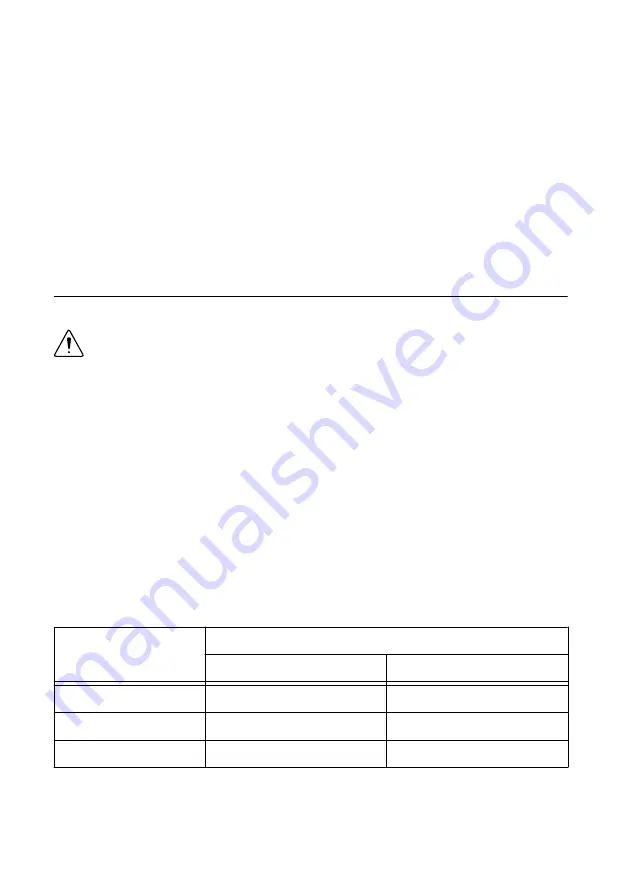
1.
Test system characterization—Characterize the amplitude imbalance of the output ports
on your power splitter. The results of this step are used as a correction in the flatness and
bandwidth verification procedure.
2.
Verification—Verify the existing operation of the device. This step confirms whether the
device is operating within the published specification prior to adjustment.
3.
Adjustment—Perform an external adjustment of the calibration constants of the device.
The adjustment procedure automatically stores the calibration date and temperature on
the EEPROM to allow traceability.
4.
Re-verification—Repeat the Verification procedure to ensure that the device is operating
within the published specifications after adjustment.
Refer to the following sections to complete each procedure.
Test System Characterization
The following procedures characterize the test equipment used during verification.
Caution
The connectors on the device under test (DUT) and test equipment are
fragile. Perform the steps in these procedures with great care to prevent damaging
any DUTs or test equipment.
Zeroing the Power Sensor
1.
Ensure that the power sensor is not connected to any signals.
2.
Zero the power sensor using the built-in function, according to the power sensor
documentation.
Characterizing Power Splitter Amplitude Imbalance
This procedure characterizes the amplitude imbalance of the two output ports of the power
splitter over a range of frequencies.
The results of the characterization are later used as a correction in the
Verifying Flatness and
Bandwidth
procedure.
Table 2.
Power Splitter Characterization
Configuration
Test Point
Frequency (MHz)
Amplitude (dBm)
1
0.05
-0.5
2
50.1
-0.5
3
100.1
-0.5
1.
Connect an SMA (f)-to-N (f) adapter to the power sensor. Refer to this assembly as the
power sensor
.
2.
Zero the power sensor as described in the
Zeroing the Power Sensor
section.
NI PXIe-5170R Calibration Procedure
|
© National Instruments
|
7