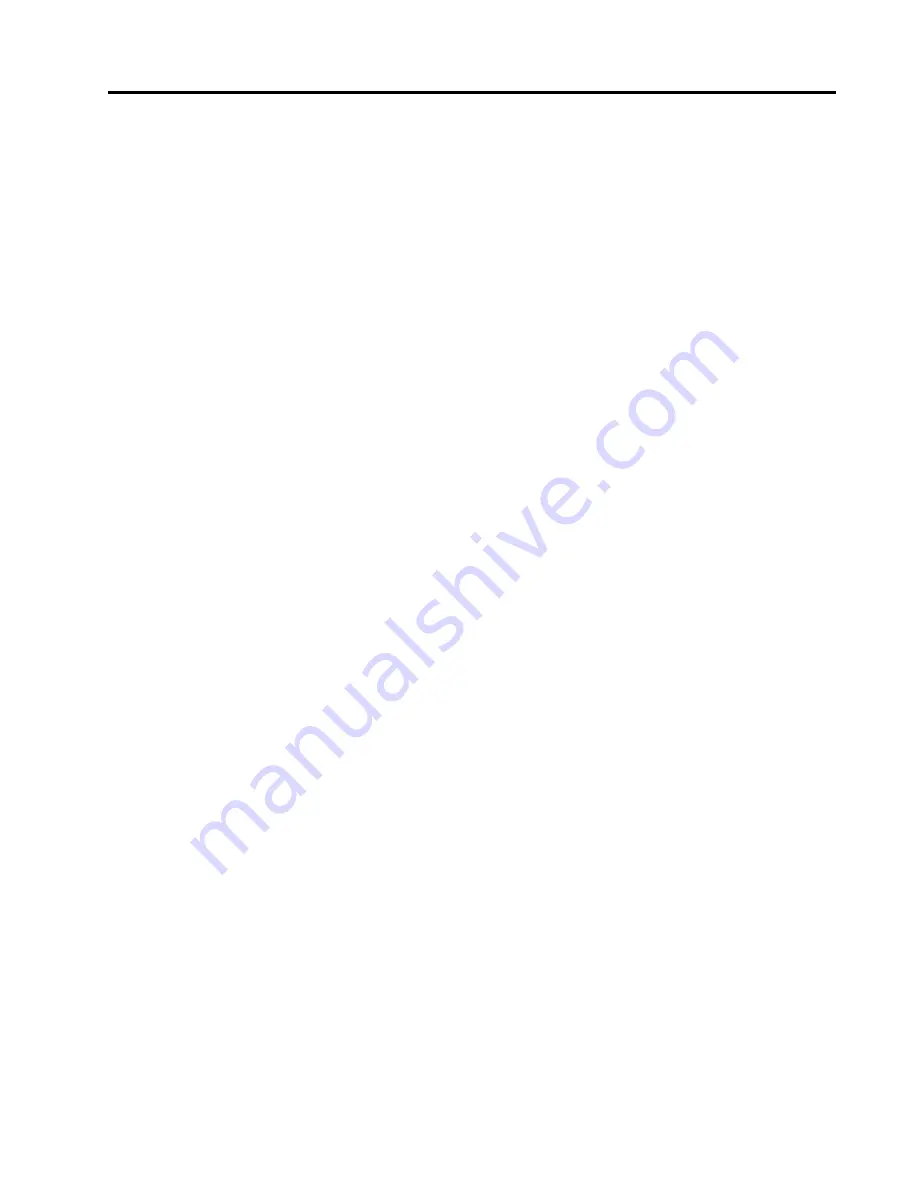
MS-2102
9.5
Chapter 9
Commissioning
the heat trace. For powerlimit to work properly, the
powerlimit current should be below the nominal current
rating of the heat trace. For example, if the heat trace
draws 20A at its rated voltage and the application only
requires 75% of its rated output, a powerlimit current of
15A will achieve a 75% reduction in power. With the
powerlimit current set, the controller attempts to clamp the
output current at that value.
The minimum powerlimit current setting should be greater
than 10% of the nominal load current. This is because
powerlimiting operates in 10% resolution. Choosing a
powerlimit current below 10% causes the heater not to
turn on since the average heater current at 10% (minimum
duty cycle) exceeds the powerlimit current setting.
Be aware of how current alarms operate with duty cycle
changes. Low current alarm is based on the nominal
current ratings of the heat trace, not the average current.
The low current alarm function converts actual current
readings to the expected current value of the heat trace
operating at 100% duty cycle prior to comparing against
alarm settings. When using powerlimit, the high current
alarm is disabled to prevent false alarms due to
measurement error of the algorithm at low duty cycles.
The error is always positive and therefore does not affect
low current alarms.
Control Scheme
The MS-2102 controller supports two types of control
scheme: on/off and proportional. The default is on/off
switching which is used for majority of the applications.
When on/off switching is used, the deadband setting
determines the heater turn off temperature above the
heater setpoint and the heater turn on temperature below
the heater setpoint. The deadband setting is user definable
located at SETPOINTS\HEATER\SETUP\DEADBAND.
In applications requiring tighter control, you can use
proportional control. To enable proportional control,
locate message SETPOINTS\HEATER
SETUP\PROPORTIONAL CONTROL. There is no
proportional gain setting as this is automatically set by the
controller to minimize errors. For further details how the
proportional control function operates, refer to
Chapter 1
Theory of Operation.
RTD
In the event of complete RTD failure, the controller can
force the heater to default on or off. This is defined by
message SETPOINT\HEATER SETUP\ IF RTD FAILS
HEATER GOES. The choice of
on
or
off
depends on the
application.
Cost of Power
In order for the energy cost functions to provide correct
information, you should enter the cost per KWh for
electrical power at SETPOINT\SYSTEM SETUP\COST
PER KWh.
Completing the Installation
At this point, the controller has been setup with enough
information to control and monitor the heat trace. Other
functions are less critical and a description on how these
function operate is located in
Chapter 6 Setpoint Values
.
Read chapter 6 to gain an understanding of all the
functions in order to customize the controller to the
application requirements.