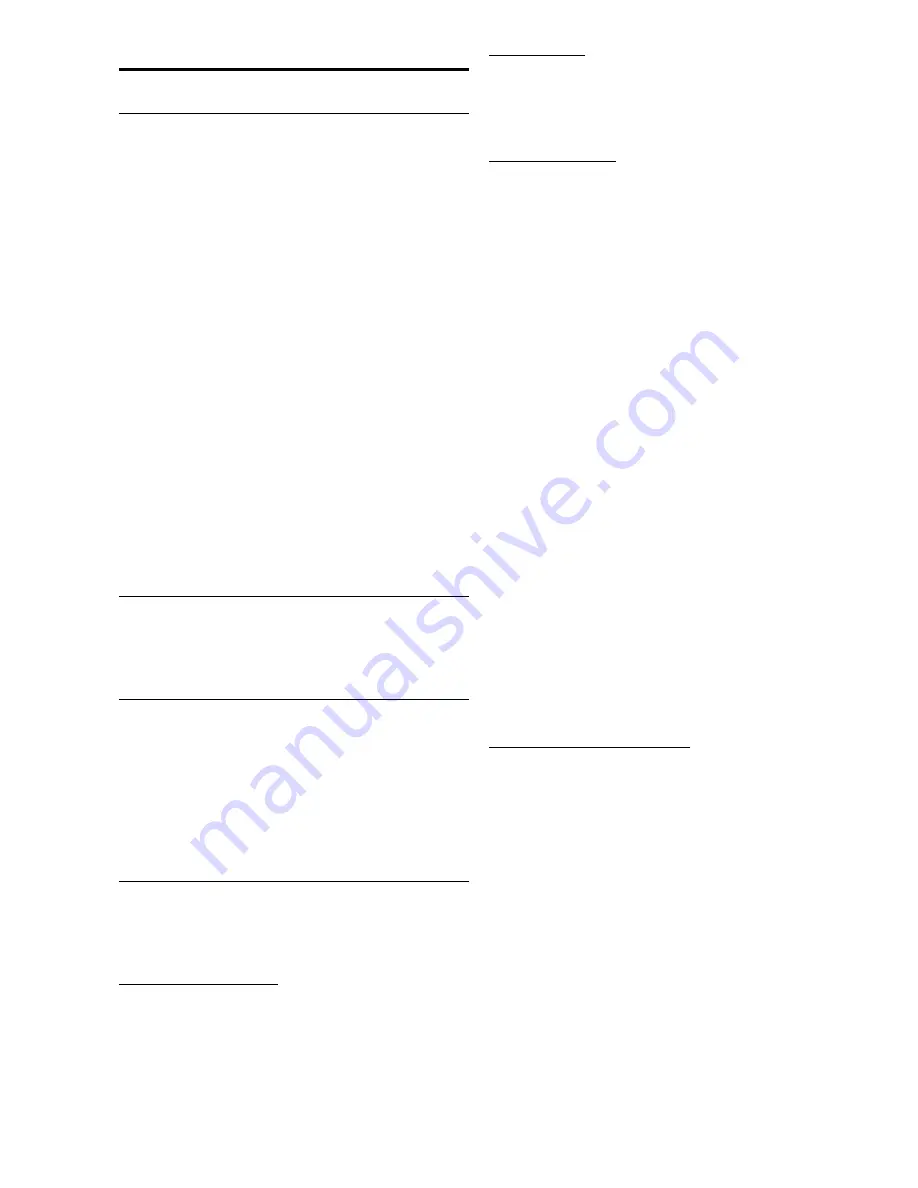
Page B.3
PO Series General Information
SSSSS
ITE
ITE
ITE
ITE
ITE
C
C
C
C
C
ONDITIONS
ONDITIONS
ONDITIONS
ONDITIONS
ONDITIONS
A
A
A
A
A
ND
ND
ND
ND
ND
S
S
S
S
S
ERVICES
ERVICES
ERVICES
ERVICES
ERVICES
Flue and Chimney Requirements
It is important that:
-
the flue pipe from the appliance and the joint
between this flue and the chimney are sealed
to prevent leakage of combustion products
-
the flue pipe from the appliance does not
protrude into the chimney beyond the inside
wall
-
the top of the flue or chimney shall be higher
than any roof within a radius of 10 metres
-
checks are made to ensure that the chimney
is suitable for oil-fired appliances and that
the proposed installation complies with all
Local Authority and other regulations
covering such installations
-
if more than one appliance is connected to a
common flue or chimney, the cross section
of this flue or chimney should be adequate
for the total volume of combustion products
from the appliances
-
it is recommended that each appliance
should be exhausted into a separate flue.
Plant Room Ventilation
An adequate dust-free supply of fresh air is required
for the burner at both high and low levels in
accordance with the appropriate standards.
Existing Appliances
The appliance should be prepared for installation
of a P Series burner by thorough cleaning, including
the removal of all adhering tar, scale and dirt. An
inspection should also be carried out to ensure that
the appliance is in good condition. Any doubt
about the suitability of the appliance should be
referred to the manufacturer.
Oil Supply
In addition to the oil system supplied with the
burner, there are some requirements for the main
oil storage and supply system that supplies oil to
the burner system.
Main Oil Storage Tank
Residual fuel oils must be maintained at all times
at the temperature specified by the fuel supplier.
The Table on Page B.7 shows the temperatures and
pressures for Class D, E, F and G oils.
Oil Deliveries
It is good practice to shut down boilers whilst the
delivery of oil is made and allow 30 minutes for oil
sediment to settle out before re-starting the
burners.
Ring Main System
The oil from the tank must be supplied to the
burner from a pumped ring main system. A typical
system is shown on Page B.8.
The inlet pressure of the oil will depend upon the
type of oil. Oil must be handled and delivered at
the temperatures and pressures shown in the Table
on the Burner Specification Sheet on Page C.2
Technical Specification.
The ring main pumps and pipe size must be
designed to at least 1.25 times the total swept
volume of the burner pump(s) it supplies. Oil supply
pipes must be constructed and installed to comply
with local conditions and appropriate Codes and
Standards. All pipework must be supported firmly,
and in the case of residual oils, lagged, traced and
thermostatically controlled. (The minimum pipe
size is 1.5 inch BSP).
Galvanised steel pipe should not be used.
It shall be of sufficient size to satisfy the pressure
and volume flow requirements of the burner under
all firing conditions.
Checks should be made to ensure that all meters
and other components are appropriately rated for
the maximum flow rate that is anticipated.
The final connection to the oil pump inlet port
should be made using the flexible pipe supplied
with the burner.
Precautions For Residual Oil
If heavy oils are heated to too high a temperature,
then lighter fractions will vaporise and this will
cause premature wear to the pump.
It is essential to filter heavy fuel oil before the
burner inlet. The filtration system should be
selected according to the individual features of the
installation but the diagram on Page B.8 gives some
basic guidelines. The ring main pressure should be
measured at the pump vacuum gauge port to allow
for any pressure drop caused by the filters.
For residual oil burners the pipework should be
insulated, trace heated and thermostatically
controlled.
Summary of Contents for PO160
Page 5: ...Page B 1 PO Series General Information GENERAL INFORMATION ...
Page 14: ...Page B 9 PO Series General Information ...
Page 15: ...PO Series General Information Page B 10 AAD PFinal B_Gen PO B_Gen pmd 250504A ...
Page 16: ...Page C 1 PO Series Technical Specification TECHNICAL SPECIFICATION ...
Page 34: ...Page C 19 PO Series Technical Specification ...
Page 35: ...PO Series Technical Specification Page C 20 AAD PFinal C_Tech Po RWF40 C_Tech pmd 250504A ...
Page 36: ...Page D 1 P Series Commissioning COMMISSIONING ...
Page 42: ...Page D 7 P Series Commissioning ...
Page 44: ...Page D 9 P Series Commissioning AAD PFinal C_Tech Po RWF40 D_Comm pmd 250504A ...
Page 45: ...P Series Page 10 ...
Page 46: ...Page E 1 PO Series Operation And Maintenance E OPERATION AND MAINTENANCE ...
Page 51: ...PO Series Operation And Maintenance Page E 6 ...
Page 52: ...Page E 7 PO Series Operation And Maintenance ...
Page 53: ...PO Series Operation And Maintenance Page E 8 N N N N NOTES OTES OTES OTES OTES ...
Page 54: ...Page E 9 PO Series Operation And Maintenance N N N N NOTES OTES OTES OTES OTES ...
Page 55: ...PO Series Operation And Maintenance Page E 10 N N N N NOTES OTES OTES OTES OTES ...