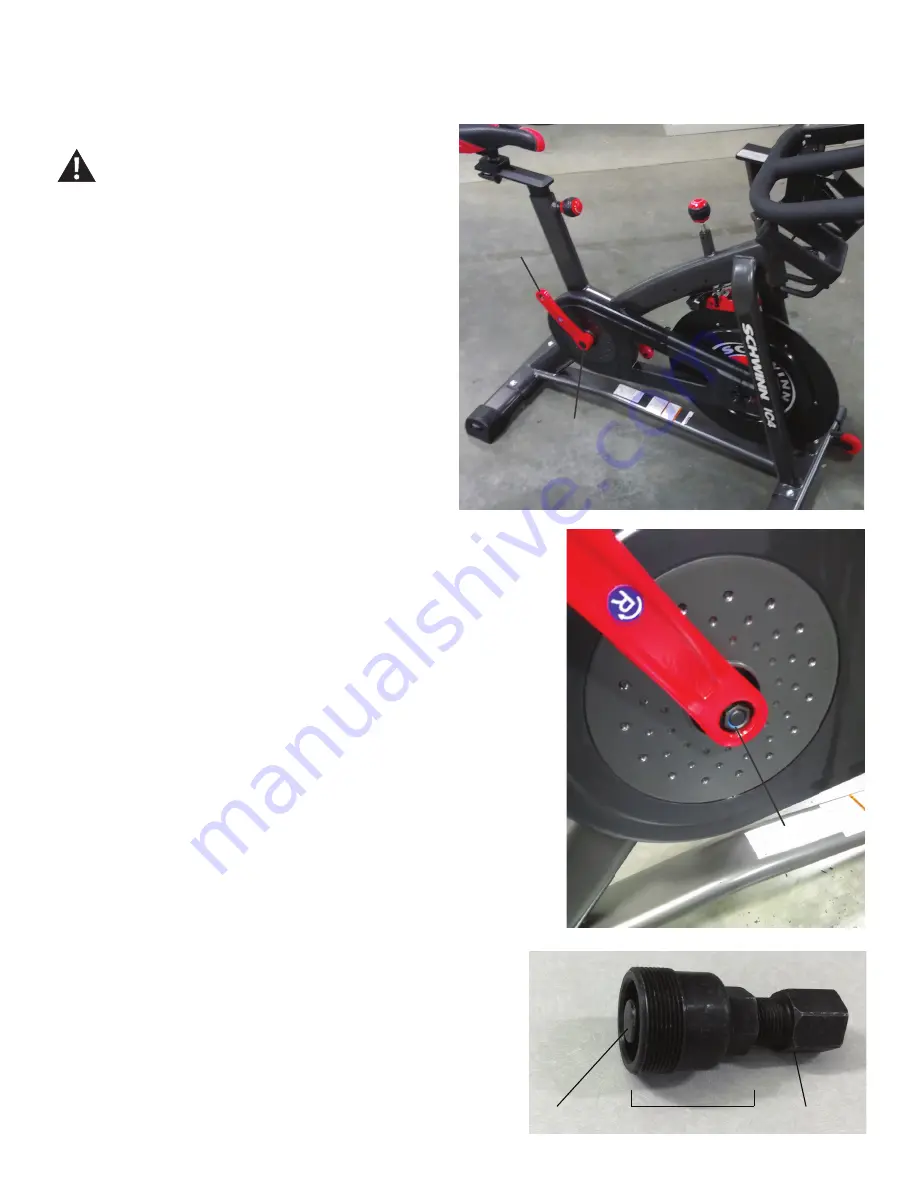
15
1.
Unplug the AC Adapter from the wall outlet and machine.
Keep the flywheel stable during this procedure. Do not
turn the crank arms. Flywheel movement can pull fingers
in and cause injury.
2.
To test the Drive Belt tension, sit on the bike and use the pedals
at approximately 20 RPM. Then accelerate quickly (speed burst) to
your maximum ability and feel whether the Drive Belt slips. If the pedals
move normally with no skipping (slip), the tension is correct.
If the tension is correct—got to step 14.
If the Drive Belt slips—continue to step 3.
3.
Using a flathead screwdriver, remove the threaded Cap from the
right Crank Arm.
4.
Using a 16mm socket and wrench, remove the Flange Nut under
the threaded Cap.
5.
Thread the Crank Puller into the Crank Arm When the Crank Puller
is in the correct position, only 1-2 threads on the outer portion (CP2) of
the Crank Puller should show.
Note:
Be sure the end of the Bolt (CP1) in the Crank Puller is flush
with the inner surface (CP2) as shown, before use.
6.
Using a 15mm wrench, turn the inner portion (CP3) of the Crank
Puller clockwise. The Crank Arm will slide off as it is tightened.
Note:
Your machine may not match the images provided exactly.
CP1
CP2
CP3
Cap
Crank Arm
Flange Nut