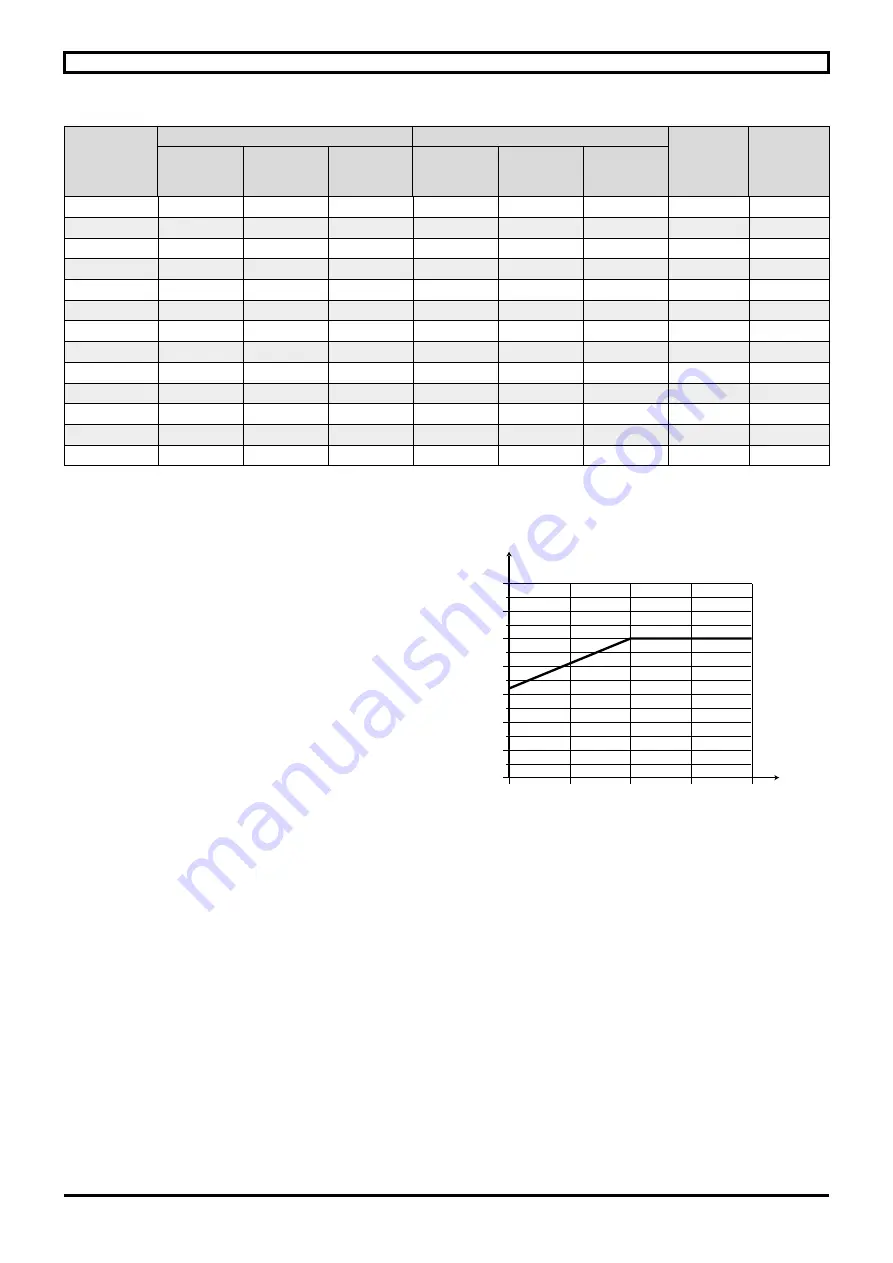
9
0
5
10
15
20
20 %
40 %
60 %
80 %
100 %
120 %
140 %
GENERAL INFORMATION
Installation guide Powerdrive MD Smart Equipment
5704 en - 2021.10 / b
525V to 690 V 3-phase supply
Switching frequency = 3 kHz - ambient temperature ≤ 40°C - altitude ≤ 1000 m.
Rating
Heavy duty
Normal duty
Imax (3s)
(A)
Imax (60s)
(A)
Pout at 525
V
(HP)
(1)
Pout at 690V
(kW)
(1)
Ico
(A)
Pout at 525
V
(HP)
(1)
Pout at 690V
(kW)
(1)
Ico
(A)
150TH
110
110
115
132
132
143
195
175
180TH
132
132
143
160
150
172
230
211
220TH
160
150
195
250
200
248
315
286
340TH
250
250
295
315
350
375
475
432
430TH
315
350
359
400
400
456
580
526
570TH
400
450
406
500
500
516
648
594
680TH
500
500
572
630
700
728
922
838
860TH
630
700
697
675
800
886
1125
1020
1140TH
675
900
787
850
1050
1000
1257
1152
1290TH
850
1050
1034
1000
1200
1315
1670
1515
1710TH
1000
1400
1169
1350
1600
1485
1866
1711
2280TH
1350
1800
1542
1500
2000
1960
2462
2257
2850TH
1500
2250
1928
1800
2500
2450
3110
2851
(1) Motor winding voltage
Frequency
(Hz)
% Ico or
% Imax (60 s)
1.4.3 - Derating at low frequency
Measuring the temperature of the power bridges in
conjunction with thermal modelling of the IGBTs ensures
protection against overheating of the
Powerdrive MD Smart
.
At low output (motor) frequencies, IGBT modules are subject
to significant temperature cycling, which can reduce their life.
To prevent this risk, the curve opposite indicates the derating
for output currents
Ico
and
Imax
when operating at low motor
frequencies in continuous operation.
1.4.4 - Standard equipment
The
Powerdrive MD Smart
is equipped as standard with a
line choke and high-speed fuses.
In some cases, after a specific design study the line choke
may be omitted. The inductance value of the transformer
supplying the equipment may act as a line choke.
1.4.5 - Derating according to the temperature
and switching frequency
See the derating tables on the next pages.
For intermediate switching frequencies (3.5 - 4.5 - 5.5 kHz),
the available current value will be the average of the upper
frequency and lower frequency currents.