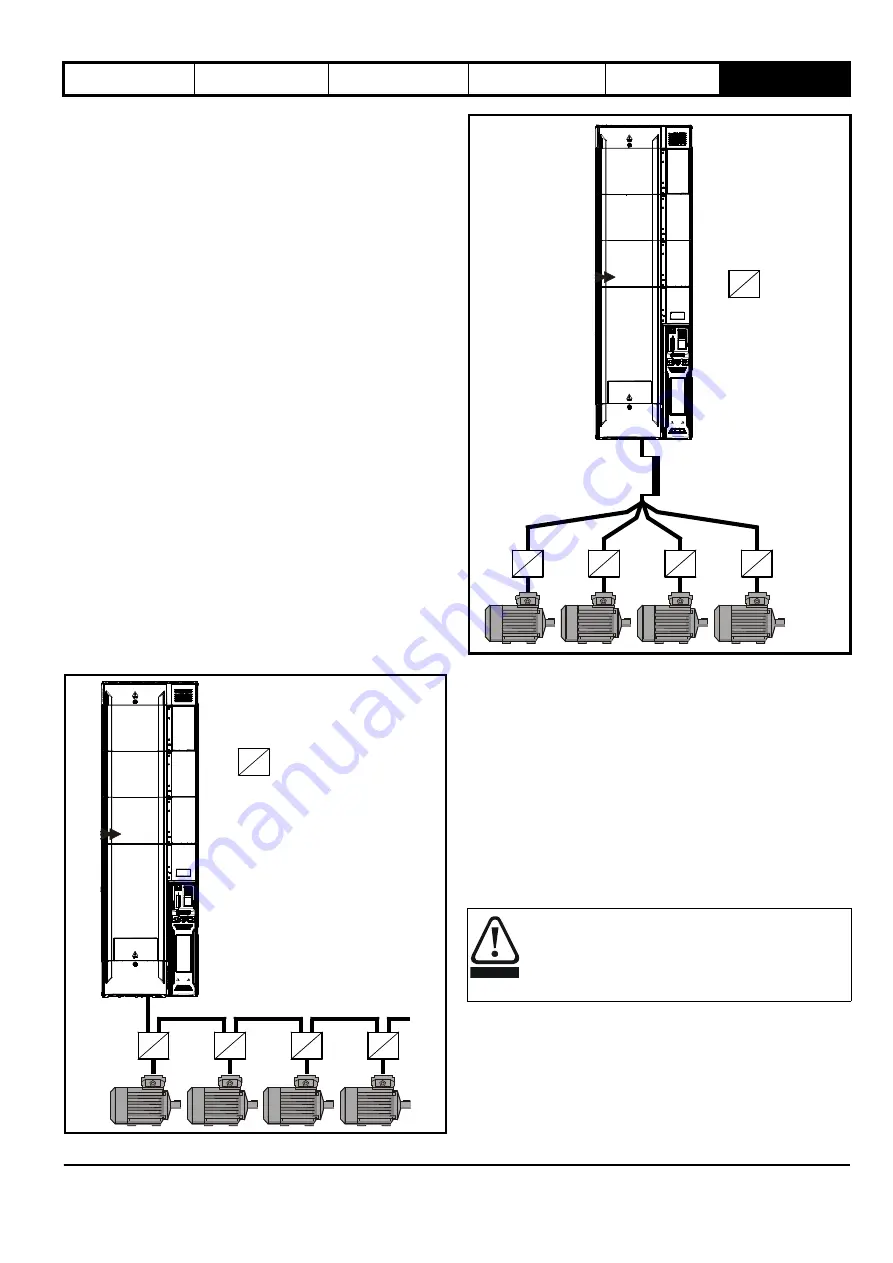
Unidrive M Modular Installation Guide
65
Issue Number: 2
Special precautions are recommended under the following conditions,
but only if the motor cable length exceeds 10 m:
•
AC supply voltage exceeds 500 V
•
DC supply voltage exceeds 670 V
•
Operation of 400 V drive with continuous or very frequent sustained
braking
•
Multiple motors connected to a single drive
For multiple motors, the precautions given in
should be followed.
For the other cases listed, it is recommended that an inverter-rated
motor be used. This has a reinforced insulation system intended by the
manufacturer for repetitive fast-rising pulsed voltage operation.
Users of 575 V NEMA rated motors should note that the specification for
inverter-rated motors given in NEMA MG1 section 31 is sufficient for
motoring operation but not where the motor spends significant periods
braking. In that case an insulation peak voltage rating of 2.2 kV is
recommended.
If it is not practical to use an inverter-rated motor, an output choke
(inductor) should be used. The recommended type is a simple iron-cored
component with a reactance of about 2 %. The exact value is not critical.
This operates in conjunction with the capacitance of the motor cable to
increase the rise-time of the motor terminal voltage and prevent
excessive electrical stress.
6.7.3 Multiple motors
Open-loop only
If the drive is to control more than one motor, one of the fixed V/F modes
should be selected (Pr
05.014
= Fd or SrE). Make the motor connections
as shown in Figure 6-10 and Figure 6-11. The maximum cable lengths in
Table 6-13 and Table 6-16 apply to the sum of the total cable lengths
from the drive to each motor.
It is recommended that each motor is connected through a protection relay
since the drive cannot protect each motor individually. For
A
connection, a
sinusoidal filter or an output inductor must be connected as shown in
Figure 6-11, even when the cable lengths are less than the maximum
permissible. For details of inductor sizes refer to the supplier of the drive.
Figure 6-10 Preferred chain connection for multiple motors
Figure 6-11 Alternative connection for multiple motors
6.7.4
A
/
Δ
motor operation
The voltage rating for
A
and
Δ
connections of the motor should always
be checked before attempting to run the motor.
The default setting of the motor rated voltage parameter is the same as
the drive rated voltage, i.e.
400 V drive 400 V rated voltage
A typical 3 phase motor would be connected in
A
for 400 V operation or
Δ
for 200 V operation, however, variations on this are common e.g.
A
690 V
Δ
400 V
Incorrect connection of the windings will cause severe under or over
fluxing of the motor, leading to a very poor output torque or motor
saturation and overheating respectively.
6.7.5 Output contactor
A contactor is sometimes required to be installed between the drive and
motor for safety purposes.
The recommended motor contactor is the AC3 type.
Switching of an output contactor should only occur when the output of
the drive is disabled.
Motor protection
relay
Chain connection (preferred)
Master
9E 10E
If the cable between the drive and the motor is to be
interrupted by a contactor or circuit breaker, ensure that the
drive is disabled before the contactor or circuit breaker is
opened or closed. Severe arcing may occur if this circuit is
interrupted with the motor running at high current and low
speed.
Star connection
Inductor
Motor
protection
relay
Master
9E 10E
WARNING
Summary of Contents for 09201760D
Page 92: ...0478 0141 02...