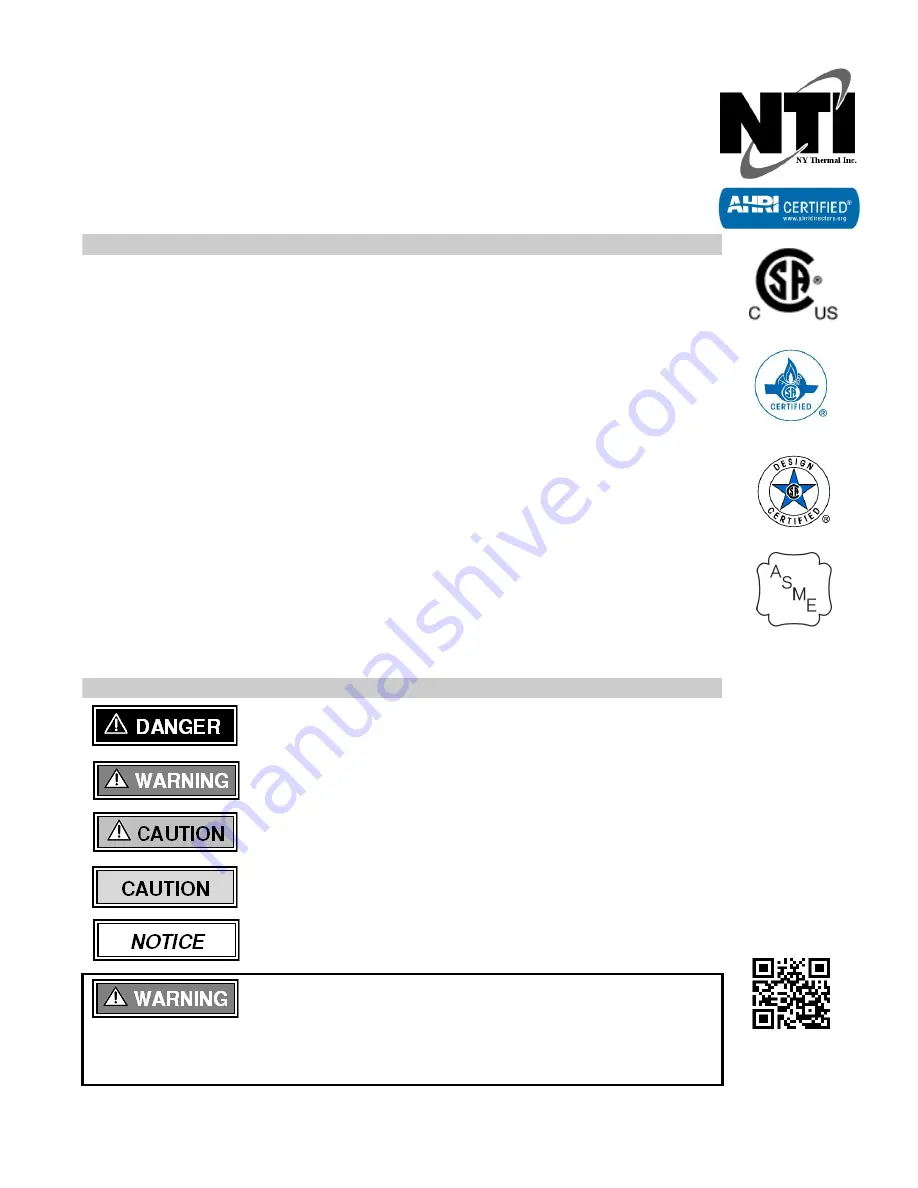
Visit us
online
Trinity Lx - WH
Model Numbers: Lx200WH - Lx800WH
Version Date: 2018-07-11
INSTALLATION AND OPERATION INSTRUCTIONS FOR
TRINITY Lx WATER HEATER
TABLE OF CONTENTS
1.0
INTRODUCTION ................................................................................................................ 3
2.0
SPECIFICATIONS .............................................................................................................. 6
3.0
WATER HEATER LOCATION .......................................................................................... 7
4.0
GENERAL VENTING ....................................................................................................... 12
5.0
VENT AND AIR-INTAKE TERMINATION CLEARANCES ........................................ 27
6.0
CONDENSATE DRAIN .................................................................................................... 30
7.0
INSTALLING GAS PIPING .............................................................................................. 31
8.0
LIGHTING THE WATER HEATER ................................................................................ 33
9.0
GAS VALVE AND BURNER SET-UP ............................................................................ 35
10.0
WATER HEATER PIPING ............................................................................................... 42
11.0
LEAD LAG INSTRUCTIONS ........................................................................................... 51
12.0
FIELD WIRING ................................................................................................................. 54
13.0
WIRING SCHEMATICS ................................................................................................... 60
14.0
INSTALLATION CHECKLIST ........................................................................................ 64
15.0
ANNUAL MAINTENANCE AND INSPECTION ........................................................... 65
16.0
PARTS LIST ...................................................................................................................... 67
17.0
TROUBLESHOOTING ..................................................................................................... 79
HAZARD SYMBOLS AND DEFINITIONS
Danger Sign: Indicates a hazardous situation which, if not avoided, will
result in serious injury or death.
Warning Sign: Indicates a hazardous situation which, if not avoided,
could result in serious injury or death.
Caution Sign plus Safety Alert Symbol: Indicates a hazardous situation
which, if not avoided, could result in minor or moderate injury.
Caution Sign without Safety Alert Symbol: Indicates a hazardous
situation which, if not avoided, could result in property damage.
Notice Sign: Indicates a hazardous situation which, if not avoided,
could result in property damage.
This Water Heater must be installed by a licensed and trained Heating
Technician or the
Warranty is Void.
Failure to properly install this
unit may result in property damage, serious injury to occupants, or
possibly death.
NTI # 85236
H