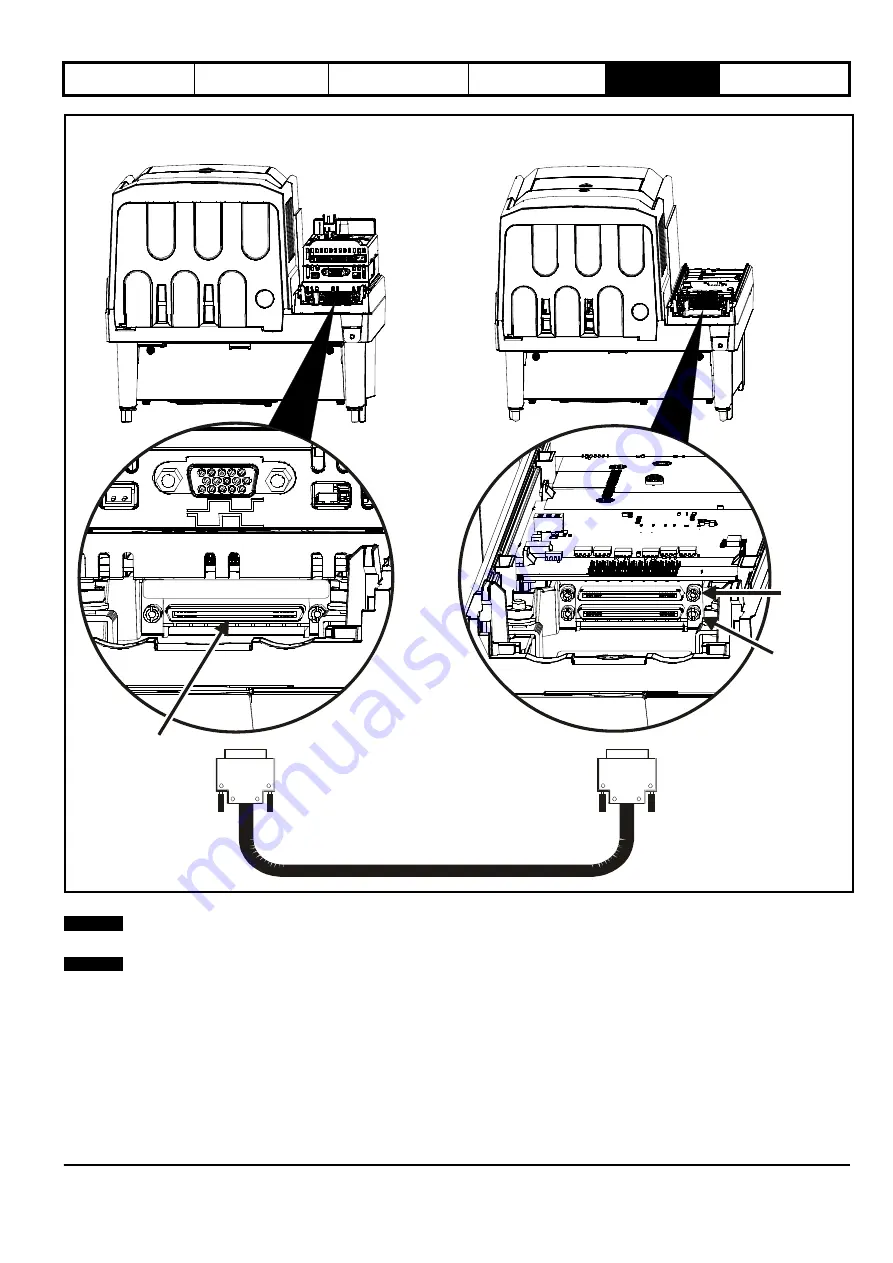
Unidrive M Modular Installation Guide
31
Issue Number: 2
Figure 5-10 Parallel control connections
*Only supplied with follower drive.
N
The parallel cable should be routed according to the rules shown in Figure 6-19
Sensitive signal circuit clearance
on page 72 for the control cable.
N
The screw locks on the parallel cable must be fully tightened.
Paralleling cable*
Input from
master
to follower
Output to
next
follower
Control master pod
Output from
master to
follower
Control follower pod
NOTE
NOTE
Summary of Contents for 09201760D
Page 92: ...0478 0141 02...