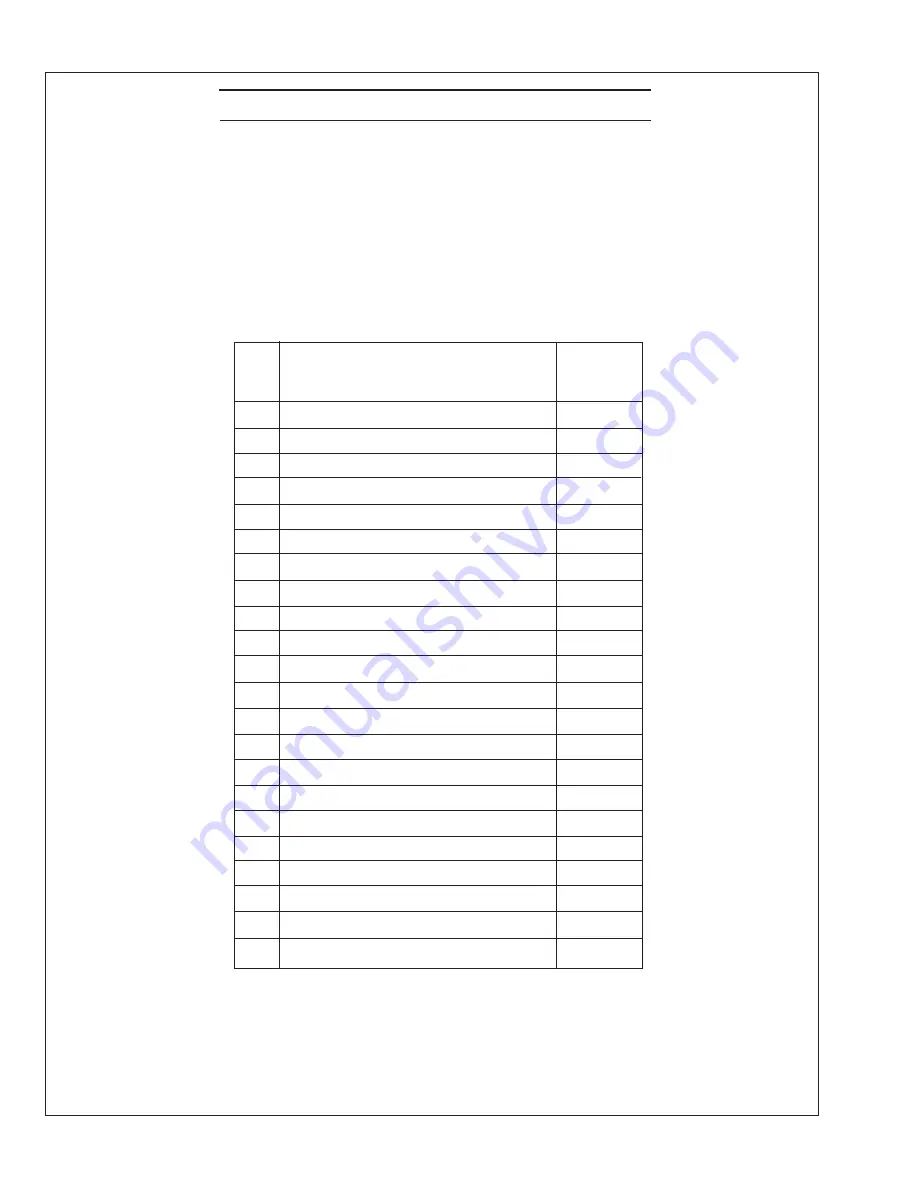
OM2-2 1/17
54
Item Description
Quantity
1
Lube Oil Filter
4
2
Air Filter Element
1
3
Fuel Filter
2
4
Fuel Filter Element
4
5
Fuel Lift Pump
1
6
Injector
1
7
Thermostat
2
8
Thermostat Seal Ring
2
9
Thermostat Cover Gasket
1
10
Rocker Cover Gasket
2
11
Engine Overhaul Gasket Kit
1
12
Zinc Anode*
6
13
Raw Water Pump Impeller*
2
14
Raw Water Pump Cover Gasket*
2
15
Raw Water Pump*
1
16
Raw Water Pump Bearing*
2
17
Coolant Pump Repair Kit
1
18
Coolant Pump Gasket
1
19
Drive Belt
1
20
Workshop Manual
1
*Heat exchanger cooled engines only
Safety at sea depends on careful preparation, product knowledge, and having the right
tools and parts. Below is a list of parts Northern Lights, Inc. recommends you carry
onboard at all times.
Onboard Parts Kits are available from your dealer.
We consider these minimum quantities. Your vessel's operating conditions may require
more of a given part. Consult your dealer. The example below lists typical items for
either heat exchanged or keel cooled engines.
On Board Spare Parts
52
Summary of Contents for M1064A
Page 11: ...OM2 2 1 17 9 Notes...
Page 48: ...OM2 2 1 17 46 Notes Added 4 10 12...
Page 49: ...OM2 2 01 17 47 D C Wiring 12 Volt Standard Ground for M1066A2 and M1066A3 Drawing D 3769B...
Page 50: ...OM2 2 01 17 48 D C Wiring 24 Volt Isolated Ground for M1066A2 and M1066A3 Drawing D 3772C...
Page 55: ......
Page 56: ......