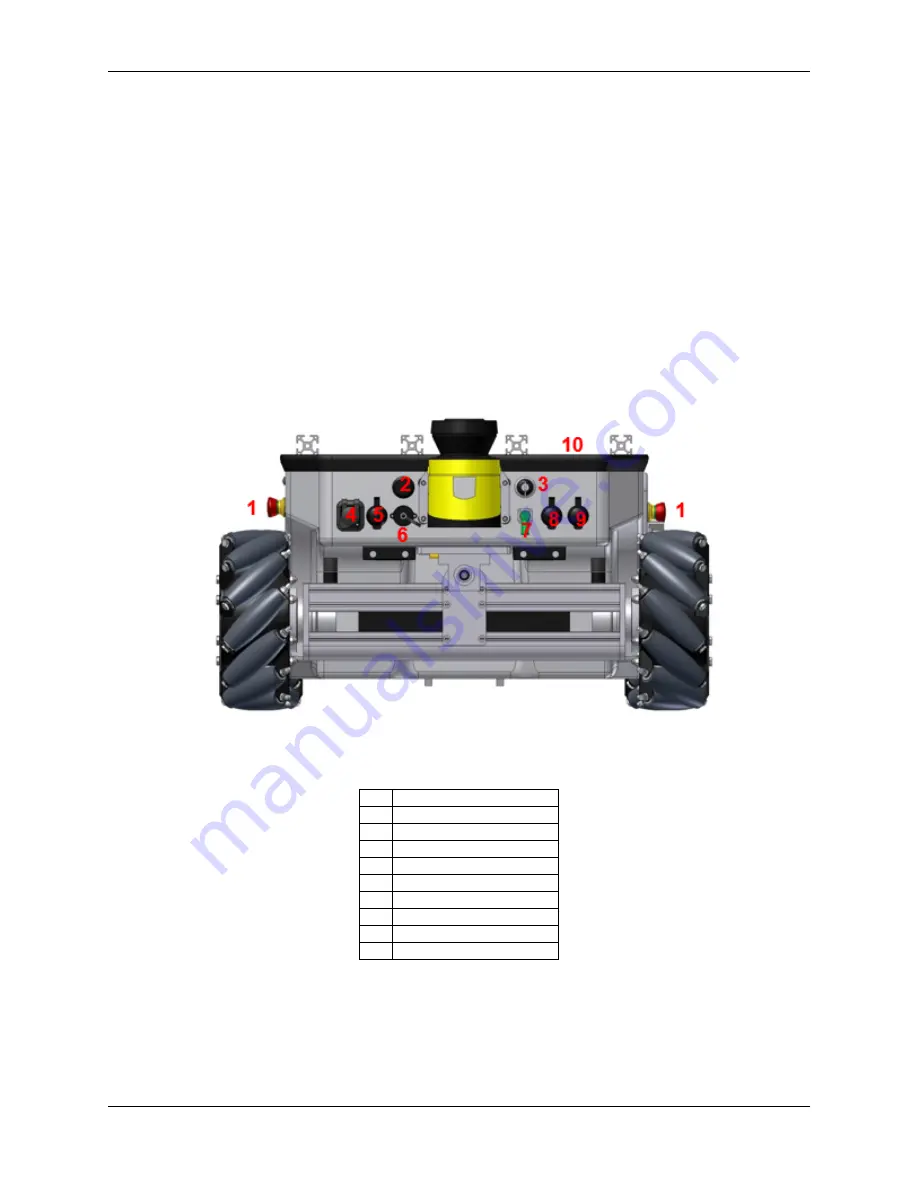
CHAPTER 2. MPO-500
2.2. OPERATING ELEMENTS
Laser Scanner Positions
The height of the scanning plane of the laser scanners must be chosen according to the applications safety require-
ments. In case the robot is to operate fully autonomously and without supervision in an area where it might encounter
unconscious people the scanning plane should be no more than 200 mm above the ground.
Each laser scanner has a 270° wide field of view which is symmetric to the scanner housing. Therefore the positions
of the laser scanners must also be chosen in consideration of blind spots.
Please contact Neobotix if the positions of the laser scanners has to be modified.
2.2 Operating Elements
The figure below shows the tail of the MPO-500 and the most important operating elements.
Fig. 1: Operating elements of the MPO-500
1
Emergency stop buttons
2
Brake release button
3
Key switch
4
HDMI socket
5
Wireless joystick receiver
6
Charging socket
7
Connector for 2nd scannerr
8
Ethernet socket
9
USB socket
10
LC-Display
2.2.1 Emergency Stop Buttons
When one of these buttons is pressed the robot is immediately set to emergency stop. All drives are disconnected from
power supply and the fail-safe brakes are engaged. This state can be reset by unlocking the emergency stop buttons
12