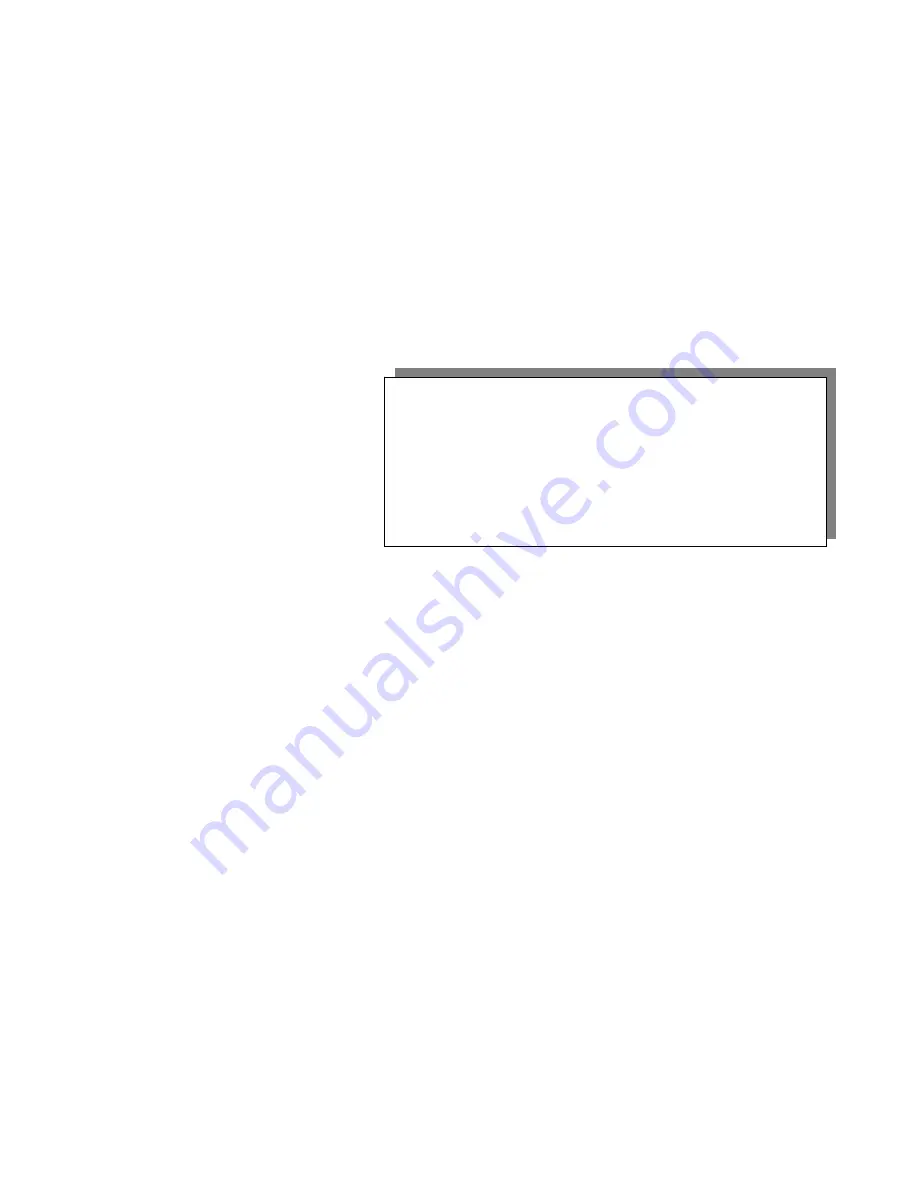
36
IMPORTANT
It is imperative that you explain to the homeowner that it is their
responsibility to:
•
Keep the vent terminal free of snow and ice.
•
Periodically check the vent terminal for debris.
13.0 INSTALLATION CHECKLIST
Installation
a)
Connect all plumbing, and ensure that there are no system leaks, add Fernox F1 Protector (NTI PN: 83448).
b)
Connect, secure, and glue all vent piping.
c)
Install all gas piping as per this manual, and local codes. Pressure test, to detect any gas leaks.
Start-up
1.
Install pressure gauge (Gauge= 0” to 15” w.c. scale) and check line and manifold pressures. (See “Section 5.2”)
2.
Turn gas shut-off valve to the ON position.
3.
Turn Power on to boiler.
4.
Set Sentry Controller to desired settings.
5.
Turn thermostat up, Ignition will occur.
Operational Checklist
Ensure that Carbon Dioxide Readings are within the acceptable ranges. Using an appropriate Oxygen or Carbon Dioxide analyzer, take a
sample of the flue gas. The sample must fall within the acceptable Carbon Dioxide ranges, which is 8% - 9.5% for natural, and 9.0%-
10.5% for propane.
(See “Section 5.2”)
Before Leaving
•
Remove gauge from gas valve and tighten bleed
screw and test plug for leaks.
•
Allow boiler to complete at least one complete
cycle, or at least 15 minutes running time.
•
Always verify proper operation after servicing
14.0 ANNUAL MAINTENANCE AND
INSPECTION
This unit requires very little maintenance, however a
Qualified Technician should inspect it at the beginning of every heating season.
Inspection Check list:
1.)
Lighting is smooth and consistent, and the combustion fan is noise & vibration free.
2.)
The condensate freely flows from the unit, and is cleaned of sediment.
3.)
Relief Valve and air vents are not weeping.
4.)
Low water cut off is flushed (if applicable)
5.)
Examine all venting, for evidence of leaks, and vent screens are cleaned.
6.)
Check the burner plate for signs of leaking.
7.)
Verify the vent clearance as per Section 3.0
8.)
Listen for water flow noises indicating a drop in boiler water flow rate. The boiler and hydronic system my need to be flushed to
eliminate hard water scale (Use Fernox DS-40 Descaler – NTI PN: 83450).
14.1 Combustion Chamber Cleaning
Once every second year
the burner door should be removed so the combustion chamber can be inspected for flue gas blockage. Such
blockage will reduce the boiler’s capacity/firing rate and can impact negatively on how smooth and efficiently the burner lights. Vacuum
out any loose build-up and clean the heat exchanger surface with an appropriate cleaner for combustion chambers. Use nylon or other
non-metallic brush to loosen the sulfate incrustations and any other contaminates. Rinse with water allowing the solution to exit via the
condensate drain. This process may warrant removing the insulation disc from the back of the heat exchanger.
Summary of Contents for Trinity Ti 100
Page 35: ...35 12 0 WIRING SCHEMATIC...