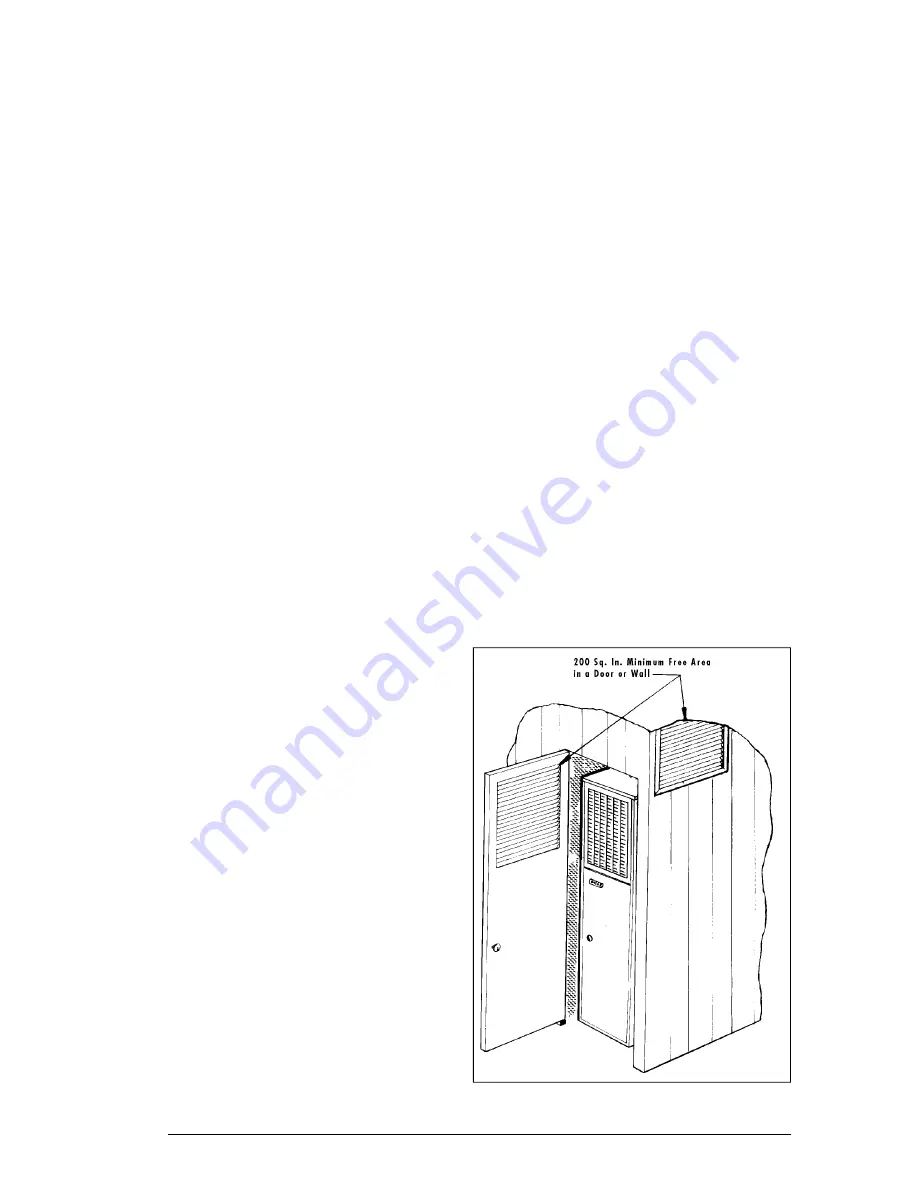
8
Using the provided hose clamp, secure the
flexible combustion air tubing from the burner to
the combustion air adapter.
CB-200A Cottage Base Installation
The CMF can be installed on a CB-200A cottage
base in certain applications, as described earlier
in these instructions (See Table 1). Refer to the
Replacement Parts List for information on
ordering this base. For installation, refer to the
instructions that are provided with the CB-200A
base kit.
Closet Installation of the Furnace
Return air systems for a closet installation of the
furnace may consist of a grille or grilles in a
closet door or side wall that
communicates with the living area of the home.
(See Figure 6) Return air openings should not
be located to draw air directly from a bathroom.
Grilles placed in a side wall require a 6" clear-
ance from the wall to the furnace so that the air
may enter the front grille of the furnace. In
addition, all return air systems, including the
floor and ceiling systems, must meet the follow-
ing conditions:
A. The return-air opening into the closet,
regardless of its location, is to be a mini-
mum of 200 square inches.
B. If the return-air opening is located in the
floor of the closet (versus the vertical front
or side wall), the opening is to be provided
with means to prevent its inadvertent clo-
sure by a flat object placed over the open-
ing.
C. The cross-sectional area of the return
duct system (when located in the floor or
ceiling of the manufactured home) leading
into the closet is to be not less than 200
square inches.
D. The total free area of the openings in the
floor or the ceiling registers serving the
return air duct system is to be not less than
300 square inches. At least one such
register is to be located where the likeli-
hood of its being covered by carpeting,
boxes, and other objects is minimized.
E. Materials located in the return duct system
shall have a flame spread classification of
200 or less.
F. Noncombustible pans having one inch
upturned flanges are located beneath
openings in a floor return duct system.
G. Hollow spaces used as ducts or plenums
for environmental air may contain mineral-
insulated metal sheathed cable, aluminum
sheathed cable, electrical metallic tubing,
rigid metal conduit, flexible metal conduit
not to exceed four (4) feet, or metal-clad
cables. Wiring materials, fixtures, are to
be suitable for the expected ambient
temperatures to which they will be sub-
jected.
H. Gas piping cannot be located in the return
duct system.
I. The negative pressure in the closet must
not be less than minus 0.05 inches water
column with the closet door closed and the
fan operating at high speed. A reading
below minus 0.05" indicates a dirty filter or
a restricted return air system.
Figure 6. Closet Installation
Summary of Contents for CMF 100-PG
Page 27: ......