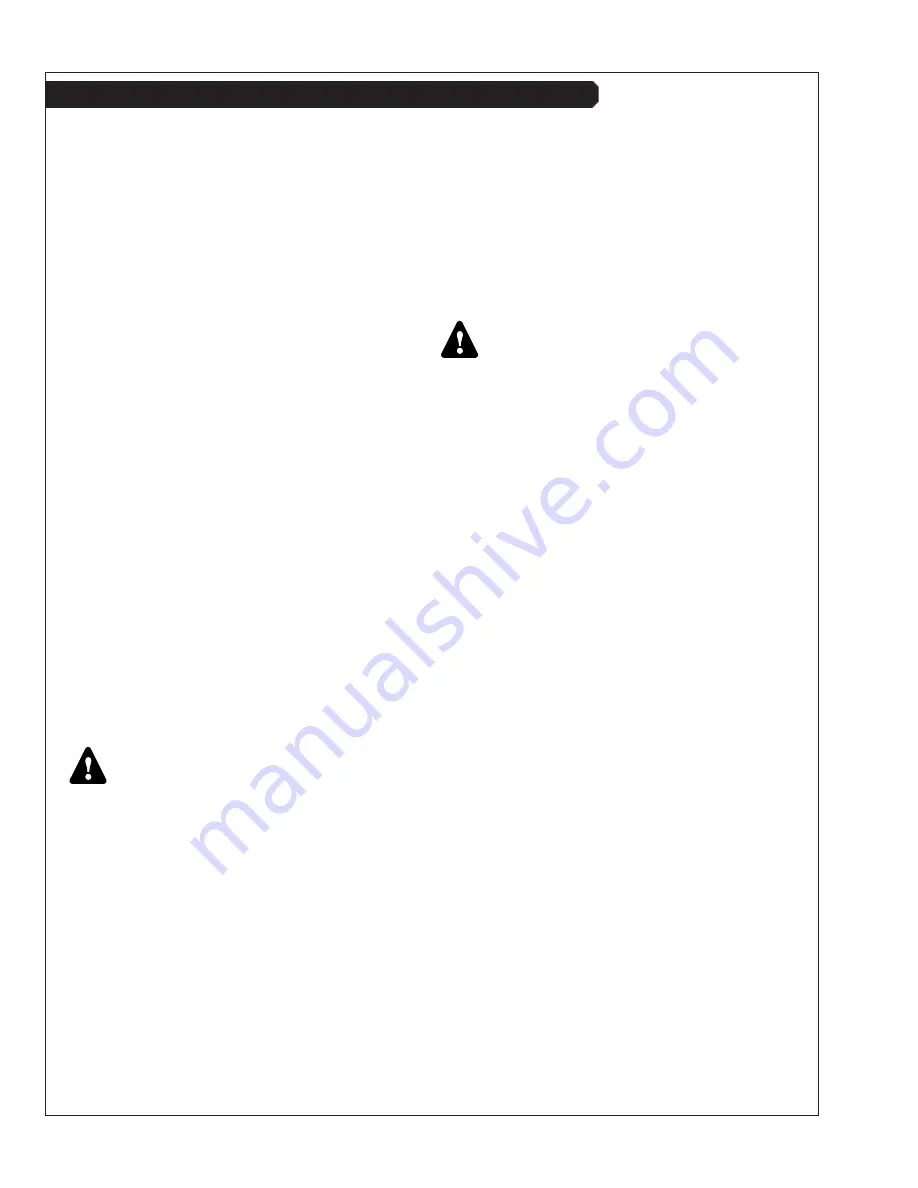
O6108 08/01
SCA'S CONTINUED
If additional SCA's are needed, prepare a mix-
ture of 50% quality water and 50%EGC (anti-
freeze). Add liquid SCA at a rate of 3%, by
volume.
Example:
30 mL of SCA per liter of H
2
O/EGC
mixture.
(1.0
fl oz of SCA per qt of H
2
O/EGC).
Add the resulting mixture to the cooling system
in quart increments. Run the engine for 2 hours
and retest the coolant. Continue process until
SCA concentration meets recommended levels.
5. SCA is available from your Northern Lights/
Lugger dealer in the following sizes.
Pint - Part Number...............20-00002
1/2 gallon - Part Number.....20-00003
6. DO NOT use any coolant system additives con-
taining soluble oil
.
COOLANT TESTING
1. Coolant test kits are available to allow on-site
evaluation of the coolant condition.
2. The kits use small strips of paper which are
dipped into the coolant. The paper changes color
and indicates the SCA concentration. It also
indicates the amount of EGC (antifreeze).
3. Test kits are available through your Northern
Lights or Lugger Dealer.
4 Pack - Part Number.......................20-00005
50 Pack - Part Number.....................20-00010
SP14. CHECKING COOLANT LEVEL
.
CAUTION: The cooling water in the engine
reaches extremely high temperatures. You
must use extreme caution when working on
hot engines to avoid burns. Allow the engine
to cool before working on the cooling system.
Open the fi ller cap carefully, using protective
clothing when the engine is warm.
1. Check the coolant level each day before starting
the engine. Check the coolant level by remov-
ing the pressure cap from the expansion tank.
In order to give the coolant an opportunity to
expand, the level should be about 1 3/4 in. (4-5
cm) below the fi ller cap sealing surface when
the engine is cold. When fi lling with coolant, the
venting cock on top of the turbocharger should
be opened to ensure that no air pockets form in
the cooling system.
2. The pressure valve in the fi ller cap releases when
the pressure is approximately 7 PSI (0.5 bar).
Use a cap pressure tester to check cap if you
suspect it is faulty.
4. The makeup coolant, added to compensate for
loss or leaks, must meet engine coolant require-
ments outlined in previous section.
SP15. FLUSHING THE COOLING SYSTEM
CAUTION: The cooling water in the engine
reaches extremely high temperatures. You
must use extreme caution when working on
hot engines to avoid burns. Allow the engine
to cool before working on the cooling system.
Open the fi ller cap carefully, using protective
clothing when the engine is warm.
IMPORTANT
Be sure to close the sea cock before working on the
engine cooling system.
1. Flush the cooling system and check for leaks and
blockage every 600 hours, or yearly.
2. The engine must be stopped and cold. Close the
sea cock. Remove the fi ller cap with caution.
Open cooling system air vent on top of turbo-
charger.
3. Drain the jacket (fresh) water circuit of the cool-
ing system.
4. To drain the raw water circuit of HE engines,
open the drain at the bottom of the heat
exchanger. (See Fig. 1,22).
5. With drains open, pour clean water into the
expansion tank. When the water from each
drain is clear and free from discoloration and
sediment, close that drain. When all drains are
closed, fl ushing is complete.
6. Re-drain the engine and refi ll the jacket (fresh)
water circuit with coolant mixture as described
in previous section.
7. Close cooling system air vent.
8. Open sea cock.
9. Start engine. Monitor temperature gauge care-
fully and check cooling system for leaks.
22
Servicing
Summary of Contents for LUGGER L6108
Page 9: ...O6108 08 01 7 Notes...
Page 35: ...O6108 08 01 33 Wiring Diagrams DC Wiring Schematic Standard Ground NL 24V C 4417...
Page 36: ...O6108 08 01 34 Wiring Diagrams DC Wiring Schematic Standard Ground Marine 24V C 4419...
Page 37: ...O6108 08 01 35 Wiring Diagrams DC Wiring Schematic Isolated Ground Marine 24V C 4421...
Page 38: ...O6108 08 01 36 DC Wiring Schematic Standard Ground Marine 12V C 4430 Wiring Diagrams...
Page 39: ...O6108 08 01 37 Wiring Diagrams DC Wiring Schematic Isolated Ground Marine 12V C 4448...