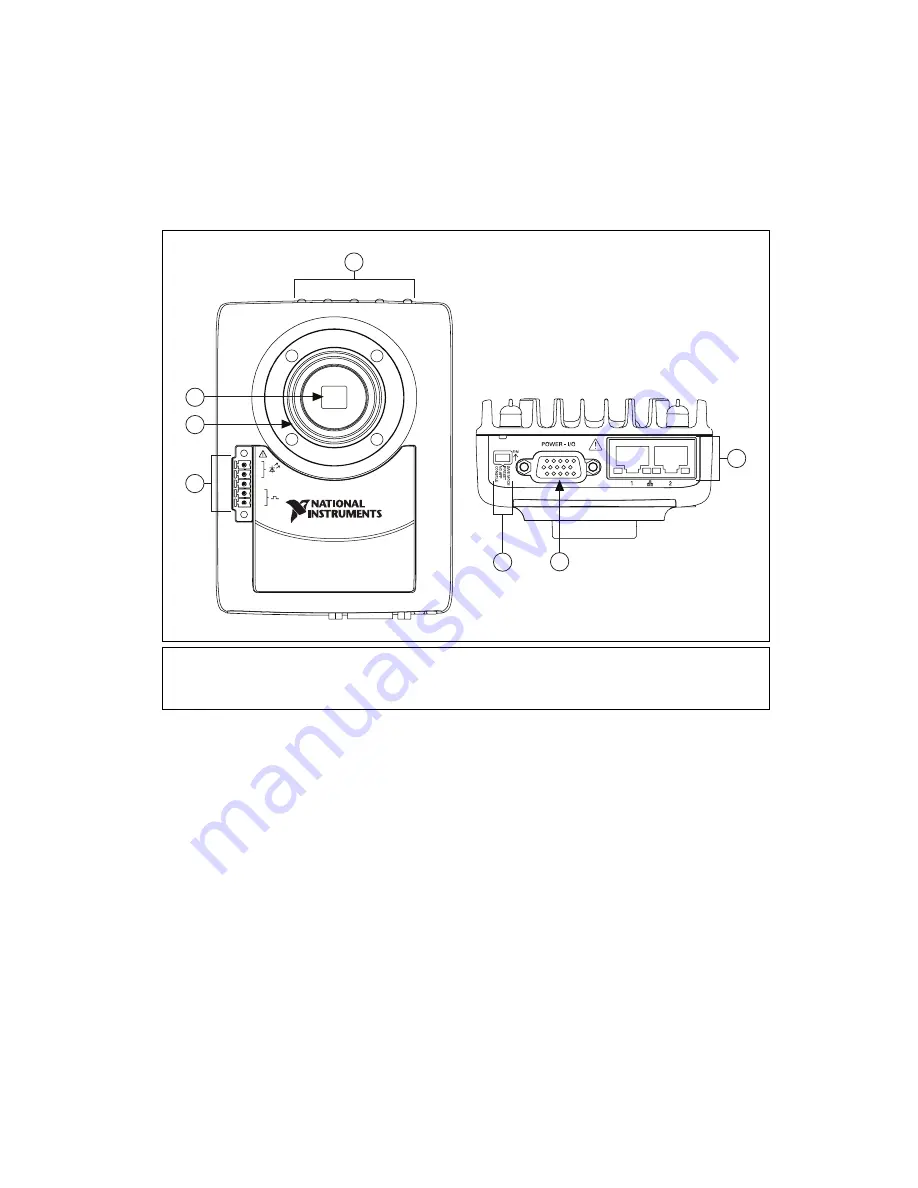
Chapter 1
NI Smart Camera Overview
©
National Instruments Corporation
1-3
NI 17xx Smart Camera User Manual
Figure 1-1 shows the smart camera.
Figure 1-1.
NI Smart Camera
1
Image Sensor
2
Standard C Lens Mount
3
Lighting Connector
4
LEDs
5
DIP Switches
6
POWER-I/O Connector
7
Ethernet Ports
GND
+
-
5V
24V
6
1
2
3
4
5
7
NI 17XX SMART CAMERA