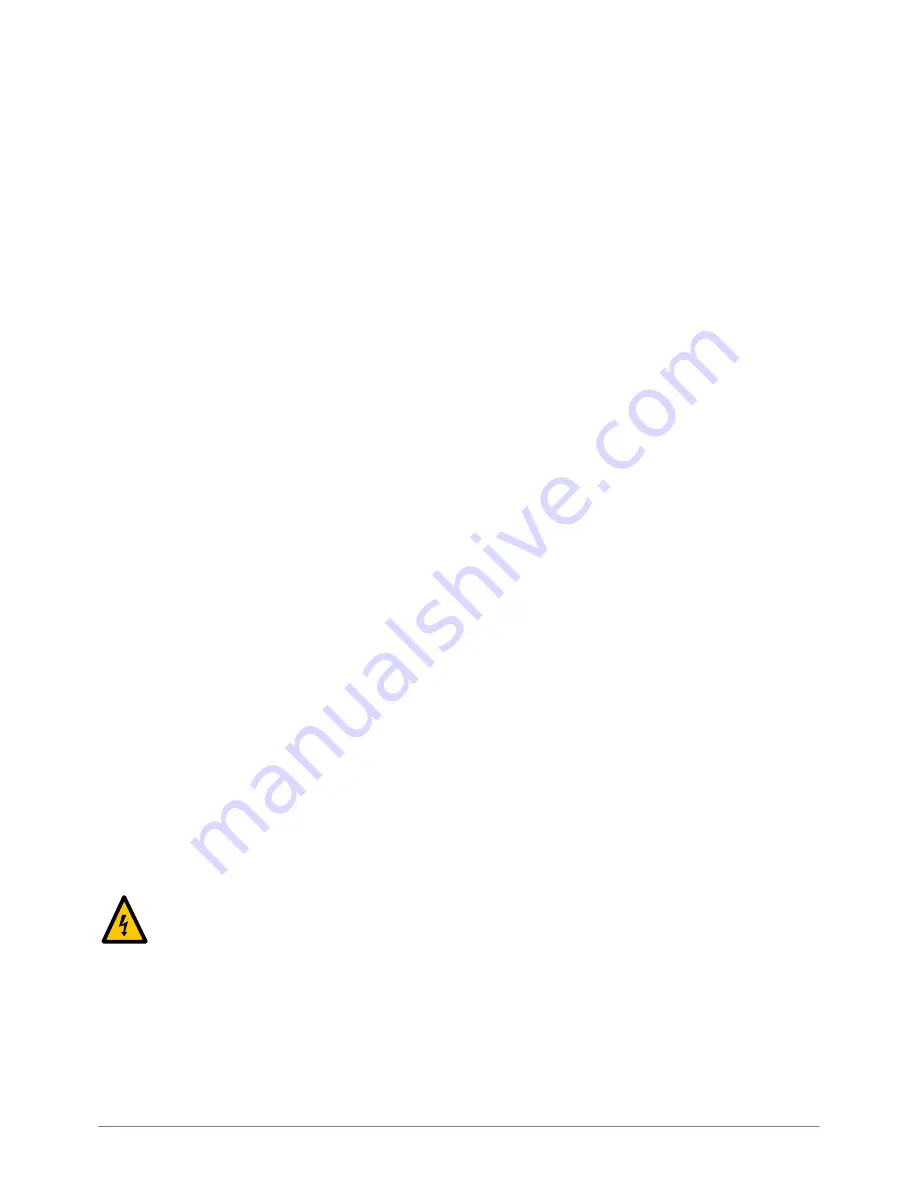
Prodigy
r
Robot Gun
2
Part 1105518
−
02
E
2014
Nordson Corporation
S
Obtain and read Material Safety Data Sheets
(MSDS) for all materials used. Follow the
manufacturer’s instructions for safe handling
and use of materials, and use recommended
personal protection devices.
S
To prevent injury, be aware of less-obvious
dangers in the workplace that often cannot be
completely eliminated, such as hot surfaces,
sharp edges, energized electrical circuits, and
moving parts that cannot be enclosed or
otherwise guarded for practical reasons.
Fire Safety
To avoid a fire or explosion, follow these
instructions.
S
Do not smoke, weld, grind, or use open flames
where flammable materials are being used or
stored.
S
Provide adequate ventilation to prevent
dangerous concentrations of volatile materials
or vapors. Refer to local codes or your material
MSDS for guidance.
S
Do not disconnect live electrical circuits while
working with flammable materials. Shut off
power at a disconnect switch first to prevent
sparking.
S
Know where emergency stop buttons, shutoff
valves, and fire extinguishers are located. If a
fire starts in a spray booth, immediately shut off
the spray system and exhaust fans.
S
Clean, maintain, test, and repair equipment
according to the instructions in your equipment
documentation.
S
Use only replacement parts that are designed
for use with original equipment. Contact your
Nordson representative for parts information
and advice.
Grounding
WARNING:
Operating faulty
electrostatic equipment is hazardous and
can cause electrocution, fire, or
explosion. Make resistance checks part
of your periodic maintenance program. If
you receive even a slight electrical shock
or notice static sparking or arcing, shut
down all electrical or electrostatic
equipment immediately. Do not restart
the equipment until the problem has
been identified and corrected.
Grounding inside and around the booth openings
must comply with NFPA requirements for Class 2,
Division 1 or 2 Hazardous Locations. Refer to
NFPA 33, NFPA 70 (NEC articles 500, 502, and
516), and NFPA 77, latest conditions.
S
All electrically conductive objects in the spray
areas shall be electrically connected to ground
with a resistance of not more than 1 megohm
as measured with an instrument that applies at
least 500 volts to the circuit being evaluated.
S
Equipment to be grounded includes, but is not
limited to, the floor of the spray area, operator
platforms, hoppers, photoeye supports, and
blow-off nozzles. Personnel working in the
spray area must be grounded.
S
There is a possible ignition potential from the
charged human body. Personnel standing on a
painted surface, such as an operator platform,
or wearing non-conductive shoes, are not
grounded. Personnel must wear shoes with
conductive soles or use a ground strap to
maintain a connection to ground when working
with or around electrostatic equipment.
S
Operators must maintain skin-to-handle contact
between their hand and the gun handle to
prevent shocks while operating manual
electrostatic spray guns. If gloves must be
worn, cut away the palm or fingers, wear
electrically conductive gloves, or wear a
grounding strap connected to the gun handle or
other true earth ground.
S
Shut off electrostatic power supplies and
ground gun electrodes before making
adjustments or cleaning powder spray guns.
S
Connect all disconnected equipment, ground
cables, and wires after servicing equipment.
Action in the Event of a Malfunction
If a system or any equipment in a system
malfunctions, shut off the system immediately and
perform the following steps:
S
Disconnect and lock out electrical power. Close
pneumatic shutoff valves and relieve pressures.
S
Identify the reason for the malfunction and
correct it before restarting the equipment.
Disposal
Dispose of equipment and materials used in
operation and servicing according to local codes.