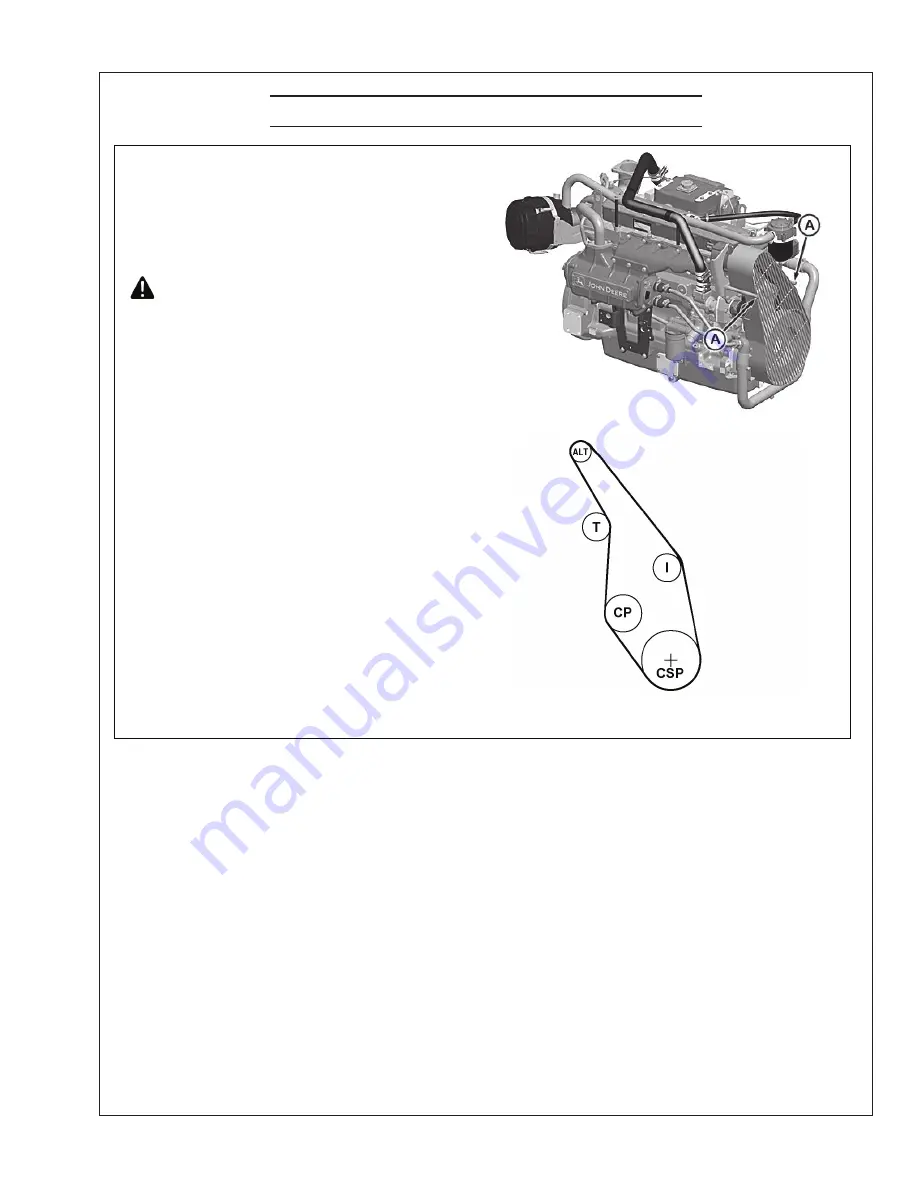
OM3-80 12/21
Service As Required (Continued)
55
RG19661,00003F4 -19-20FEB13-1/1
Replacing Alternator Belt (With Automatic
Tensioner)
Refer to CHECKING BELT TENSIONER SPRING
TENSION AND BELT WEAR in Lubrication and
Maintenance/500 Hour/12 Month Section for additional
information on the belt tensioner.
CAUTION: Belt guard should be in place at all
times when engine is running.
NOTE: While belt is removed, inspect pulleys and
bearings. Rotate and feel for hard turning or
any unusual sounds. If pulleys or bearings need
replacement, see your John Deere dealer.
1. Remove cap screws (A) and carefully remove belt
guard from engine.
2. Release tension on belt using a breaker bar and socket
on tension arm and remove poly-vee belt from pulleys.
3. Inspect belts for cracks, fraying, or stretched out
areas. Replace if necessary.
4. Install new belt, making sure belt is correctly seated in
all pulley grooves. Refer to belt routing at right.
5. Apply tension to belt with tensioner. Remove socket.
6. Start engine and check belt alignment.
A—Cap Screws
ALT— Alternator
CSP—Crankshaft Pulley
I— Idler Pulley
T—Tensioner
CP—Coolant Pump
RG2216
2—
UN—06DEC12
Remove Belt Guard
RG1207
7—
UN—26FEB0
2
Belt Routing