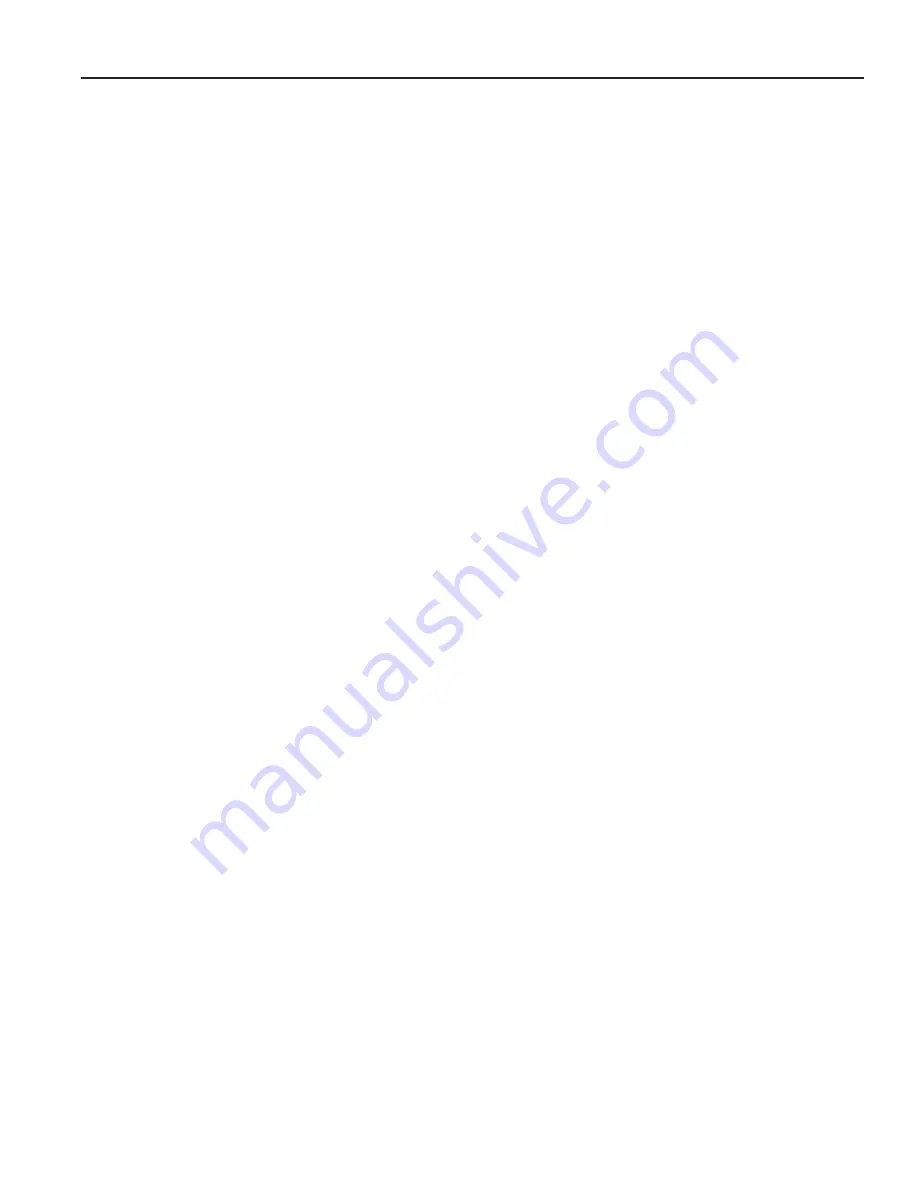
FC Flow Computer
5
Step 3 : Compute the Volumetric Flow-
Volumetric flow is the term given to the flow in volume units.
The value is computed based on the flowmeter input type
selected and augmented by any performance enhancing
linearization that has been specified by the user.
Step 4: Compute the Corrected Volume Flow at Reference
Conditions-
In the case of a corrected liquid or gas volume flow calculation,
the corrected volume flow is computed as required by the
selected compensation equation.
Step 5 : Compute the Mass Flow-
All required information is now available to compute the mass
flow rate as volume flow times density. A heat flow computation
is also made if required.
Step 6: Check Flow Alarms-
The flow alarm functions have been assigned to one of
the above flow rates during the setup of the instrument. A
comparison is now made by comparing the current flow rates
against the specified hi and low limits.
Step 7: Compute the Analog Output-
This designated flow rate value is now used to compute the
analog output.
Step 8: Compute the Flow Totals by Summation-
A flow total increment is computed for each flow rate. This
increment is computed by multiplying the respective flow rate
by a time base scaler and then summing. The totalizer format
also includes provisions for total rollover.
Step 9: Pulse Output Service-
The pulse output is next updated by scaling the total increment
which has just been determined by the pulse output scaler and
summing it to any residual pulse output amount.
Step 10: Update Display and Printer Output-
The instrument finally runs a task to update the various table
entries associated with the front panel display and serial
outputs.
Instrument Setup
The setup is password protected by means of a numeric lock
out code established by the user. The help line and units of
measure prompts assure easy entry of parameters.
An EZ Setup function is supported to rapidly configure the
instrument for first time use. A software program is also
available which runs on a PC using a RS-232 Serial for
connection to the Flow Computer. Illustrative examples may
be down loaded in this manner.
The standard setup menu has numerous subgrouping of
parameters needed for flow calculations. There is a well
conceived hierarchy to the setup parameter list. Selections
made at the beginning of the setup automatically affect
offerings further down in the lists, minimizing the number of
questions asked of the user.
In the setup menu, the flow computer activates the correct
setup variables based on the instrument configuration, the
flow equation, and the hardware selections made for the
compensation transmitter type, the flow transmitter type,
and meter enhancements (linearization) options selected. All
required setup parameters are enabled. All setup parameters
not required are suppressed.
Also note that in the menu are parameter selections which have
preassigned industry standard values. The unit will assume
these values unless they are modified by the user.
Most of the process input variables have available a “default”
or emergency value which must be entered. These are the
values that the unit assumes when a malfunction is determined
to have occurred on the corresponding input.
It is possible to enter in a nominal constant value for
temperature or density, or pressure inputs by placing the
desired nominal value into the default values and selecting
"manual". This is also a convenience when performing bench
top tests without simulators.
The system also provides a minimum implementation of an
“audit trail” which tracks significant setup changes to the unit.
This feature is increasingly being found of benefit to users
or simply required by Weights and Measurement Officials
in systems used in commerce, trade, or “custody transfer”
applications.
Simulation and Self Checking:
This mode provides a number of specialized utilities required
for factory calibration, instrument checkout on start-up, and
periodic calibration documentation.
A service password is required to gain access to this
specialized mode of operation. Normally quality, calibration,
and maintenance personnel will find this mode of operation
very useful.
Many of these tests may be used during start-up of a new
system. Output signals may be exercised to verify the electrical
interconnects before the entire system is put on line.
The following action items may be performed in the Diagnostic
Mode:
Print Calibration/Maintenance Report
View Signal Input (Voltage, Current, Resistance, Frequency)
Examine Audit Trail
Perform a Self Test
Perform a Service Test
View Error History
Perform Pulse Output Checkout / Simulation
Perform Relay Output Checkout / Simulation
Perform Analog Output Checkout / Simulation
Calibrate Analog Inputs using the Learn Feature
Calibrate Analog Output using the Learn Feature
Schedule Next Maintenance Date
Note that a calibration of the analog input/output will advance
the audit trail counters since it effects the accuracy of the
system.
Summary of Contents for FC
Page 2: ......