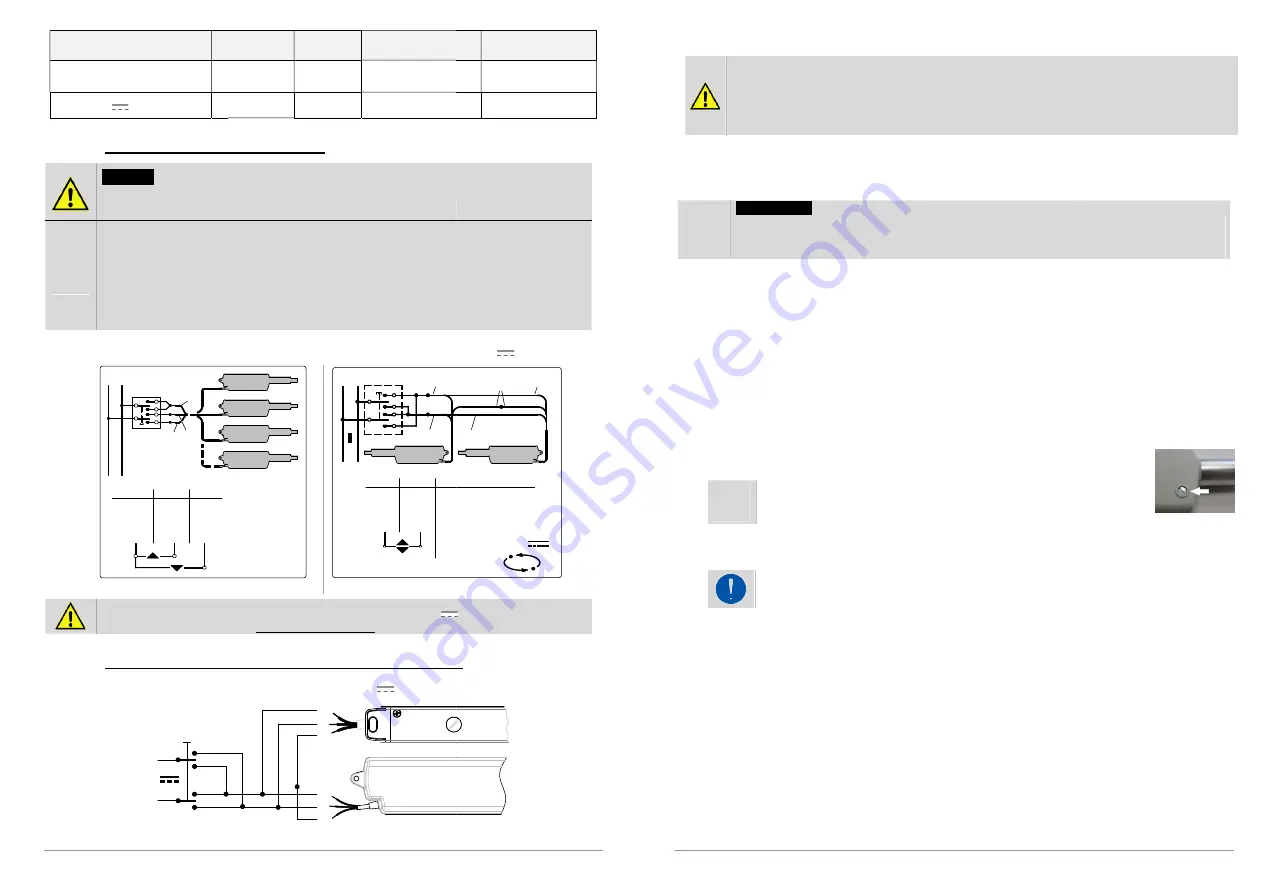
Supply voltage
110-230V~ 50/60Hz
24V
Syncro³
11.1. Machine electrical connections
C
AUTION
Where several machines a
follow the correct electrical connections; incorrect connection can damage the
machines and create a hazardous situation.
The electrical connection for communication and synchronisation (Green cable) must
be made with a simple unipolar terminal of an a
supplied).
A stable and safe connection, with a good electrical contact (copper to copper) is
essential to prevent communication disturbances as the forward voltage is very low.
The communication wires can have a maximum
Wiring diagram 110/230V~
SCHWA RZ
HELLBLAU
BRA UN
F
N
BLEU CLAIR
AZUL
MA RRON
MA RRÓN
NEGRO
NOIRE
1
3
2
AZZURRO
LIGHT BLUE
1
MA RRONE
NERO
BLA CK
2
BROWN
3
110/230V ~
10
0-
23
0V
~
50
/6
0H
z
IMPORTANT FOR PRODUCT SAFETY
Green wire "3" is not used,
11.2. Connection with a K
24V
+
-
11
Cable
length
Number
of wires
Power wires
2 m
3
L
IGHT
B
LUE
,
B
LACK
B
ROWN
2 m
3
R
ED
,
B
LACK
Machine electrical connections
Where several machines are connected in a Syncro³ system, always
follow the correct electrical connections; incorrect connection can damage the
machines and create a hazardous situation.
The electrical connection for communication and synchronisation (Green cable) must
be made with a simple unipolar terminal of an appropriate size (the terminal is
A stable and safe connection, with a good electrical contact (copper to copper) is
essential to prevent communication disturbances as the forward voltage is very low.
The communication wires can have a maximum length of 10 metres.
110/230V~
Wiring diagram
110/230V ~
- +
24
V
1
2
1
2
3
ROT
ROJO
ROUGE
RED
ROSSO
SCHWARZ
NEGRO
NOIRE
BLACK
NERO
GRÜN
VERDE
VERT
GREEN
VERDE
IMPORTANT FOR PRODUCT SAFETY
:
in motors with a 24V
Green wire "3" is not used,
it must be insulated
.
Connection with a K-LOCK electromechanical lock
Wiring diagram 24V
2
3
1
N
V
R
K-LOCK
ROCK
(24V - 24V SYNCRO
3
)
Communication
wires
LACK
LACK
G
REEN
re connected in a Syncro³ system, always
follow the correct electrical connections; incorrect connection can damage the
The electrical connection for communication and synchronisation (Green cable) must
ppropriate size (the terminal is
A stable and safe connection, with a good electrical contact (copper to copper) is
essential to prevent communication disturbances as the forward voltage is very low.
length of 10 metres.
Wiring diagram 24V
3
1
2
GRÜN
VERDE
VERT
GREEN
VERDE
24V
SYNCRO
CÂBLE DE CONTRÔLE
CABLE DE CONTROL
LEITUNGSÜBER-WACHUNG
CONTROL WIRE
FILO DI COMUNICAZIONE
, supply voltage, if the
LOCK electromechanical lock
12. PROGRAMMING THE ACTUATOR
Before performing the
make sure that the electrical power supplied to the
indicated on the technical data label on the machine,
check that the wires are correctly connected, in accordance with the wiring diagram
in the previous chapter of
After testing, the actuator leaves the factory
available. To set the desired stroke, you will have to once more perform the opening
end-position setting procedure, as indicated below.
IMPORTANT
Where two or more ROCK actuators are connected in a Syncro³
system, or with K-LOCK electromechanical locks, the recognition of the group is
completely automatic and occurs in the first manoeuvre when programming the
stroke end positions.
The closing stroke end position
stops due to the current absorption that occurs when the window or sunscreen blades
close, that is, when the power absorbed exceeds a threshold pre
The actuator considers any stroke
After each closure or electronic protection intervention, the rod moves in the
direction by about 0,5-1,0 mm, to allow the right compression of the
the internal mechanical components of the actuator.
The
RESET
procedure must be carried out with the rod detached from the bracket. The
stroke end-position setting or
RESET
sequence:
1. Fully unscrew and remove the magnet
figure at the side)
on the actuator.
NOTE: with several actuators in a Syncro³ system, there is NO
need to remove the
as their recognition process is automatic;
2. Supply power to move
actuators, the rods move independently from each other.
C
AUTION
:
if a K-LOCK is present
it to switch to the O
3. The actuator moves automatically in the
and then (still automatically) in the
4. Disconnect the power to the machine.
5. Refit the screw with the magnet and screw it into its housing;
6. Connect the actuator rod to the bracket.
7. The opening stroke can be customi
stage. Command the actuator to
or let it run to the stroke
and used as the stroke
synchronisation.
8. Give a close command and check that the rod
retracts to the stroke end position.
12
PROGRAMMING THE ACTUATOR
Before performing the stroke end-position setting procedure,
make sure that the electrical power supplied to the
indicated on the technical data label on the machine,
check that the wires are correctly connected, in accordance with the wiring diagram
the previous chapter of this manual.
After testing, the actuator leaves the factory programmed to open to the maximum stroke
available. To set the desired stroke, you will have to once more perform the opening
setting procedure, as indicated below.
Where two or more ROCK actuators are connected in a Syncro³
LOCK electromechanical locks, the recognition of the group is
completely automatic and occurs in the first manoeuvre when programming the
end positions.
position is automatic and cannot be programmed. The actuator
stops due to the current absorption that occurs when the window or sunscreen blades
when the power absorbed exceeds a threshold pre-set by the manufacturer.
stroke end position within the last 1 cm valid.
After each closure or electronic protection intervention, the rod moves in the
0 mm, to allow the right compression of the
the internal mechanical components of the actuator.
must be carried out with the rod detached from the bracket. The
RESET
procedures consist in the following steps, performed in
Fully unscrew and remove the magnet-holder screw
(indicated in the
on the actuator.
NOTE: with several actuators in a Syncro³ system, there is NO
need to remove the magnet-holder screw on the other machines
as their recognition process is automatic;
in either the opening or closing direction
actuators, the rods move independently from each other.
LOCK is present (24V ROCK), you must wait around 4 seconds for
O
PEN
position;
The actuator moves automatically in the
C
LOSE
direction up to the
and then (still automatically) in the
O
PEN
direction, by about 3 cm.
power to the machine.
Refit the screw with the magnet and screw it into its housing;
Connect the actuator rod to the bracket.
The opening stroke can be customised as desired and must be determined at this
stage. Command the actuator to
O
PEN
to the desired distance (stroke customisation)
stroke end position.
This outward distance will be memorised
stroke end position in
O
PEN
. With Syncro³, the
Give a close command and check that the rod
(or rods, with synchronised actuators)
end position.
position setting procedure,
make sure that the electrical power supplied to the actuator matches that
check that the wires are correctly connected, in accordance with the wiring diagram
to open to the maximum stroke
available. To set the desired stroke, you will have to once more perform the opening stroke
Where two or more ROCK actuators are connected in a Syncro³
LOCK electromechanical locks, the recognition of the group is
completely automatic and occurs in the first manoeuvre when programming the
is automatic and cannot be programmed. The actuator
stops due to the current absorption that occurs when the window or sunscreen blades
set by the manufacturer.
end position within the last 1 cm valid.
After each closure or electronic protection intervention, the rod moves in the opposite
0 mm, to allow the right compression of the gaskets and/or relax
must be carried out with the rod detached from the bracket. The
the following steps, performed in
(indicated in the
NOTE: with several actuators in a Syncro³ system, there is NO
holder screw on the other machines
direction. With Syncro³
you must wait around 4 seconds for
direction up to the stroke end position
direction, by about 3 cm.
ed as desired and must be determined at this
distance (stroke customisation)
This outward distance will be memorised
ncro³, the actuators move in
with synchronised actuators)