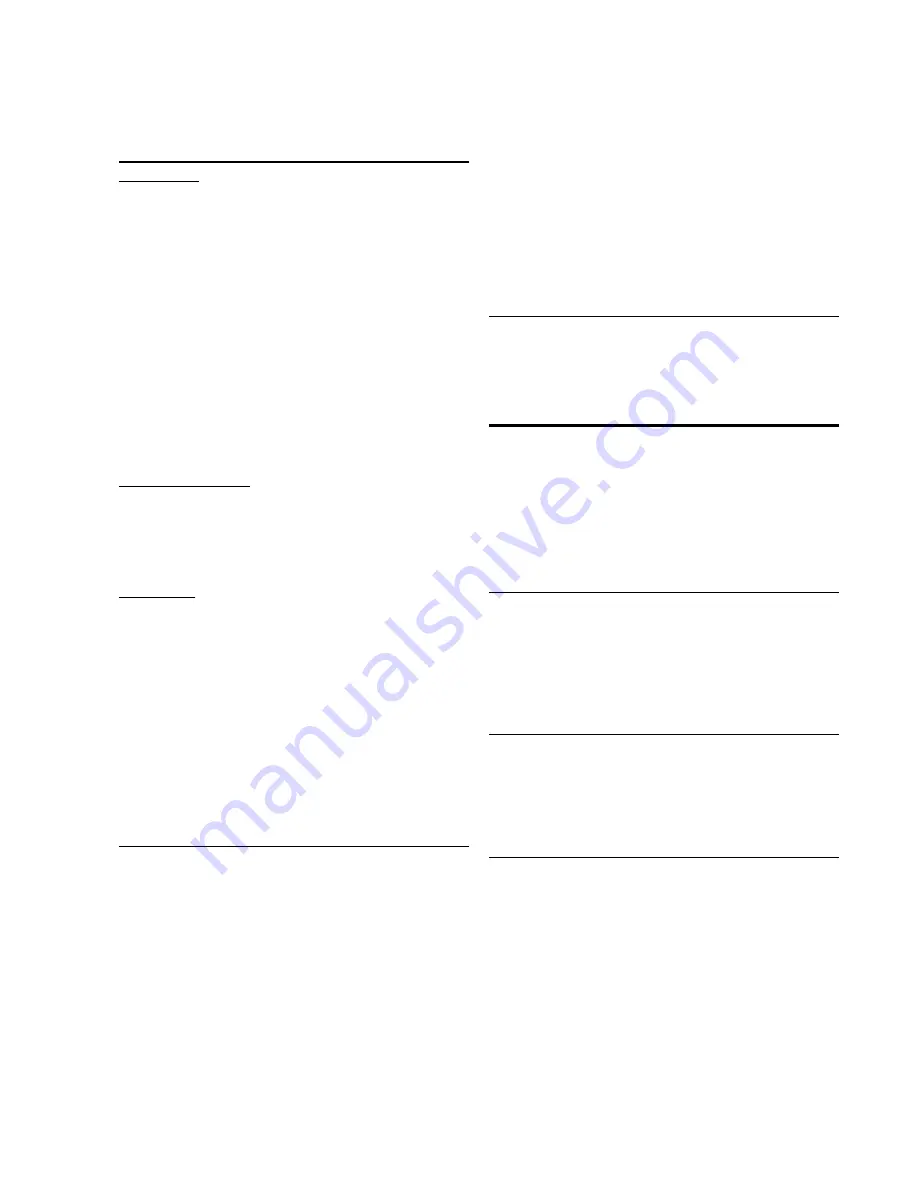
Page E.3
PO Series Operation And Maintenance
Clean the fan blades with a stiff brush, taking care
not to damage them. Inspect the burner air inlet and
ensure that there is no obstruction to the air flow.
Replace the plate and retaining nuts.
Burner Inner Assembly
Air Diffuser
Remove the burner air diffuser plate for inspection
and cleaning as follows: -
1.
Remove the PE cell from its holder and secure
to a safe place.
2.
Fit the three guide rods through the sockets
on the front plate.
3.
Loosen and remove the 4 nuts and washers
securing the backplate to the burner casing.
4.
Pull the backplate assembly rearwards,
guiding the inner tube until the diffuser is
clear of the burner head casing
5.
Clean the diffuser of any deposits using a
stiff brush.
Ignition Electrodes
Clean and check the electrodes are not cracked or
worn. Renew if necessary.
Check the settings of the ignition electrodes and
reset if necessary, details are shown on Page C.16.
Oil Nozzle
Remove the oil nozzle, dismantle it and wash the
internal filter and other components in a suitable
solvent. Remove any remaining deposits with a clean,
lint-free cloth. The oil nozzle should be replaced after
2000 hours operation.
Re-assemble the inner assemblies in reverse order.
Replace all covers and secure all fittings. The burner
is now ready for operation and remove the guide
rods. Switch on the electrical and fuel supplies to
the burner.
Oil Filters
The oil filter located on top of the preheater should
be removed and cleaned in paraffin or another
suitable solvent.
SAFETY WARNING : CLASS ‘G’ OIL BURNERS
OPERATE WITH OIL AT 140°C FOR
ATOMISATION. THE BURNER SYSTEM SHOULD
BE TAKEN OFF LINE AND ALLOWED TO COOL
BEFORE ATTEMPTING THESE TASKS.
In the case of the cold oil filter, remove the plug
from the sump and drain off any sludge and/or
water present at six-weekly intervals. The cleaning
knob on this filter should be rotated daily. If the
filter fitted in the oil supply line has a disposable
element this should be replaced at least once a
year, more frequently if this is dictated by the
condition of the fuel or other local conditions. If
the filter element is re-usable it should be cleaned
at appropriate intervals. After filter cleaning
operations it will be necessary to remove air from
the system by bleeding the pump.
Oil Preheater
Regular checks should be made to ensure that the
oil temperature is maintained at the correct level
(refer to the table on Page B.8).
FFFFF
A
AA
AAUL
UL
UL
UL
ULTTTTT
F
F
F
F
F
INDING
INDING
INDING
INDING
INDING
Any changes made in control settings as a result of
identifying and remedying fault conditions as
described below may necessitate partial or
complete recommissioning. Recommissioning
shall be undertaken only by appropriately qualified
and experienced personnel
.
Modulating System
If malfunction of the modulating controller
(RWF40) is suspected, check that only a
compatible pressure/temperature detector has
been used. If problems persist then replacement
of the unit should be considered.
Incorrect Rotation of the Fan Motor
The fan motor rotates in the direction of the arrow
printed on the Nu-way nameplate mounted on the
fan casing. If the direction of rotation is incorrect,
interchange any two phases.
Fan Motor Fails To Start
Check that :
-
The electricity supply is available
-
The burner is correctly wired
-
The fuses are correctly sized and not blown
-
The motor overload is not tripped
-
The burner controller is not locked out
-
The appliance controls are calling for heat
-
The oil preheater thermostats and oil
temperature
Summary of Contents for PO160
Page 5: ...Page B 1 PO Series General Information GENERAL INFORMATION ...
Page 14: ...Page B 9 PO Series General Information ...
Page 15: ...PO Series General Information Page B 10 AAD PFinal B_Gen PO B_Gen pmd 250504A ...
Page 16: ...Page C 1 PO Series Technical Specification TECHNICAL SPECIFICATION ...
Page 34: ...Page C 19 PO Series Technical Specification ...
Page 35: ...PO Series Technical Specification Page C 20 AAD PFinal C_Tech Po RWF40 C_Tech pmd 250504A ...
Page 36: ...Page D 1 P Series Commissioning COMMISSIONING ...
Page 42: ...Page D 7 P Series Commissioning ...
Page 44: ...Page D 9 P Series Commissioning AAD PFinal C_Tech Po RWF40 D_Comm pmd 250504A ...
Page 45: ...P Series Page 10 ...
Page 46: ...Page E 1 PO Series Operation And Maintenance E OPERATION AND MAINTENANCE ...
Page 51: ...PO Series Operation And Maintenance Page E 6 ...
Page 52: ...Page E 7 PO Series Operation And Maintenance ...
Page 53: ...PO Series Operation And Maintenance Page E 8 N N N N NOTES OTES OTES OTES OTES ...
Page 54: ...Page E 9 PO Series Operation And Maintenance N N N N NOTES OTES OTES OTES OTES ...
Page 55: ...PO Series Operation And Maintenance Page E 10 N N N N NOTES OTES OTES OTES OTES ...