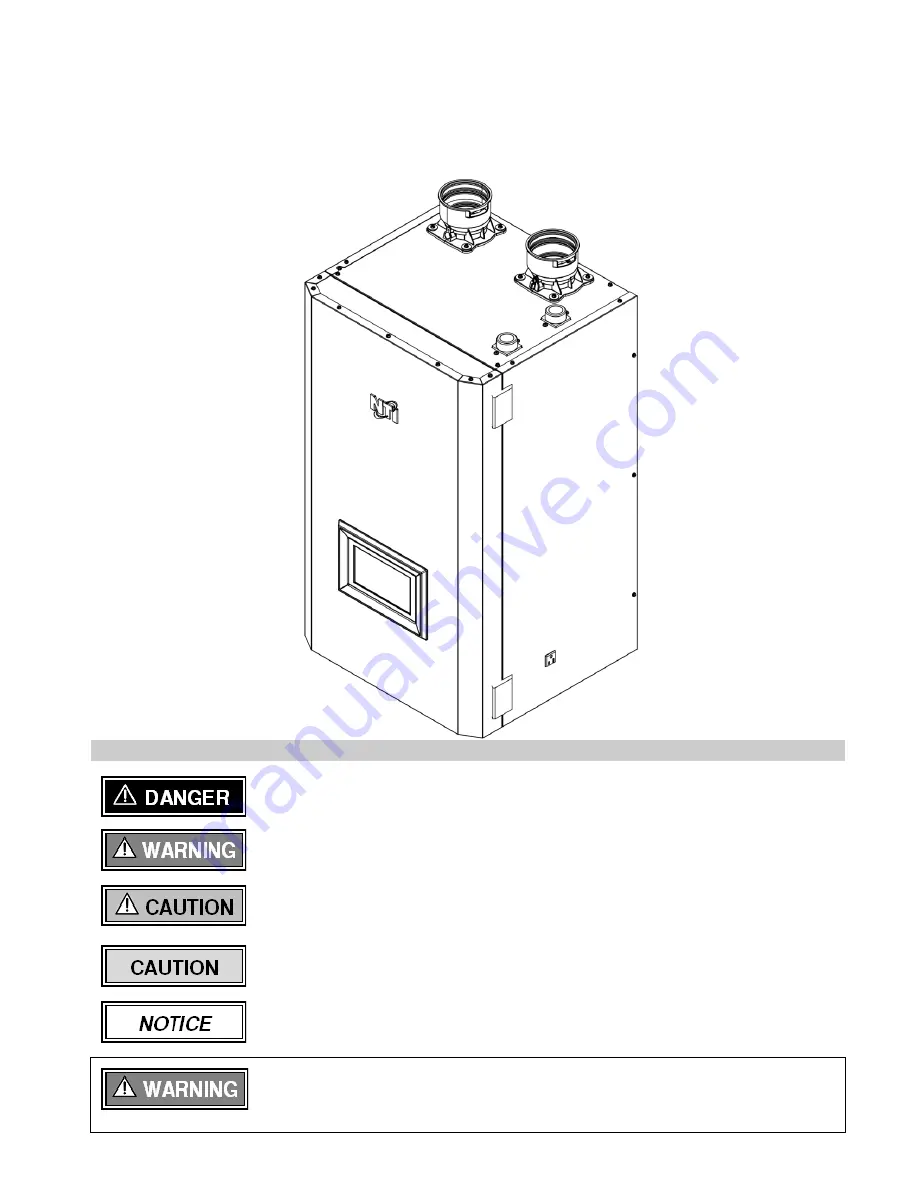
TFTN 085-399
INSTALLATION AND OPERATION MANUAL
Version Date: 2022-09-06
HAZARD SYMBOLS AND DEFINITIONS
Danger Sign: Indicates a hazardous situation which, if not avoided, will result in serious
injury or death.
Warning Sign: Indicates a hazardous situation which, if not avoided, could result in
serious injury or death.
Caution Sign plus Safety Alert Symbol: Indicates a hazardous situation which, if not
avoided, could result in minor or moderate injury.
Caution Sign without Safety Alert Symbol: Indicates a hazardous situation which, if not
avoided, could result in property damage.
Notice Sign: Indicates a hazardous situation which, if not avoided, could result in property
damage.
This Boiler must be installed by a licensed and trained Heating Technician, or the
Warranty is Void.
Failure to properly install this unit may result in property damage,
serious injury to occupants, or possibly death.
NTI # 87137