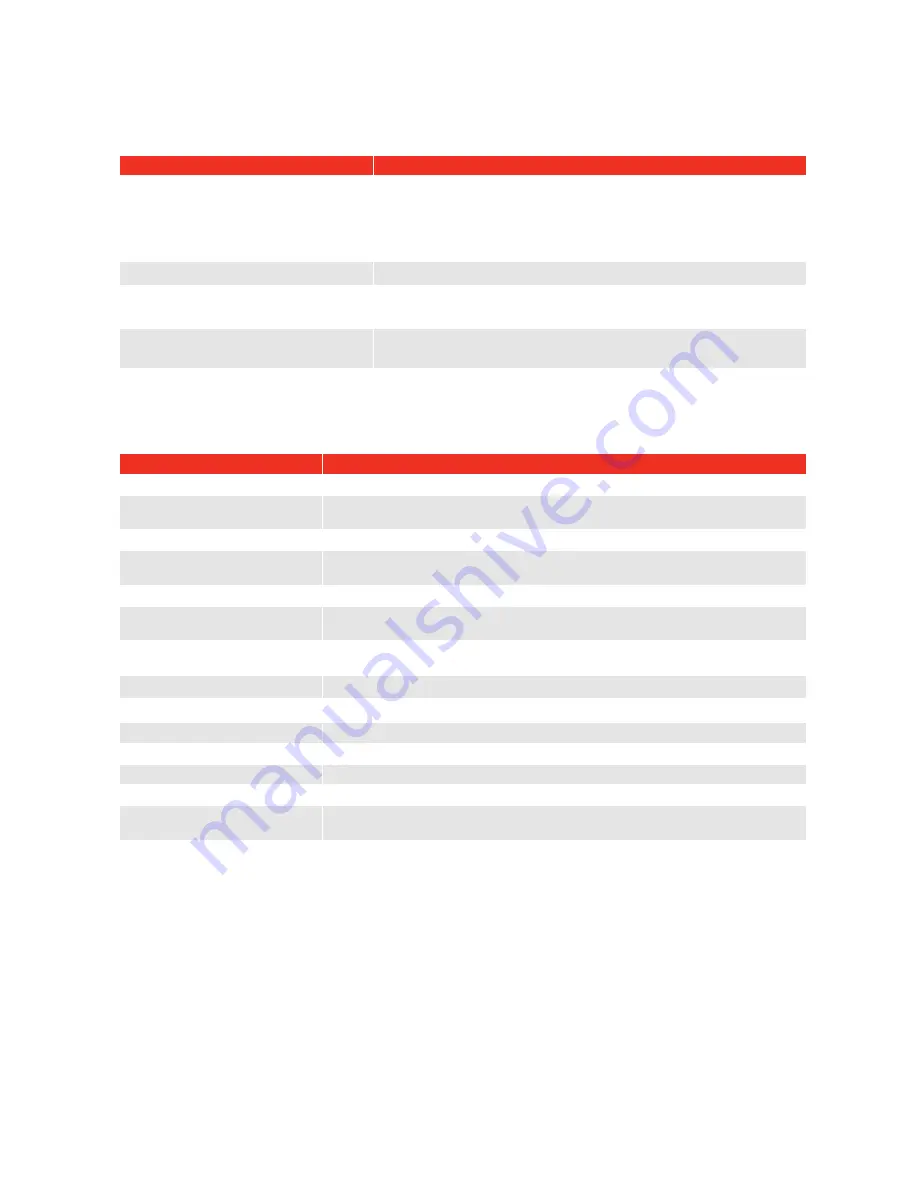
26
TROUBLE SHOOTING
The following is only a guide, for more complex faults please contact Norbar or a Norbar distributor.
Problem
Cause
Tool output does not rotate when
trigger pressed
Check air supply is functioning and connected
Check air pressure setting (at least 1 bar (14 psi))
Check correct setting of direction lever
Output drive square sheared, needs replacing
Gear train or air motor is damaged
Drive square is sheared
See maintenance section to replace drive square
Tool does not stall
Fastener sheared or thread stripped
Gear train or air motor is damaged
Free running speed becomes
impaired
Silencers are blocked / need replacing
GLOSSARY OF TERMS
Word or Term
Meaning
A/F
Across Flats
Air pressure setting data
Graph and or table supplied with all stall tools to show the air pressure
setting to produce required torque
Bi-directional
Tool capable of Clockwise and Counter-clockwise square rotation
Calibration Device
Torque measurement system to display peak torque using a joint simulator
or test fastener
Fastener
Bolt or stud to be tightened
Lubro Control Unit
Unit to provide filtering and lubrication along with pressure regulation. Not
supplied with tool
Nose Extension
A reaction type used where tool access is restricted, typical examples on
wheel nuts on heavy vehicles. Available as an accessory.
PneuTorque
®
Product name
PPE
Personal Protective Equipment
PTS
PneuTorque
®
Single-Motor
Reaction Bar
Item to counteract applied torque. Also called reaction plate
Stall Tool
Tool will stall due to air pressure set.
TBC
To be confirmed
Twist coupling / Claw
coupling
A type of air connector. Not recommended by Norbar.
Summary of Contents for PneuTorque PTS-52-500
Page 1: ...OPERATOR S MANUAL PNEUTORQUE PTS Part Number 34438 Issue 2 Original Instructions English ...
Page 2: ......
Page 27: ...25 ...
Page 29: ...27 NOTES ...