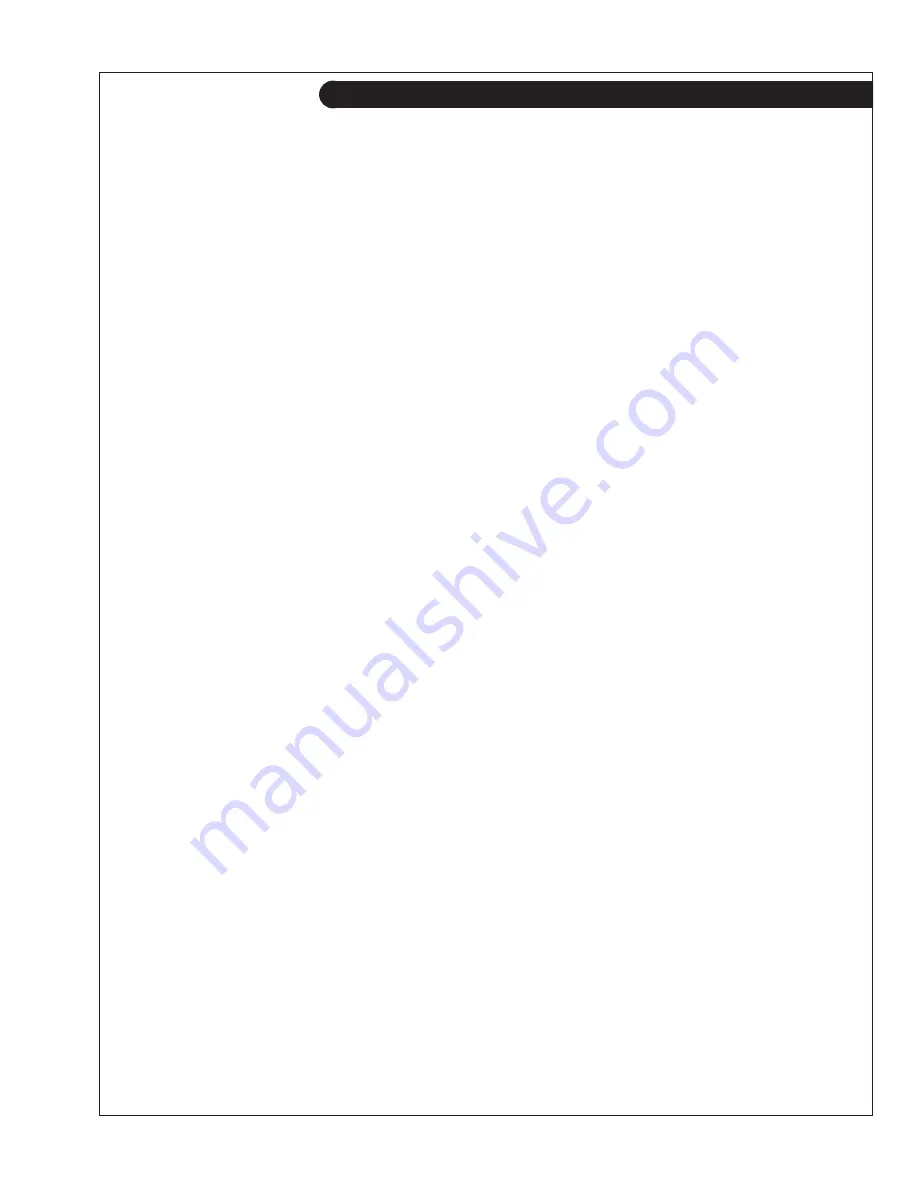
O6108 08/01
b. Reinstall bracket between the engine block
and rear of pump. Leave pump mounting nut
(see Fig. 12,8) loose until pump is timed.
c. Reinstall feed lines (see Fig. 12,7) and
torque banjo bolts to 18.0 ft. lbs. (2.5 kg).
Reinstall lubrication oil line (see Fig. 12,1)
and torque banjo bolt to 9.0 ft. lbs. (1.25 kg)
Install new sealing washers on both sides of
banjo bolts.
d. Reinstall fuel injection lines (see Fig. 12,2)
and line clamp (Fig. 12,1). Torque fuel line
sleeve nuts at injection pump to 18-25 ft. lbs.
(2.5-3.5 kg). Torque fuel line sleeve nuts at
the injectors to 14.5-18 ft. lbs. (2.0-2.5 kg).
TIMING INJECTION PUMP
1. The Match Mark Alignment Method:
Note: This is used when the injection pump is
being reinstalled on the original engine and the
pump has NOT been repaired.
a. When the stamped line on the injection
pump is aligned with the stamped line on the
drive case, the pump is correctly timed (see
Fig. 14).
2. Delivery Valve Method:
Use delivery valve method when a repaired or
replaced injection pump is being installed.
a. Disconnect fuel injection line from the No.
1 cylinder delivery valve on the injection
pump (12,4).
b. Remove delivery valve holder. Remove
spring and delivery valve and put valve
holder back in injection pump.
c. Place the throttle (12,9) in the full fuel (for-
ward) position.
d. Use a breaker bar with the appropriate
socket to rotate the crankshaft in a clockwise
direction while operating the priming pump
(12,6). This is best done by two people.
e. Stop rotating and pumping when fuel stops
fl owing out of the delivery valve holder
(12,4).
17
SP11. INJECTION PUMP
1. The pump settings, maximum speed, idle speed
and exhaust smoke should be checked after
every 2400 hours of operation. Service of the
fuel injection pump should only be done if
checks indicate pump malfunction.
2. Low power and no smoke can indicate a fuel
injection pump malfunction. Check for full
throttle, proper solenoid adjustment and air fi lter
cleanliness before replacing pump. Black smoke
occasionally may indicate an injection pump
problem.
3. Any repair which involves disassembly of the
injection pump must be carried out by trained
mechanics with the proper tools and test devices.
NOTE: All warranties on the engine become null
and void if the injection pump seals are broken
by unauthorized persons.
4. Injection Pump Removal:
a. Clean injection pump, hoses and area around
the pump with cleaning solvent or a steam
cleaner.
NOTE: Never steam clean or pour cold water
on an injection pump while the engine is
running or the pump is warm.
b. Remove line clamps (see Fig. 12,3) & fuel
injection lines (Fig. 12,2).
c. Remove feed lines (see Fig. 12,7), lubri-
cation tube (Fig. 12,1) and return line
(Fig. 12,5).
d. Remove pump mounting nut (see Fig. 12,8)
and mounting bracket at rear of pump.
e. Remove four nuts (see Fig. 12,10) between
the drive case and the fl ange on the pump
drive. It will be necessary to use a socket
wrench, a universal joint and an extension to
loosen the two bolts on the back side of the
pump.
f. Remove pump from drive case.
6. Injection Pump Installation:
a. Line up pump to drive case. The spline lacks
a tooth, so match male and female to this
position. Reinstall the four nuts (see Fig.
12,10) holding the pump to the drive case
but do not tighten until pump is timed. (See
Injection Pump Timing, Pg. 18.)
Servicing
Summary of Contents for LUGGER L6108
Page 9: ...O6108 08 01 7 Notes...
Page 35: ...O6108 08 01 33 Wiring Diagrams DC Wiring Schematic Standard Ground NL 24V C 4417...
Page 36: ...O6108 08 01 34 Wiring Diagrams DC Wiring Schematic Standard Ground Marine 24V C 4419...
Page 37: ...O6108 08 01 35 Wiring Diagrams DC Wiring Schematic Isolated Ground Marine 24V C 4421...
Page 38: ...O6108 08 01 36 DC Wiring Schematic Standard Ground Marine 12V C 4430 Wiring Diagrams...
Page 39: ...O6108 08 01 37 Wiring Diagrams DC Wiring Schematic Isolated Ground Marine 12V C 4448...