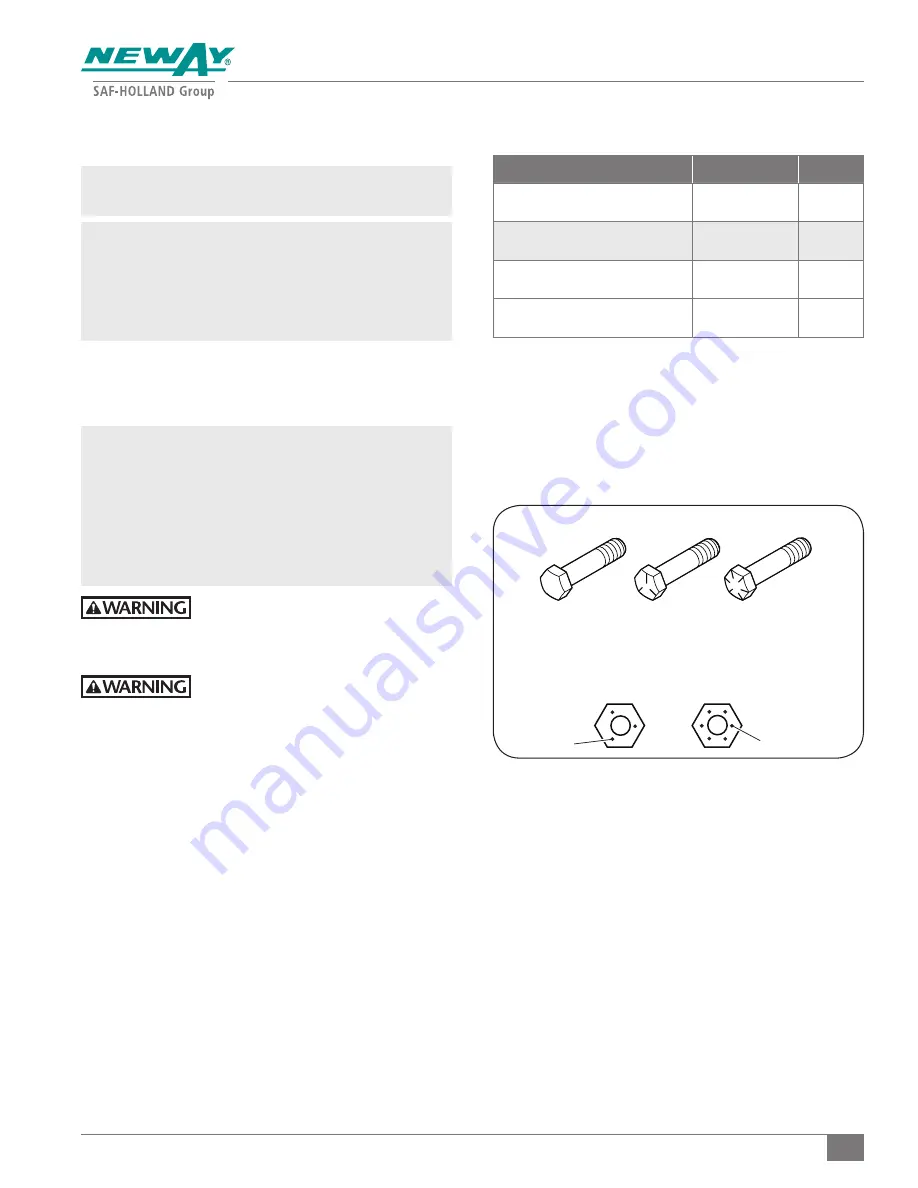
15
XL-PS20053RM-en-US Rev A · 2017-10-06 · Amendments and Errors Reserved © SAF-HOLLAND, Inc., SAF-HOLLAND, HOLLAND, NEWAY, SAF, and logos are trademarks of SAF-
HOLLAND S.A., SAF-HOLLAND GmbH, and SAF-HOLLAND, Inc.
Torque Specifications
11. Torque Specifications
NOTE:
Torque specifications listed in this section
are with clean
lubricated/coated threads, supplied by SAF-HOLLAND.
IMPORTANT:
The use of special lubricants with friction
modifiers, such as Anti-Seize or Never-Seez
®
,
without written approval from SAF-HOLLAND
Engineering, will void warranty and could
lead to over torquing of fasteners or other
component issues.
General Information
The torque specifications listed throughout the manual are
applied to the lock nut and NOT the bolt.
IMPORTANT:
Most of the fasteners used in this suspension
are Grade 8 bolts and Grade C lock nuts.
These fasteners have the strength and
hardness properties required for their
particular function. They MUST be replaced
with fasteners of the same grade, size and
form as the original in order to prevent
failure
(Figure 10)
.
Failure to use the proper fasteners when
servicing the suspension could cause
component failure which, if NOT avoided,
could result in death or serious injury.
Failure to properly torque all fasteners
will result in component failure which,
if NOT avoided, could result in death or
serious injury.
All fasteners MUST be re-torqued after the first 100 hours
of service or 5,000 miles (8,000 km).
Refer to vehicle OEM for torque specifications for vehicle
frame fastener hardware.
COMPONENT
TORQUE RANGE
SIZE
Clevis Pin Assembly
18-24 ft-lb
24-33 N•m
5/16"-18
Chamber Bracket
37-50 ft-lb
50-68 N•m
1/2"-13
LSZ13 Pivot Connections
200-250
ft-lb
271-339 N•m
3/4"-10
LSZ20 Pivot Connections
330-370
ft-lb
447-502 N•m
7/8"-14
Table 1
GRADE 1 OR 2
BOLT GRADE MARKINGS
LOCK NUT GRADE MARKINGS
3 DOTS
LOCK NUT
GRADE B
LOCK NUT
GRADE C
6 DOTS
GRADE 5
GRADE 8
Figure 10