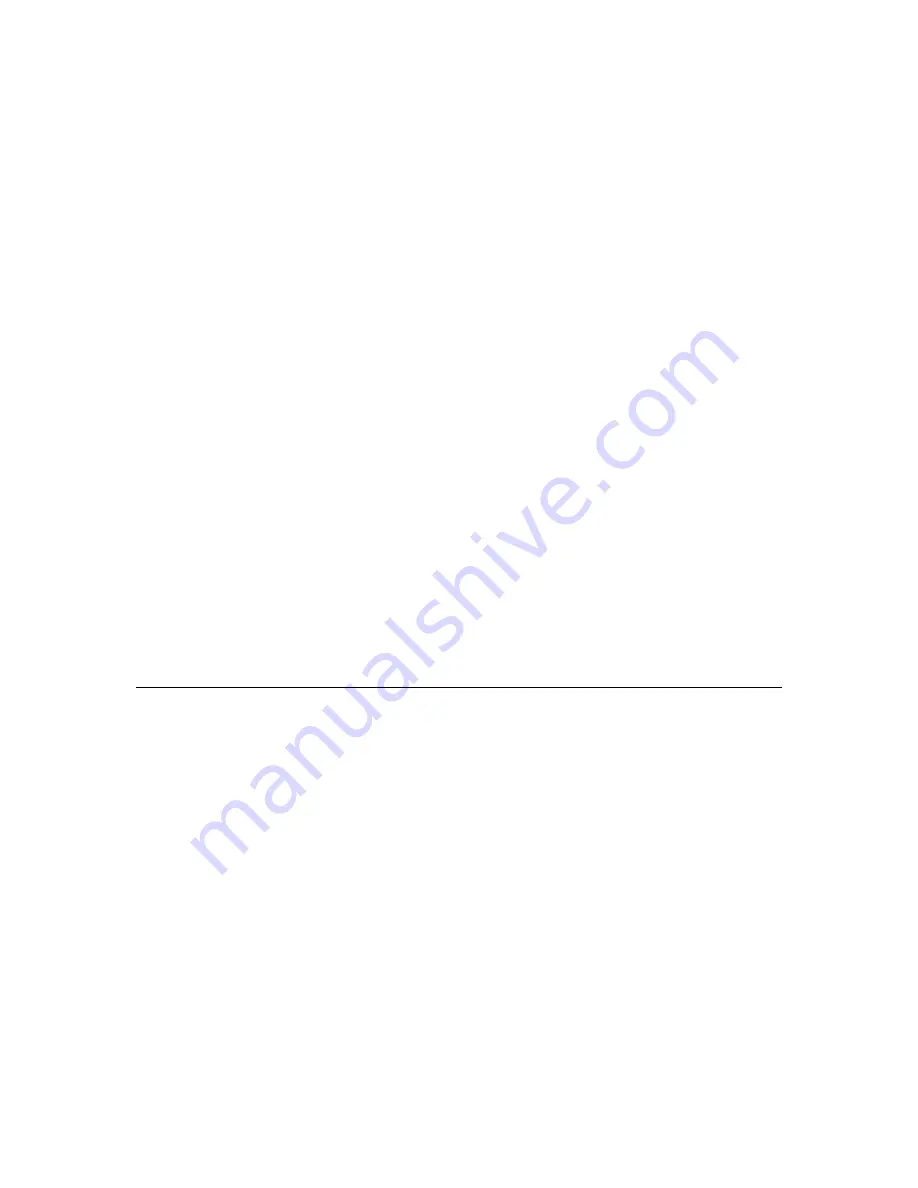
appeared, read on.
The drum itself is made of case-hardened steel, and with many more splines than the centre so there is
no tendency for the plain steel plates to notch into the drum The innermost friction surface on early
clutches was a separate steel plate located by two tiny little roll-pins in blind holes in the back of the drum.
Once the clutch was together this was O.K, but if the pins came loose (as they did) it was almost
impossible to put the thing together and locate the backplate properly. It was also impossible because of
the hardness to drill through the roll-pin holes so that proper rivets could be fitted-unless you had access
to fancy equipment for spark erosion, but it is possible to tack-weld the back plate in position if you grind a
couple of notches in the edge of the plate so you can get in with arc-welding equipment without spoiling
the splines. Later the drums avoid the problem by having the back plate held in with three rivets to start
with. John Hudson has advised that there is no need to re-rivet or weld this plate in, just remove the
remains of the pins and let the plate do its own thing, quite safe.
The main problem with the later solid friction plates was the reduction in friction when they eventually
became oil soaked and glazed-so the clutch slipped at maximum torque. This could be relieved by
grooving the plate surface radially-six grooves each side, with the corner of a square file (or the edge of a
grinding wheel if you are in a hurry-but DON'T breathe the resulting dust). Wash the plates in petrol and
be prepared to do it again at 10.000 mile intervals. I have never seen a worn out Commando clutch-even
with slip you have enough drive to get home. Those of you with scientific inclinations can look again at
'the diaphragm spring diagram to appreciate that a bit of wear on the plates actually increases the
clamping load slightly --whereas with coil springs the load drops quickly as the plates wear, aggravating
any tendency to slip.
The 828cc models (and the very last 745cc models) have bronze plates so that they can be thinner and
get more in, increasing the torque capacity. Even so, they tend to form a sticky slippery surface in time
and need to be washed off occasionally.
One queer thing which does happen is this. If the alternator starts to come loose the clutch will tend to slip
at the same time. I suspect that this is because of the extra snatching-vibration caused by the •loose
rotor, which lowers the effective friction. Just as a brick won't slide down a plank but will start to slide if
you drum on the end of the plank with a hammer. Anyone got any other theory?
CARBURETTORS: continued from page 21
all the oil off the bore, mixing with the oil, and getting down the exhaust pipe ready to split the silencer
when a spark gets in from the other cylinder. Both these things should be done if the head gasket blows-
and if possible it helps to jack the exhaust valve open slightly to relieve the compression--do this by over
tightening the rocker adjuster on that cylinder-but not by more than a turn or so or the valve may hit the
piston. Ah, happy days. . . . If you have twin cables all the way and twin pull throttle, to be recommended
as cable life is considerably lengthened. then to run on one cylinder just remove the cable outer end stop
on the offensive side. For Boyer/Rita a owners removing a coil lead isn't advisable so a spare plug wired
/taped to earth with plug cap fitted to let spark go in fret air is recommended. No need to remove the
original plug, as it doesn't food the engine and stops the ingress of dirt/grit on the suck stroke.
20
Summary of Contents for 850 Mk 1 1974
Page 46: ...Keep polishing 44...