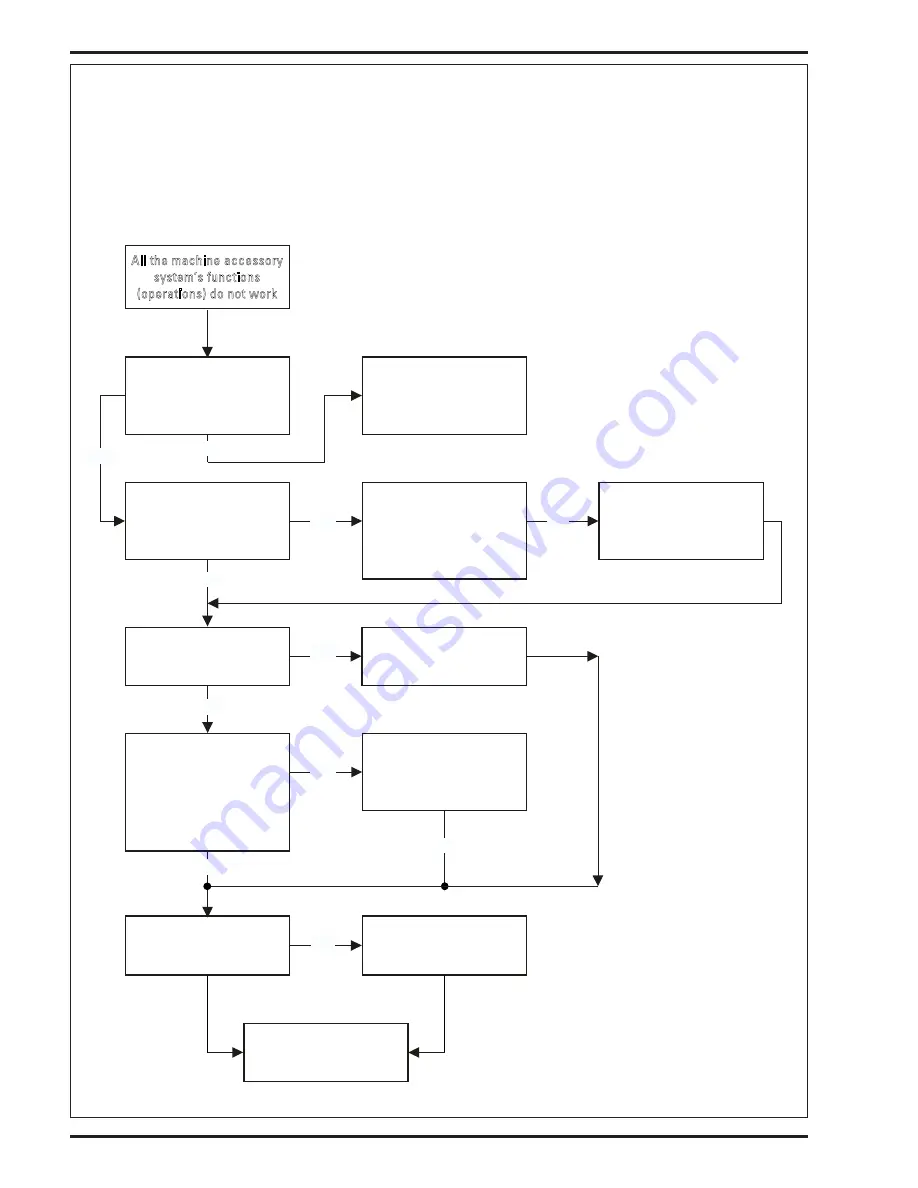
22
- FORM NO. 56043093 / Captor
™
4300, 4800, 5400
TROUBLESHOOTING GUIDE
Possible Symptom
1
All the machine accessory system’s functions (operations) do not work. Example: no brush, broom, vacuum and hopper functions etc.
Part A: Electrical Control Circuit
Note: Do all testing with Key Switch ON.
All the machine accessory
system’s functions
(operations) do not work
When key is first turned
on do all the A2 display
panel lights momentarily
turn on?
Test for the 12V output from
A1 wires WHT/BRN & BLK
Check the power & commu-
nication inputs to A2
•
Test circuit continuity of
wires BRN/BLU & GRN/BLU
•
Test for 12V power input
wires WHT/BRN & BLK
Sub a new A2 Display Panel
Machine system fixed all
functions now operational
See Hydraulic Load Circuit
Part B
Repair or replace
defective wiring
Replace A1 Main
Controller
No
No
Test for the 12V power
input to A1, wires VIO &
BLK
•
Check for a defective F2
circuit breaker (15A)
•
An open in either the circuit
battery (pos.) VIO wire or BLK
battery (neg.) wire
No
Repair or replace defective
parts.
Do the A2 panel lights now
function?
No
Yes
Replace the A1 Controller
No
Yes
Yes
No
No
Yes
Summary of Contents for Captor 4300
Page 13: ...FORM NO 56043093 Captor 4300 4800 5400 11 THIS PAGE IS INTENTIONALLY BLANK ...
Page 68: ...66 FORM NO 56043093 Captor 4300 4800 5400 ENGINE SYSTEM FIGURE 4 TIER II revised 7 08 ...
Page 74: ...72 FORM NO 56043093 Captor 4300 4800 5400 HYDRUALIC SYSTEM ...
Page 75: ...FORM NO 56043093 Captor 4300 4800 5400 73 HYDRAULIC SYSTEM ...
Page 88: ...86 FORM NO 56043093 Captor 4300 4800 5400 ELECTRICAL SYSTEM THIS PAGE IS INTENTIONALLY BLANK ...
Page 102: ...100 FORM NO 56043093 Captor 4300 4800 5400 AXP EDS SYSTEM revised 12 08 ...
Page 107: ......
Page 108: ......