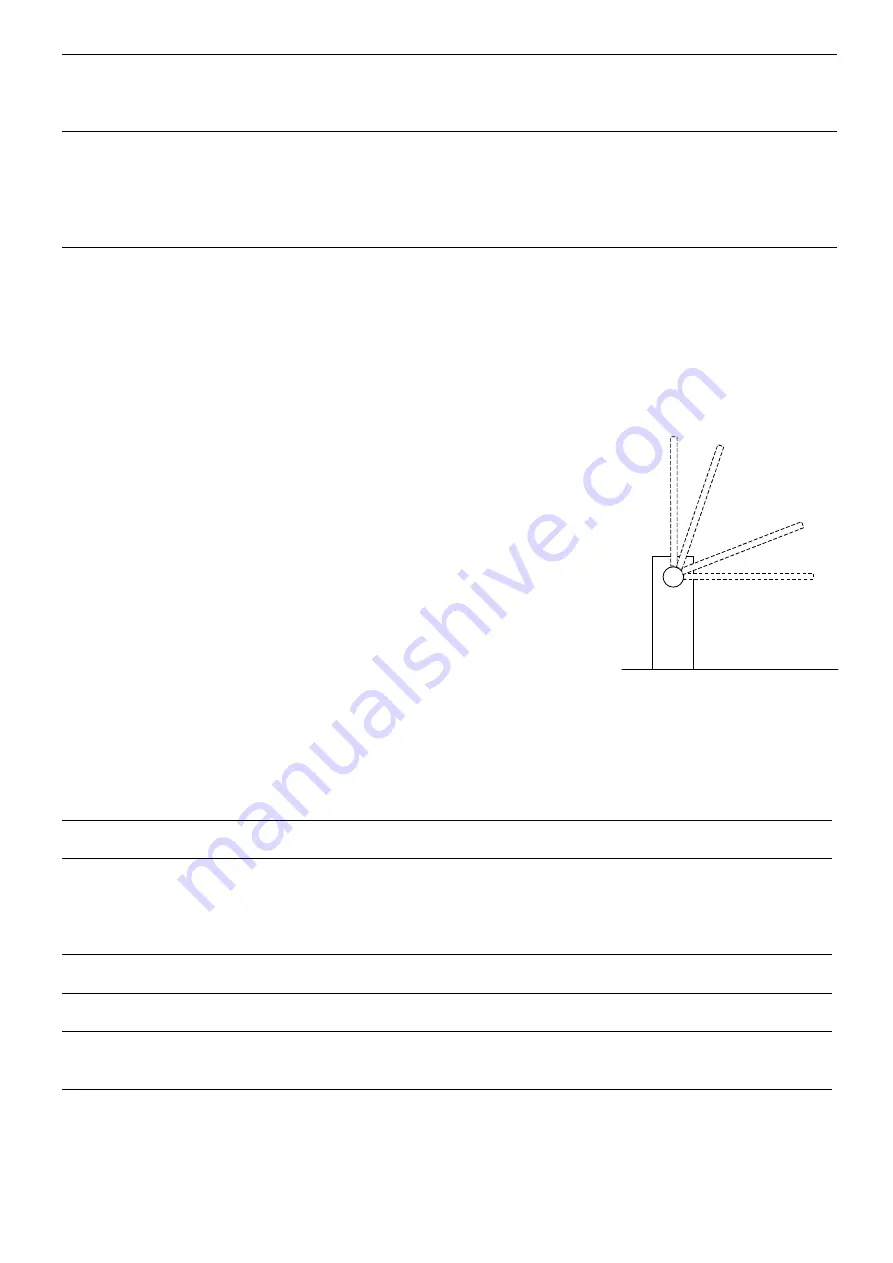
33
must switch off; when the bar is open only the open limit switch LED must switch off; if this is not
the case, disconnect the power supply and invert the limit switches connector
leave the bar at an angle of approximately 45° so that it is free to move in the opening and closing
directions, and then lock the barrier
•
Check that the bar moves in the correct direction, i.e.:
press the Close button and check that the bar moves in the closing direction
if the bar moves in the opening direction press the Close button again to stop the movement, then
disconnect the power supply and invert the positions of two of the motor feeding wires
irrespective of the direction of movement of the bar, it is advisable to stop the movement
immediately by pressing the Close button again
3URJUDPPLQJDQGDGMXVWPHQWV
If the check performed on the various connections produces positive results, you can now start the mechanical
stops search phase. This procedure is necessary because the SIA20 control unit must measure the distance
travelled by the gear motor to bring the bar from fully closed (position 0) to fully open (position 1).
The mechanical stops search procedure can be performed using initial search mode or automatic search mode.
Following the "initial search" or "automatic search", if you wish you can edit the RA and RC deceleration
positions by means of a manual programming procedure.
Position 0:
this is the point at which the bar is in the closed condition,
corresponding to the closing stroke mechanical stop.
Position RC:
this is the position at which the bar must start its deceleration
phase during the closing manoeuvre.
Position RA:
this is the position at which the bar must start its deceleration
phase during the opening manoeuvre.
Position 1:
this is the point at which the bar is in the fully open condition,
corresponding to the opening stroke mechanical stop.
0HFKDQLFDOVWRSVLQLWLDOVHDUFK
The "mechanical stops initial search" procedure is executed automatically as the first manoeuvre following
installation of the barrier.
7RDFWLYDWHWKHPHFKDQLFDOVWRSVLQLWLDOVHDUFK
5. release the barrier, move it clear of the mechanical stops so that it is free to move in the opening and
closing directions, and then lock the barrier
6. briefly press the Close button on the board or generate a command pulse on the inputs and wait for the
control unit to perform a low speed closing manoeuvre to position 0, a low speed opening manoeuvre to
position 1, and a high speed closing manoeuvre to position 0.
1RWH
if after transmitting the command the first movement is an opening manoeuvre, transmit a second
command to stop the procedure and then invert the polarity of the motor feeding wires.
7. When the sequence described above is concluded, a mathematical operation is executed to calculate the
deceleration positions (RA and RC) automatically.
8. The mechanical stops "initial search" procedure is now terminated and the gear motor is ready for use. Set
up the "functions" dip switches as required.
1RWH
If one of the safety devices should trip or another command pulse is received during the "initial
search" procedure, movement of the bar will be interrupted immediately; in this case the above procedure
must be repeated starting from step 1.
0HFKDQLFDOVWRSVDXWRPDWLFVHDUFK
As an alternative to the "Initial search" procedure the "Mechanical stops automatic search" procedure can be
activated at any time without having to clear the memory. The procedure performs the mechanical stops
0
RA
RC
1
Summary of Contents for Signo
Page 1: ...1 ISTSG REV 00 01 ...
Page 2: ...2 1 2 A B SIGNO3 SIGNO4 SIGNO6 ...
Page 3: ...3 4 5 7 3 6 ...
Page 4: ...4 8 9 11 10 12 ...
Page 25: ...25 ISTSG REV 00 01 ...