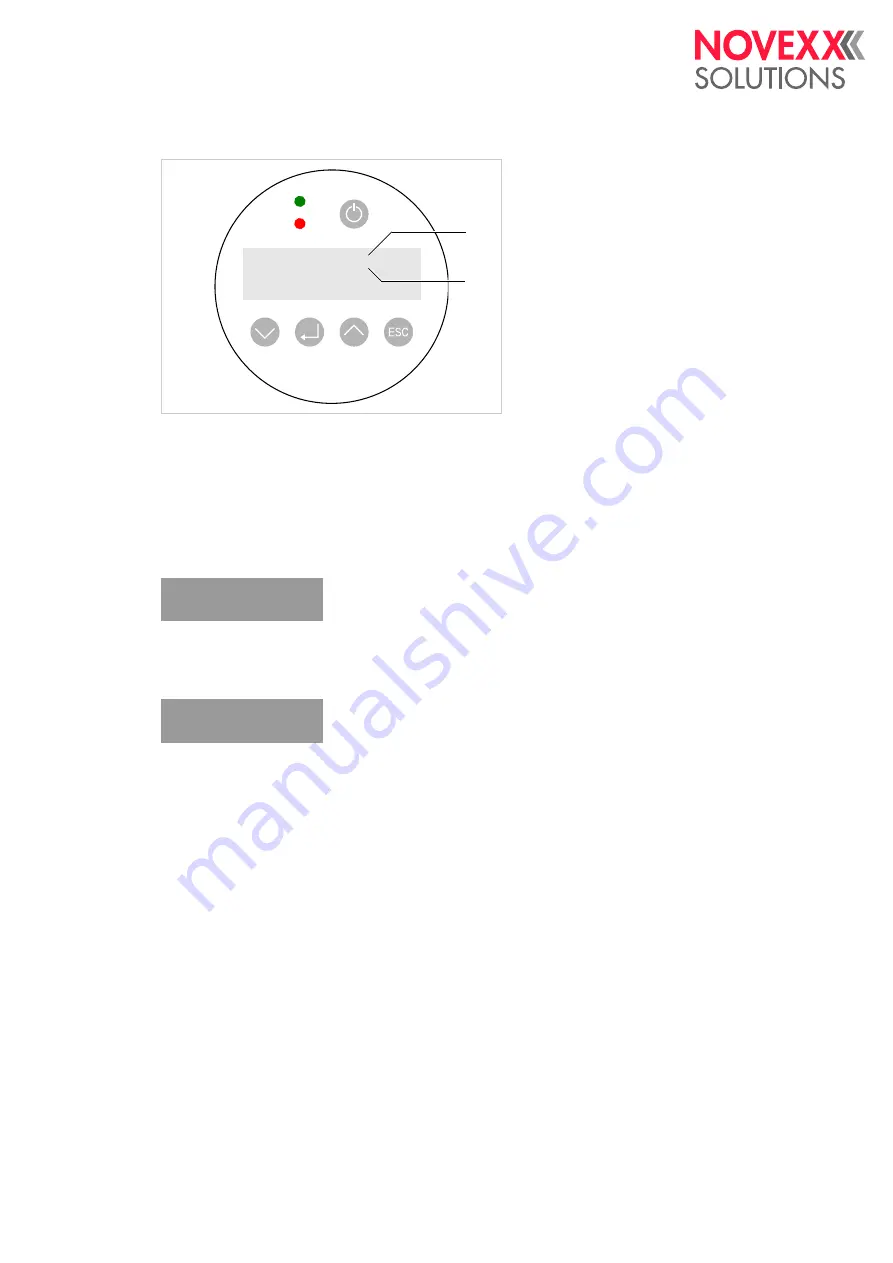
User Manual
ALX 92x
09/2016 | 00
38
Online mode
[28] Control panel of the ALX 92x in online mode.
A
Interpreter activity
B
Data transfer
Activate online mode
Activate from offline mode:
Press the ONLINE key.
Screen:
(There are no pending print jobs for processing).
Data transfer and interpreter activity
Screen showing
data transfer
:
A
data transfer
to the printer that is currently in progress is indicated in the display by a dot on the
right below the number of jobs loaded [28B].
Screen showing
interpreter activity
:
An additional dot above the first one at the vertical midpoint of the line [28A] indicates activity of the
interpreter:
•
No dot
: No data to interpret.
•
Dot
: The interpreter is working (data still present in the spooler)
•
Flashing dot
: The interpreter is waiting for additional data to be able to complete the command
(no data in the spooler).
ONLINE 0 JOBS
ONLINE 0: JOBS
PROG
FEED
ONLINE
APPLY
ON
ERROR
ONLINE 0: JOBS
A
B
Summary of Contents for ALX 924
Page 2: ......
Page 6: ...User Manual ALX 92x 09 2016 6 Content...
Page 90: ......
Page 91: ...Novexx Solutions GmbH Ohmstra e 3 85386 Eching Germany 49 8165 925 0 www novexx com...